10 Simple Steps to ISO 9001 Certification
10 Simple Steps to ISO 9001 Certification
If you’ve been thinking about getting your business ISO 9001 certified, you might feel like it’s a mountain to climb. The jargon, the requirements, the process—it can all seem a bit overwhelming at first. But what if I told you that achieving ISO 9001 certification doesn’t have to be so daunting? With the right plan, you can break it down into manageable chunks and get it done one step at a time.
That’s what this guide is all about. I’m here to walk you through the Steps to ISO 9001 Certification in a way that feels simple, practical, and achievable. Whether you’re running a small business or managing a larger organization, these steps will help you understand exactly what to do and how to do it.
ISO 9001 certification isn’t just about having a shiny badge to show off. It’s about building a stronger foundation for your business—one that helps you deliver consistent quality, keep customers happy, and create a more efficient operation. By the end of this article, you’ll see how these Steps to ISO 9001 Certification can transform your business for the better.
So, grab a cup of coffee, and let’s take this one step at a time. You’re closer to ISO 9001 certification than you think!
Why ISO 9001 Certification Matters
Before we dive into the specific Steps to ISO 9001 Certification, let’s take a moment to talk about why it’s worth pursuing in the first place. Whether you’re new to the idea of ISO 9001 or you’ve been considering certification for a while, understanding its value will make the process feel even more worthwhile.
What Is ISO 9001 Certification, and Why Should You Care?
ISO 9001 certification isn’t just a set of rules—it’s a globally recognized standard for quality management systems (QMS). It’s like a trusted blueprint for building a business that runs smoothly, delivers consistent quality, and keeps customers coming back for more.
But here’s the real magic: ISO 9001 certification doesn’t just benefit your customers. It helps your entire organization become more efficient, organized, and future-ready. When you follow the Steps to ISO 9001 Certification, you’re not just working toward a certificate—you’re building a better business.
What Makes ISO 9001 Certification So Valuable?
Think about it: in today’s competitive world, customers are spoiled for choice. They want to work with businesses they can trust—ones that prioritize quality and deliver on their promises. ISO 9001 certification is like a stamp of approval that tells customers, “We take quality seriously.”
But the benefits go beyond impressing your customers. By following the Steps to ISO 9001 Certification, you’ll see improvements in areas like:
- Efficiency: Streamlining processes means less wasted time and resources.
- Risk management: Spotting potential problems early saves you from costly mistakes.
- Team engagement: Clear systems and roles make life easier (and less stressful) for your employees.
- Reputation: Being ISO 9001 certified gives you a competitive edge in your industry.
Why Breaking It Down into Steps Makes All the Difference
If you’re feeling a little overwhelmed by the idea of ISO 9001 certification, don’t worry—you’re not alone. One of the most important things to remember is that the process doesn’t have to happen all at once. The key is to take it step by step.
That’s why this guide is here to help. By breaking the process into 10 simple Steps to ISO 9001 Certification, we’ll make sure you feel confident and in control every step of the way. Whether you’re starting from scratch or already have some systems in place, these steps will guide you toward success.
ISO 9001 certification isn’t just a box to tick—it’s a way to future-proof your business and show the world you’re serious about quality. Ready to dive into the process? Let’s start uncovering those 10 simple steps!
Step 1: Understand ISO 9001 Standards
Let’s kick things off with the first and arguably the most important step in your journey: understanding what ISO 9001 is all about. This might sound obvious, but trust me, diving into the details of the standard will set the stage for success. When you really understand the requirements, the rest of the Steps to ISO 9001 Certification will feel much easier to tackle.
What Is ISO 9001?
At its core, ISO 9001 is a set of guidelines for creating and maintaining a quality management system (QMS). It’s not a one-size-fits-all rulebook but rather a framework that you can adapt to your business’s unique needs. The standard focuses on things like meeting customer expectations, improving processes, and making decisions based on data.
Think of it like this: ISO 9001 gives you a roadmap for how to run your business more efficiently while delivering consistent quality. Understanding these principles will make the remaining Steps to ISO 9001 Certification feel less like a mystery and more like a well-planned journey.
How to Get Familiar with the Standard
So, how do you go about understanding ISO 9001? Start by reading the standard itself. You can purchase the official ISO 9001 document, which outlines all the requirements in detail. If that feels too technical, don’t worry—there are plenty of guides and resources that break it down into plain English.
One of the most important things to note is that ISO 9001 is based on several key principles, including:
- Customer focus
- Leadership
- Process approach
- Continuous improvement
Getting familiar with these principles will help you connect the dots as you move through the Steps to ISO 9001 Certification.
Why This Step Matters
Think of understanding ISO 9001 as the foundation for everything else. If you don’t know what’s required or how the standard works, the rest of the process might feel overwhelming. But when you’ve got a clear picture of what you’re working toward, you can approach the next steps with confidence.
This is why starting here is so crucial. The Steps to ISO 9001 Certification aren’t just about ticking boxes—they’re about creating a system that genuinely improves your business. And understanding the standard is your first big step in making that happen.
Take some time to get comfortable with ISO 9001. Whether you read the standard cover to cover, attend a training session, or dive into online resources, this step will set you up for success as you move forward. Ready for Step 2? Let’s keep going!
Step 2: Secure Management Buy-In
Now that you’ve got a solid understanding of what ISO 9001 is all about, the next step is to get your leadership team on board. This might sound straightforward, but it’s one of the most critical Steps to ISO 9001 Certification. Without strong support from management, the entire process can feel like pushing a boulder uphill. So, let’s talk about how to secure that all-important buy-in.
Why Management Buy-In Matters
Here’s the thing: ISO 9001 certification isn’t something you can achieve on your own. It requires resources, time, and company-wide commitment. That’s why it’s so important to have your leadership team fully invested in the process. When management believes in the value of ISO 9001, they’re more likely to provide the support and resources you need to succeed.
One of the key Steps to ISO 9001 Certification is ensuring that quality becomes a priority for the entire organization—not just a project for the quality team. This starts at the top. Leaders set the tone for the rest of the company, so their enthusiasm (or lack thereof) will have a ripple effect.
How to Get Leadership on Board
So, how do you convince management that ISO 9001 certification is worth pursuing? Start by clearly communicating the benefits. Here are some points to emphasize:
- Improved Efficiency: Explain how the certification process will streamline workflows and reduce waste, ultimately saving the company time and money.
- Customer Trust: Highlight how ISO 9001 certification builds credibility and attracts more customers.
- Competitive Advantage: Mention that being certified can open doors to new markets, contracts, and partnerships.
- Long-Term Growth: Stress that ISO 9001 creates a solid foundation for sustainable business growth.
Use real-life examples or case studies to illustrate these benefits. Showing how other companies have successfully implemented ISO 9001 can be a powerful motivator.
Involve Management in the Process
Here’s another important tip: don’t just ask for support—get management actively involved. Invite them to be part of key decisions, like setting goals or identifying areas for improvement. This gives them a sense of ownership and helps them see the value of ISO 9001 firsthand.
The Steps to ISO 9001 Certification aren’t just about checking boxes; they’re about building a culture of quality throughout the organization. When leaders are engaged, it’s much easier to get the rest of the team on board.
Address Concerns Head-On
It’s natural for leadership to have concerns about the time, cost, or complexity of certification. Be ready to address these head-on. For example, if they’re worried about the cost, explain how the efficiencies gained will offset the initial investment. If they’re concerned about time, reassure them that the process can be broken into manageable phases.
By being proactive and transparent, you’ll build trust and make it easier to secure their full support.
Why This Step Sets the Tone
Securing management buy-in isn’t just one of the Steps to ISO 9001 Certification—it’s the foundation for everything that follows. With leadership on board, you’ll have the resources, authority, and momentum you need to drive the process forward. And when the entire organization sees that quality is a top priority for management, it creates a culture of commitment and accountability.
So, don’t skip this step! Take the time to build a strong case and get your leadership team excited about the journey ahead. With their support, you’re already one big step closer to ISO 9001 certification. Ready for Step 3? Let’s keep the momentum going!
Step 3: Assemble Your Team
Now that your leadership is on board and excited about the journey, it’s time to gather the people who will help bring your vision to life. Assembling a strong team is one of the most important Steps to ISO 9001 Certification, and with the right people in place, the process will feel much more manageable. Let’s talk about how to create your dream ISO 9001 team!
Why You Need a Team for ISO 9001 Certification
Here’s the thing: ISO 9001 certification isn’t a one-person job. It involves reviewing processes, making improvements, training employees, and preparing for audits. Having a dedicated team ensures you’re spreading the workload across multiple shoulders rather than putting it all on one person.
Plus, ISO 9001 is about creating a system that works for the entire organization. By involving people from different departments, you’ll get valuable input, ensure everyone feels included, and create a system that truly reflects how your business operates. In short, assembling the right team is a crucial step toward successfully completing the Steps to ISO 9001 Certification.
Who Should Be on Your Team?
The size and makeup of your team will depend on your business, but here are a few key roles you might want to fill:
- Quality Manager or ISO 9001 Champion
This person will take the lead and act as the go-to expert for the certification process. They’ll keep the team on track, manage timelines, and ensure everything stays organized. - Department Representatives
Include people from various departments (like production, sales, customer service, and HR) to provide insights into how things work across the organization. - Documentation Specialist
ISO 9001 involves a lot of documentation, so having someone who can organize and manage these materials is a big plus. - Internal Auditor
Choose someone who can review your processes and identify areas that need improvement before the official certification audit.
By involving a mix of roles, you’ll have a well-rounded team that can tackle every aspect of the Steps to ISO 9001 Certification effectively.
How to Get Your Team Engaged
Building a team is one thing—getting them excited and engaged is another. Here are a few tips to keep the energy high:
- Explain the “Why”: Share the benefits of ISO 9001 certification and how it will help the business grow and succeed.
- Define Clear Roles: Let everyone know what’s expected of them so there’s no confusion about responsibilities.
- Provide Training: If team members aren’t familiar with ISO 9001, offer training or resources to bring them up to speed.
- Encourage Collaboration: Create an environment where team members feel comfortable sharing ideas and feedback.
One of the Steps to ISO 9001 Certification is ensuring that everyone is on the same page. When your team understands the goal and feels supported, they’ll be more motivated to contribute.
What If Your Team Is Small?
If you’re running a small business, you might not have the luxury of assembling a large team—and that’s okay! In that case, focus on assigning roles based on skillsets rather than departments. For example, one person might handle documentation while another takes the lead on training.
The key is to create a structure that works for your specific business. ISO 9001 is flexible, and so are the Steps to ISO 9001 Certification.
Why This Step Matters
Your team is the backbone of the entire ISO 9001 certification process. They’re the ones who will review processes, implement changes, and ensure everything is running smoothly. By assembling the right group of people, you’re setting yourself up for success.
So, take your time to choose wisely, get everyone involved, and create a collaborative environment. With a strong team by your side, you’re ready to move on to the next step. Let’s keep going—you’ve got this!
Step 4: Conduct a Gap Analysis
Now that you’ve assembled your team and laid the groundwork, it’s time to take an honest look at where your business stands. This is where a gap analysis comes in—and it’s one of the most important Steps to ISO 9001 Certification. Think of it as a “health check” for your current processes. It helps you identify what you’re already doing well and where you need to improve to meet ISO 9001 standards.
What Is a Gap Analysis?
A gap analysis is a systematic review of your current processes, systems, and documentation compared to the requirements of ISO 9001. It’s all about spotting the “gaps” between where you are now and where you need to be to achieve certification.
Here’s an analogy: if ISO 9001 certification is your destination, the gap analysis is your map. It shows you exactly how to get from Point A (your current state) to Point B (certification). By breaking things down into manageable pieces, this step makes the rest of the Steps to ISO 9001 Certification feel much less overwhelming.
How to Conduct a Gap Analysis
So, how do you get started? Follow these simple steps:
- Review the ISO 9001 Standard
Start by going through the requirements of ISO 9001. This will give you a clear picture of what’s expected. Don’t worry if it feels a bit technical—your team can work together to break it down into practical terms. - Examine Your Current Processes
Take a close look at your existing workflows, policies, and procedures. Are they documented? Are they consistent? Do they align with ISO 9001 principles like customer focus, leadership, and continuous improvement? - Identify Gaps
Compare your current processes to the ISO 9001 requirements. Are there areas where you’re falling short? For example, maybe you don’t have a formal process for gathering customer feedback, or perhaps your documentation is incomplete. - Prioritize Improvements
Once you’ve identified the gaps, rank them based on their importance. This will help you focus on the areas that need the most attention as you move forward with the Steps to ISO 9001 Certification.
Why a Gap Analysis Matters
The beauty of a gap analysis is that it gives you clarity. Instead of feeling like you’re navigating a maze, you’ll have a clear roadmap for what needs to be done. Plus, this step can save you time and resources by pinpointing exactly where to focus your efforts.
One of the key Steps to ISO 9001 Certification is understanding that you don’t have to fix everything overnight. A gap analysis helps you take a strategic approach, tackling the most critical areas first and building momentum as you go.
Tips for a Successful Gap Analysis
- Involve Your Team: Your team members are the ones who know your processes best. Involve them in the analysis to get a well-rounded view of how things work—and where they can improve.
- Stay Objective: Be honest about your current weaknesses. The goal isn’t to criticize but to identify opportunities for growth.
- Keep It Organized: Document your findings clearly so you can refer back to them as you move through the other Steps to ISO 9001 Certification.
What’s Next?
Now that you’ve completed your gap analysis, you’ve got a solid foundation for the next steps. You know what needs to change, where to focus your energy, and how to prioritize your efforts. This clarity will make the rest of the process much smoother and more efficient.
So, take a deep breath—you’re making real progress! With your roadmap in hand, you’re ready to move on to the next step. Let’s keep going and bring you closer to ISO 9001 certification!
Step 5: Create a Plan
Now that you’ve conducted a gap analysis and know exactly what needs to be done, it’s time to turn those insights into action. This is where creating a plan comes in, and trust me—it’s one of the most exciting Steps to ISO 9001 Certification because it’s all about mapping out how you’re going to achieve your goal. A good plan keeps you focused, organized, and on track as you work toward certification.
Why Creating a Plan Is Essential
Let’s face it—without a plan, things can get chaotic pretty quickly. ISO 9001 certification involves a lot of moving parts, and having a clear roadmap ensures nothing gets overlooked. Think of it as your personal guide to navigating the certification process step by step.
One of the most important Steps to ISO 9001 Certification is breaking the process into manageable tasks. A solid plan helps you prioritize improvements, set realistic deadlines, and allocate resources effectively. It’s like building a puzzle—piece by piece, it all comes together.
How to Build Your ISO 9001 Plan
Creating your plan doesn’t have to be complicated. Follow these simple steps to get started:
- Set Clear Objectives
Start by defining what you want to achieve with ISO 9001 certification. Is it about improving efficiency? Building customer trust? Expanding into new markets? Knowing your “why” will keep you motivated and help guide your decisions. - Prioritize the Gaps
Refer back to your gap analysis and identify the areas that need the most attention. For example, if documentation is a big gap, that might be one of your first priorities. Focus on what’s critical to meet the ISO 9001 requirements. - Break It Down into Tasks
Divide the work into smaller, actionable tasks. For instance:
- Document processes for customer feedback.
- Train employees on quality management principles.
- Conduct internal audits.
Each task should be specific and tied to a clear goal. - Assign Responsibilities
Delegate tasks to your team members based on their expertise and roles. This not only ensures accountability but also makes the workload more manageable. Remember, one of the key Steps to ISO 9001 Certification is involving your entire team. - Set a Timeline
Establish realistic deadlines for each task. Make sure your timeline gives you enough room to implement changes, train your team, and review progress without feeling rushed. - Track Progress
Use a simple tool like a spreadsheet or project management software to keep track of what’s been completed and what still needs work. Regular check-ins will help you stay on track and make adjustments as needed.
Tips for Success
- Start with Quick Wins: Focus on tasks that are easy to complete or will have the biggest impact first. This builds momentum and keeps your team motivated.
- Be Flexible: Your plan is a guide, not a rulebook. If something isn’t working or needs extra attention, don’t be afraid to adjust your approach.
- Celebrate Milestones: Completing the Steps to ISO 9001 Certification is a big deal! Celebrate small wins along the way to keep morale high.
Why This Step Makes All the Difference
Creating a plan isn’t just about getting organized—it’s about turning your vision into reality. This step transforms the overwhelming process of certification into something achievable and clear. By having a plan in place, you’ll feel confident knowing exactly what needs to happen and when.
Remember, the Steps to ISO 9001 Certification are a journey, not a sprint. Take it one task at a time, and before you know it, you’ll be well on your way to achieving certification. Ready for the next step? Let’s keep moving forward—you’re doing great!
Step 6: Document Your Processes
You’ve got your plan in place—great! Now, it’s time to roll up your sleeves and tackle one of the most important Steps to ISO 9001 Certification: documenting your processes. I know, I know—“documentation” might not sound like the most exciting part of the journey, but trust me, it’s a game-changer. Good documentation brings clarity, consistency, and structure to your business, and it’s an absolute must for ISO 9001 certification.
Why Documentation Is So Important
Think of documentation as the blueprint for how your business runs. It’s where you spell out your processes, policies, and procedures so everyone on your team knows exactly what to do and how to do it. Without clear documentation, things can get messy—confusion creeps in, mistakes happen, and quality suffers.
One of the key Steps to ISO 9001 Certification is making sure your processes are not only well-documented but also easy for your team to follow. Remember, the goal here isn’t to create mountains of paperwork—it’s to provide clear, concise instructions that improve consistency and efficiency.
What Needs to Be Documented?
ISO 9001 doesn’t require you to document everything, but there are certain key areas you’ll need to focus on, including:
- Your Quality Policy
This is a high-level statement that outlines your commitment to quality and continuous improvement. It sets the tone for your entire Quality Management System (QMS). - Your Objectives
Clearly define what you want to achieve with your QMS. For example, you might aim to improve customer satisfaction, reduce waste, or enhance efficiency. - Processes and Procedures
Document the key steps involved in your operations. For example:- How do you handle customer complaints?
- What’s your process for quality control?
- How do you gather and act on customer feedback?
- Roles and Responsibilities
Specify who’s responsible for what. This helps eliminate confusion and ensures accountability across your team. - Records Management
Detail how you’ll manage and store important records, such as audit reports, training logs, and quality control data.
These are just a few examples, but the idea is to create a clear roadmap for how your business operates—and how you ensure quality every step of the way.
How to Make Documentation Simple and Effective
Let’s be honest—no one loves dealing with endless forms and instructions. That’s why it’s important to keep your documentation simple, clear, and user-friendly. Here’s how:
- Use Plain Language: Avoid technical jargon or overly complex wording. The easier it is to understand, the better.
- Be Visual: Diagrams, flowcharts, and checklists can make your processes much easier to follow than walls of text.
- Focus on What Matters: Document only what’s necessary for your QMS and ISO 9001 requirements. Don’t get bogged down in unnecessary details.
- Involve Your Team: Your employees are the ones who will use these documents daily, so get their input to ensure everything makes sense.
By keeping things straightforward and practical, you’ll make this step of the Steps to ISO 9001 Certification much less intimidating—and much more effective.
How to Stay Organized
Good documentation is only useful if it’s easy to find and maintain. Consider using a centralized digital system to store and organize your documents. This makes updates simple and ensures everyone has access to the latest versions.
Pro tip: Create a version control system to keep track of changes. ISO 9001 requires you to manage document updates, so having a process for this will save you a lot of headaches.
Why This Step Builds Confidence
Documenting your processes isn’t just about meeting ISO 9001 requirements—it’s about creating clarity and consistency within your business. When your team has a clear guide to follow, they’ll feel more confident in their roles, and you’ll see improvements in efficiency and quality.
This is why documenting your processes is such a pivotal part of the Steps to ISO 9001 Certification. It sets the foundation for everything else, ensuring that your Quality Management System is solid, reliable, and ready for the certification audit.
So, grab a pen (or open that Word document) and get started! The more effort you put into this step, the smoother the rest of the process will be. Ready for the next step? Let’s keep building on this momentum—you’re doing amazing!
Step 7: Train Your Team
With your processes documented and your plan coming together, the next critical step is training your team. After all, a Quality Management System (QMS) is only as strong as the people who follow it. This is one of the most practical Steps to ISO 9001 Certification because it ensures your entire team understands their roles and responsibilities within the system. Let’s break it down.
Why Training Matters
Imagine rolling out new processes, but no one knows how to follow them. Frustrating, right? Training eliminates confusion and helps everyone understand how their work connects to the big picture. When your team is confident and informed, your QMS runs smoothly—and that’s a key requirement for ISO 9001 certification.
One of the Steps to ISO 9001 Certification is building a culture of quality. Training plays a huge role in this by showing your employees that quality isn’t just a “project”—it’s a way of working that benefits everyone, from the team on the ground to the customers you serve.
What Should Training Cover?
Training should be practical, relevant, and tailored to your team’s needs. Here are some key areas to focus on:
- ISO 9001 Basics
Give your team a quick overview of what ISO 9001 is, why it matters, and how it applies to your business. Keep it simple and relatable—no need to overwhelm them with technical jargon. - Roles and Responsibilities
Clearly explain what each team member’s role is within the QMS. For example:- Who’s responsible for documenting processes?
- Who handles customer feedback?
- Who ensures quality checks are completed?
- Process Changes
Walk your team through any new or updated processes. Show them how to follow the steps, answer questions, and address any concerns they might have. - Continuous Improvement
ISO 9001 is all about ongoing improvement, so encourage your team to share ideas for making processes even better. Training isn’t just about teaching—it’s also about listening and learning from your employees.
How to Deliver Effective Training
Training doesn’t have to be boring or overly complicated. Here are a few tips to make it engaging and effective:
- Keep It Hands-On: Let your team practice the processes they’ll be using day to day. For example, if you’re introducing a new way to handle customer complaints, run a mock scenario to help them get comfortable.
- Use Visuals: Diagrams, flowcharts, and videos can make complex processes easier to understand.
- Break It into Chunks: Instead of cramming everything into one long session, break training into smaller, focused sessions that are easier to digest.
- Encourage Questions: Create a safe space where employees feel comfortable asking questions or seeking clarification.
Remember, one of the Steps to ISO 9001 Certification is ensuring that your entire team is on board. Training is your chance to build that confidence and get everyone moving in the same direction.
How to Measure Training Success
Once your training sessions are complete, take a moment to evaluate how they went. Did your team seem engaged? Do they understand their roles? Are they confident in following the new processes?
You might also consider conducting a quick assessment or quiz to check understanding. Another idea is to hold follow-up sessions after a few weeks to address any new questions or challenges that arise. The goal is to make sure everyone feels supported as they adjust to the QMS.
Why This Step Sets You Up for Success
Training isn’t just a checkbox on your way to certification—it’s an investment in your team and your business. When everyone understands the QMS and their part in it, you’ll see fewer mistakes, smoother operations, and a stronger commitment to quality.
This step also reinforces one of the most important Steps to ISO 9001 Certification: collaboration. ISO 9001 isn’t something you do alone—it’s a team effort, and training ensures your team is ready to step up and succeed.
So, gather your team, create an engaging training plan, and get started! With this step under your belt, you’re building a solid foundation for the rest of your certification journey. Ready to keep going? Let’s dive into the next step together!
Step 8: Implement the System
Now that your team is trained and ready to go, it’s time to bring your Quality Management System (QMS) to life! This is where all the planning, documenting, and training come together. Implementing your system is one of the most exciting and rewarding Steps to ISO 9001 Certification because you finally get to see it in action. Let’s dive into what this step looks like and how to make it as smooth as possible.
What Does “Implementation” Mean?
Implementation is simply the process of putting your QMS into practice. It’s about turning your documented processes and procedures into everyday routines that your team follows consistently. Think of it like testing out a new recipe—you’ve got all the ingredients and instructions; now it’s time to cook!
This step isn’t just about following rules. One of the Steps to ISO 9001 Certification is creating a system that works for your business, so it should feel natural and aligned with your operations. The goal is to integrate the QMS into your daily activities so it becomes part of how your business runs—not an extra task on the to-do list.
How to Successfully Implement Your QMS
Here’s a simple game plan to get started:
- Start Small
You don’t have to roll out the entire QMS all at once. Begin with one department or process to test the waters. For example, you might start with how you handle customer feedback or quality control in production. This lets you iron out any wrinkles before scaling up. - Communicate Clearly
Make sure everyone understands what’s happening and why. Regular updates, team meetings, and open communication channels will help your team stay informed and engaged throughout the process. - Follow Your Documentation
Remember all those processes you documented in Step 6? Now’s the time to put them to use. Encourage your team to follow the steps exactly as outlined. If something doesn’t work as expected, note it for review and adjustment later. - Monitor Progress
Keep an eye on how things are going. Are employees following the processes? Are there any bottlenecks or challenges? Monitoring helps you catch issues early and make adjustments as needed. - Encourage Feedback
Your team is your best resource for identifying what’s working and what isn’t. Create a space where they feel comfortable sharing their experiences and suggestions for improvement.
Challenges You Might Face (and How to Overcome Them)
It’s normal to hit a few bumps during implementation. Here are some common challenges and how to handle them:
- Resistance to Change: Some team members might struggle to adapt to new processes. Be patient, offer support, and remind them of the benefits of ISO 9001 certification.
- Process Confusion: If employees are unsure about how to follow a process, provide additional training or clarify the documentation.
- Inconsistencies: If people are doing things differently, revisit the process and ensure everyone is on the same page.
Remember, one of the key Steps to ISO 9001 Certification is learning from these challenges and using them to improve your system.
How to Know Your System Is Working
A well-implemented QMS should make your business run more smoothly. You might notice fewer errors, improved efficiency, and a stronger focus on quality. But don’t worry if everything isn’t perfect right away—this is a learning process, and fine-tuning is part of the journey.
Use key performance indicators (KPIs) to measure your progress. For example:
- Are you meeting customer satisfaction goals?
- Have you reduced defects or complaints?
- Are processes being followed consistently?
Tracking these metrics will help you gauge how well your system is performing and identify areas for improvement.
Why Implementation Is a Game-Changer
This step is where your hard work starts to pay off. By putting your QMS into action, you’re taking a huge leap toward creating a more efficient, high-quality operation. It’s also one of the most pivotal Steps to ISO 9001 Certification because it sets the stage for the final steps, like audits and certification.
So, take a deep breath and dive in! Implementation might feel like a big step, but with the preparation you’ve done, you’re more than ready. Watch your QMS come to life and celebrate the progress you’re making. Ready for the next step? Let’s keep the momentum going!
Step 9: Conduct an Internal Audit
Congratulations—you’ve implemented your Quality Management System (QMS)! Now it’s time to take a closer look at how everything is working. Conducting an internal audit is one of the final Steps to ISO 9001 Certification, and it’s all about making sure your QMS is effective, compliant, and ready for the certification audit. Let’s dive into how to approach this step with confidence.
What Is an Internal Audit?
An internal audit is a self-check to see how well your QMS is performing and whether it meets the ISO 9001 requirements. Think of it like a dress rehearsal before the big performance—it’s your chance to spot any areas that need improvement and make adjustments before the official certification audit.
This step ensures that all the Steps to ISO 9001 Certification you’ve followed so far are working as intended. It’s not about pointing fingers or finding fault—it’s about continuous improvement and making sure you’re on the right track.
Why Internal Audits Are Important
Internal audits are a key part of the ISO 9001 process because they help you:
- Identify gaps or nonconformities in your system.
- Ensure that your processes are being followed consistently.
- Build confidence that your QMS is ready for the certification audit.
- Reinforce a culture of accountability and quality within your team.
One of the most valuable Steps to ISO 9001 Certification is learning from these audits and using the insights to refine your processes.
How to Conduct an Internal Audit
Internal audits don’t have to be intimidating. Here’s a step-by-step approach to make the process smooth and effective:
- Create an Audit Plan
Start by defining the scope of your audit. Which processes will you review? Who will be responsible for conducting the audit? Set clear objectives and create a schedule to keep things organized. - Choose Your Auditors
Select team members who understand the QMS but aren’t directly involved in the processes being audited. This ensures objectivity and provides a fresh perspective. - Gather Your Documentation
Before the audit, review the documentation for the processes you’ll be auditing. This includes procedures, policies, and any records that show how the processes are being followed. - Conduct the Audit
During the audit, compare what’s happening in practice to what’s documented. Are employees following the processes? Are records being kept as required? Look for any discrepancies or opportunities for improvement. - Record Findings
Document your observations, both good and bad. Highlight areas where the processes are working well and note any gaps or nonconformities that need to be addressed. - Report Results
Share your findings with your team and management. Be constructive—this is about improving, not assigning blame. Include actionable recommendations for addressing any issues. - Take Corrective Action
If you find gaps or nonconformities, create an action plan to resolve them. Follow up to ensure the corrective actions are implemented effectively.
Common Challenges and How to Overcome Them
- Feeling Overwhelmed: Break the audit into smaller sections and focus on one area at a time.
- Resistance from Team Members: Emphasize that the audit is about improving processes, not blaming individuals.
- Unclear Documentation: If your records are hard to follow, simplify them before conducting the audit.
One of the Steps to ISO 9001 Certification is creating a system that works for everyone, so use this opportunity to make things more efficient and user-friendly.
How Internal Audits Prepare You for Certification
Think of the internal audit as your chance to fine-tune your QMS. By identifying and addressing any gaps now, you’ll go into the certification audit feeling confident and prepared. It’s also a great way to build a culture of continuous improvement—one of the core principles of ISO 9001.
Why This Step Brings You Closer to Certification
Internal audits might seem like extra work, but they’re a crucial step in the process. They give you the opportunity to spot and fix issues before the certification audit, ensuring that your QMS meets the ISO 9001 requirements. Plus, they show your team and auditors that you’re serious about maintaining high standards.
This step is one of the final Steps to ISO 9001 Certification, and it’s a powerful way to ensure everything you’ve worked on so far is running smoothly. So, grab your audit checklist and get started—you’re almost there! Ready for the final step? Let’s finish strong!
Step 10: Schedule the Certification Audit
You’ve made it! After all the preparation, planning, and fine-tuning, you’re finally ready for the certification audit. This is the moment where everything you’ve worked toward comes together. Scheduling and preparing for the certification audit is the last of the Steps to ISO 9001 Certification, and it’s your chance to show off your Quality Management System (QMS). Let’s talk about how to approach this step with confidence.
What Is the Certification Audit?
The certification audit is the official review conducted by an accredited certification body to determine if your QMS meets the requirements of ISO 9001. Think of it like the final exam after a long semester—you’ve studied, you’ve practiced, and now it’s time to demonstrate what you’ve learned.
This audit typically happens in two stages:
- Stage 1 – Documentation Review: The auditor reviews your documentation to ensure it aligns with ISO 9001 requirements. This is where all the hard work you did in documenting your processes (Step 6) really pays off.
- Stage 2 – On-Site Audit: The auditor visits your workplace to assess how well your QMS is being implemented and followed in practice. They’ll check processes, talk to employees, and verify that everything is working as intended.
Completing this audit successfully is the final step in achieving certification. It’s the culmination of all the Steps to ISO 9001 Certification you’ve been working through.
How to Schedule the Certification Audit
Here’s how to get started with scheduling your audit:
- Choose a Certification Body
Research and select an accredited certification body that’s recognized in your industry. Look for one with a solid reputation and experience working with businesses like yours. - Plan Ahead
Certification bodies can get busy, so it’s a good idea to schedule your audit well in advance. This gives you plenty of time to prepare and ensures you’re not rushed. - Coordinate with Your Team
Let your team know the audit dates and what to expect. Everyone should be on the same page and ready to demonstrate their understanding of the QMS. - Confirm the Scope
Work with the certification body to confirm the scope of the audit. This includes which processes and locations will be reviewed.
By following these steps, you’re setting yourself up for a smooth and successful audit experience.
How to Prepare for the Audit
Preparation is key when it comes to the certification audit. Here are some tips to help you get ready:
- Review Your Documentation: Double-check that all your processes, procedures, and records are up to date and easily accessible.
- Conduct a Final Internal Audit: Use this as a last-minute rehearsal to make sure everything is running smoothly.
- Train Your Team: Remind employees about the key aspects of the QMS and encourage them to answer auditor questions honestly and confidently.
- Organize Your Workspace: A tidy, organized environment creates a positive impression and makes it easier for auditors to do their job.
Remember, one of the most important Steps to ISO 9001 Certification is staying calm and confident. You’ve done the work—now it’s time to show it off.
What to Expect During the Audit
During the audit, the auditor will:
- Review Your Documentation: They’ll check that your quality policy, objectives, and procedures align with ISO 9001 requirements.
- Observe Your Processes: The auditor will watch how your processes are carried out to ensure they match what’s documented.
- Talk to Your Team: Auditors often ask employees about their roles and how they follow the QMS. Encourage your team to answer honestly and explain things in their own words.
Auditors are there to evaluate your system, not to trip you up. If something isn’t perfect, they’ll provide feedback and guidance on how to improve.
Why This Step Is So Important
The certification audit is the final hurdle before achieving ISO 9001 certification. It validates all the hard work you’ve done and shows that your QMS meets international quality standards. It’s also a chance to learn—auditors often provide valuable insights that can help you fine-tune your system even further.
This step is the culmination of all the Steps to ISO 9001 Certification, and it’s a big milestone for your business. Passing the audit means you’ve joined the ranks of organizations that prioritize quality and continuous improvement.
What Happens After the Audit?
If you pass the audit, congratulations—you’re officially ISO 9001 certified! You’ll receive your certificate, which you can proudly display to show customers, partners, and stakeholders that you meet the gold standard for quality management.
If there are any nonconformities, don’t worry. You’ll have time to address them and schedule a follow-up audit. This is all part of the process, and it’s an opportunity to make your system even stronger.
Wrapping It All Up
Scheduling and preparing for the certification audit is the final and most exciting of the Steps to ISO 9001 Certification. It’s the moment where all your hard work pays off, and you take the final step toward building a stronger, more efficient, and more trusted business.
So, take a deep breath, trust in the system you’ve built, and embrace the process. You’re ready to cross the finish line—and the reward will be worth every bit of effort! Let’s celebrate this incredible achievement!
Looking for More Resources on ISO 9001?
Looking for ISO 9001 Resources Tailored to Your Industry?
If this article helped clarify ISO 9001, take the next step with our industry-focused tools designed to simplify your certification journey:
- ISO 9001 Documentation Kits by Industry: Whether you’re in manufacturing, construction, consulting, or healthcare — we have complete, ready-to-use documentation tailored for your sector.
- Online ISO 9001 Training: Learn how to implement ISO 9001 effectively with our easy-to-follow video lessons, real-world examples, and practical exercises.
- ISO 9001 Checklist: Download our step-by-step checklist to ensure your QMS meets all the 9001:2015 requirements from start to finish.
These resources are crafted to save you time, reduce stress, and help you achieve certification with confidence. Choose your industry and start now!
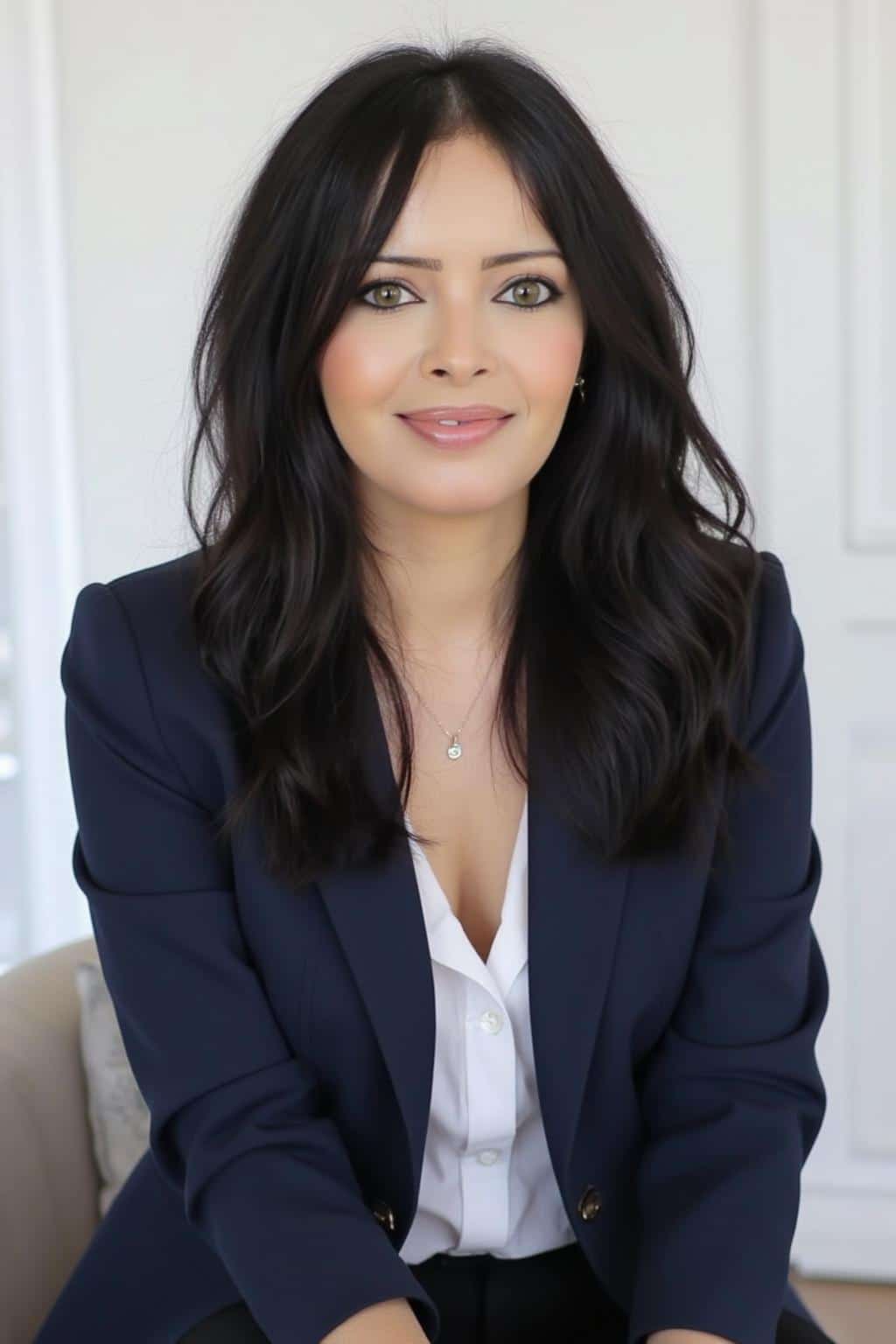
👋 Hi, I’m HAFSA, and for the past 12 years, I’ve been on a journey to
make ISO standards less intimidating and more approachable for everyone.
Whether it’s ISO 9001, ISO 22000, or the cosmetics-focused ISO 22716,
I’ve spent my career turning complex jargon into clear, actionable steps
that businesses can actually use. I’m not here to call myself an expert—I prefer “enthusiast” because I truly love what I do.
There’s something incredibly rewarding about helping people navigate food safety and quality management systems
in a way that feels simple, practical, and even enjoyable.
When I’m not writing about standards, you’ll probably find me playing Piano 🎹, connecting with people, or diving into my next big project💫.
I’m an engineer specialized in the food and agricultural industry
I have a Master’s in QHSE management and over 12 years of experience as a Quality Manager
I’ve helped more than 15 companies implement ISO 9001, ISO 22000, ISO 22716, GMP, and other standards
My clients include food producers, cosmetics manufacturers, laboratories, and service companies
I believe quality systems should be simple, useful, and efficient
Outside of work, I play piano and love learning something new every day
Let’s make ISO less about stress and more about success! 🙏