ISO 9001 Certification Process: A Step-by-Step Guide
ISO 9001 Certification Process: A Step-by-Step Guide
So, you’re thinking about getting ISO 9001 certified, but the whole ISO 9001 certification process feels like a big, complicated maze? Don’t worry—you’re not alone! Many quality managers and business owners hear about ISO 9001 and immediately picture piles of paperwork, endless audits, and a never-ending to-do list. But here’s the good news: the process isn’t as overwhelming as it seems when you break it down step by step.
In this guide, we’re going to walk through the ISO 9001 certification process in a way that actually makes sense—no jargon, no unnecessary complexity, just clear, actionable steps to help you achieve certification smoothly. Whether you’re a quality manager looking to streamline operations or a business owner wanting to boost customer confidence, this guide will make sure you understand what’s involved, why it matters, and how to succeed.
By the time you’re done reading, you’ll have a solid grasp of:
✔ What ISO 9001 certification really means and why it’s worth it.
✔ How to prepare for the ISO 9001 certification process without stress.
✔ The key steps, from setting up your Quality Management System (QMS) to passing your external audit.
✔ What happens after certification and how to maintain compliance with ease.
The best part? Getting certified isn’t just about earning a piece of paper—it’s about improving your business, building customer trust, and setting yourself apart from the competition. So, let’s dive in and break down the ISO 9001 certification process into simple, practical steps that anyone can follow.
Ready to get started? Let’s go!
Step 1: Understanding ISO 9001 and Its Benefits
Before jumping into the ISO 9001 certification process, let’s take a step back and make sure we understand what ISO 9001 is all about. After all, knowing why you’re doing something makes the journey a whole lot easier, right?
At its core, ISO 9001 is an internationally recognized standard for quality management. It’s designed to help businesses—big or small—improve efficiency, enhance customer satisfaction, and ensure that their products or services consistently meet high-quality standards. But here’s the real kicker: getting ISO 9001 certified isn’t just about meeting a set of rules. It’s about creating a structured, organized way of running your business that actually works and delivers real results.
Why Does ISO 9001 Matter?
Think about it: Have you ever experienced inconsistent service at a restaurant—one day everything is perfect, and the next time, it’s a mess? That’s what happens when businesses don’t have strong quality management processes in place. The ISO 9001 certification process helps companies avoid this by ensuring consistent quality, clear processes, and continuous improvement—no matter what industry they’re in.
For businesses, this means:
✔ Fewer mistakes, less waste – A well-structured QMS helps reduce errors and inefficiencies.
✔ Happier customers – Consistency and reliability lead to stronger customer trust.
✔ Stronger reputation – Being ISO 9001 certified makes you stand out in a crowded market.
✔ Better business opportunities – Many clients and partners prefer or even require their suppliers to be ISO 9001 certified.
How the ISO 9001 Certification Process Helps Your Business Grow
Some people think of ISO 9001 certification as just another box to tick, but it’s so much more than that. The ISO 9001 certification process pushes businesses to evaluate their workflows, identify weaknesses, and make meaningful improvements. It’s like giving your business a quality health check—spotting the gaps and fixing them before they become major issues.
And the best part? Once you’re through the ISO 9001 certification process, you’re not just holding a certificate—you’re holding a competitive advantage. You’re showing customers, investors, and partners that you take quality seriously and that your business is built on a solid, reliable foundation.
Now that you understand why ISO 9001 certification matters, let’s move on to the next step: getting ready for the process. Because trust me, a little preparation now will make the entire ISO 9001 certification process a whole lot smoother!
Step 2: Preparing for the ISO 9001 Certification Process
Alright, now that we’ve covered why ISO 9001 certification is important, it’s time to roll up our sleeves and get ready for the actual ISO 9001 certification process. Preparation is key here—think of it like training for a marathon. The better prepared you are, the smoother the journey will be.
So, what do you need to do before diving into the ISO 9001 certification process? Let’s break it down.
Assessing Your Readiness for ISO 9001 Certification
Before anything else, you need to figure out where your business currently stands in relation to ISO 9001 requirements. This is where a gap analysis comes in handy.
A gap analysis is like an ISO 9001 readiness check—it helps you compare your existing processes to the standard’s requirements and identify areas that need improvement. Some businesses already have solid quality management practices in place, while others may need to build their system from scratch. Either way, a gap analysis gives you a clear picture of what needs to be done before you officially start the ISO 9001 certification process.
Here’s what you should look at during this stage:
✔ Do you have clearly defined quality objectives?
✔ Are your processes well-documented and followed consistently?
✔ Do employees understand their roles in maintaining quality?
✔ Are there clear procedures for handling customer feedback and complaints?
If you answered “no” to any of these, don’t worry—that’s exactly why we’re going through the ISO 9001 certification process step by step!
Building Your ISO 9001 Implementation Team
You don’t have to tackle this alone! One of the best ways to ensure a smooth ISO 9001 certification process is to create an ISO 9001 implementation team. This team will be responsible for developing and maintaining the Quality Management System (QMS), coordinating training, and making sure everyone is on the same page.
Who should be on this team?
✔ Top management – They set the vision and provide resources.
✔ Process owners – These are the people who manage key operations daily.
✔ Quality representatives – Team members who understand ISO 9001 and can guide the process.
By having a dedicated team, you can ensure that the ISO 9001 certification process is well-organized, efficient, and supported across the company.
Training and Awareness: Getting Everyone On Board
Here’s a little secret: The success of your ISO 9001 certification process doesn’t just depend on leadership—it depends on everyone in the company. If your employees don’t understand ISO 9001 or why it matters, it will be much harder to implement effectively.
This is why ISO 9001 training is essential. Your team needs to know:
✔ What ISO 9001 certification is and why your company is pursuing it.
✔ How their daily tasks impact quality and compliance.
✔ What changes (if any) they need to make in their workflows.
You can provide training through:
📌 In-house training sessions led by your implementation team.
📌 External training programs or online courses.
📌 Hiring an ISO 9001 consultant to guide your team through the process.
The goal here isn’t just to check a training box—it’s to build a culture of quality. When employees see the value in ISO 9001 certification, they’ll be more engaged and committed to making it a success.
Setting a Timeline for Your ISO 9001 Certification Process
A common question at this stage is: How long does it take to get ISO 9001 certified? The truth is, it depends on your business size, current processes, and level of preparation. On average, the ISO 9001 certification process can take anywhere from 3 to 12 months.
To keep things on track, create a realistic timeline with clear milestones. Here’s a simple example:
📅 Month 1-2: Conduct gap analysis and form the implementation team.
📅 Month 3-4: Develop and document quality management processes.
📅 Month 5-6: Train employees and conduct internal audits.
📅 Month 7-8: Schedule and complete the certification audit.
Having a timeline ensures you stay focused and don’t get stuck in “we’ll do it later” mode.
Final Thoughts Before Moving Forward
Now that you’ve laid the groundwork, you’re ready to start implementing your Quality Management System (QMS)—the backbone of the ISO 9001 certification process. This is where you’ll develop structured processes, document workflows, and ensure that everything aligns with ISO 9001 standards.
It might feel like a lot, but trust me—taking the time to prepare now will make the rest of the ISO 9001 certification process much easier. So, let’s move on to the next step: Building a QMS that meets ISO 9001 requirements!
Step 3: Implementing a Quality Management System (QMS)
Now that you’ve laid the groundwork, it’s time to build the foundation of your ISO 9001 certification process—your Quality Management System (QMS). Think of your QMS as the blueprint for how your company operates, ensuring consistency, efficiency, and quality in everything you do. Without a well-structured QMS, achieving ISO 9001 certification would be like trying to bake a cake without a recipe—it might turn out okay, but it’s a lot harder than it needs to be!
So, what exactly goes into a QMS that meets ISO 9001 standards? Let’s break it down into simple, actionable steps.
Developing ISO 9001-Compliant Processes and Policies
A big part of the ISO 9001 certification process is documenting your company’s processes. Why? Because ISO 9001 is all about consistency. When your processes are clearly defined and followed by everyone, you reduce mistakes, improve efficiency, and keep customers happy.
Here’s what you need to focus on:
✔ Defining key processes – Identify the essential workflows in your business, from order management to product/service delivery.
✔ Documenting procedures – Write down the “how-to” for each process in a way that’s easy to follow.
✔ Creating a quality policy – This is your company’s commitment to quality and continuous improvement.
✔ Setting measurable quality objectives – What are your company’s goals for improving quality and efficiency?
Your documentation doesn’t have to be overwhelming—it just needs to be clear enough that anyone in your company can follow it without confusion.
Making Sure Your QMS Works in Practice
It’s one thing to create a bunch of policies and procedures, but the real question is: do they work in real life? The best way to ensure your QMS is effective is to test it out in daily operations.
Here’s how you can do that:
📌 Walk through your processes – Observe how tasks are performed and make sure they align with your documented procedures.
📌 Get feedback from employees – Your team works with these processes every day—if something doesn’t make sense, they’ll know!
📌 Look for inefficiencies – Are there unnecessary steps? Any bottlenecks that slow things down? Adjust as needed.
Remember, the ISO 9001 certification process isn’t about making things harder for your team—it’s about improving how your business runs. If a process feels too complicated, simplify it!
Risk-Based Thinking: Identifying and Preventing Problems
One of the key principles of ISO 9001 is risk-based thinking. Instead of just reacting to problems after they happen, ISO 9001 encourages businesses to identify risks in advance and put controls in place to prevent them.
Here’s how you can apply this to your QMS:
✔ Identify potential risks – What could go wrong in your processes? Think about supply chain issues, product defects, service delays, or miscommunication with customers.
✔ Develop preventive actions – What steps can you take to reduce these risks? This could include quality checks, training programs, or better supplier management.
✔ Monitor and adjust – Keep track of how well your risk controls are working and make improvements over time.
By integrating risk-based thinking into your QMS, you’re not just meeting an ISO requirement—you’re making your business stronger and more resilient.
Involving Employees in the ISO 9001 Certification Process
Here’s something a lot of businesses overlook: Your employees play a huge role in making your QMS work. Even the best-designed system won’t succeed if your team isn’t on board.
How can you get your employees engaged in the ISO 9001 certification process?
✔ Explain the “why” behind ISO 9001 – When people understand how ISO 9001 benefits them (fewer errors, smoother workflows, better customer feedback), they’re more likely to embrace it.
✔ Provide hands-on training – Show employees how to use the QMS in their daily tasks. Make training interactive and practical.
✔ Encourage feedback – Your team members are the ones using these processes daily. Listen to their insights and make improvements where needed.
Remember, ISO 9001 isn’t just about meeting requirements—it’s about creating a culture of quality. When employees feel involved, they’re more likely to support the process and take ownership of their roles.
Final Check: Is Your QMS Ready for an Audit?
Before moving forward in the ISO 9001 certification process, do a quick self-check to ensure your QMS is solid:
✅ Are all key processes documented and easy to follow?
✅ Do employees understand their roles and responsibilities in maintaining quality?
✅ Have you identified and addressed potential risks?
✅ Are you tracking and measuring quality objectives?
If you can confidently answer “yes” to these questions, you’re ready for the next big step: the internal audit. This is where you’ll test your QMS, find any weak spots, and make improvements before the official certification audit.
In the next section, we’ll dive into the internal audit process and how to make sure your business is fully prepared for certification. Stay tuned—you’re getting closer to achieving your ISO 9001 certification!
Step 4: Conducting an Internal Audit – A Critical Step in the ISO 9001 Certification Process
You’ve put in the work—your Quality Management System (QMS) is in place, your processes are documented, and your team is on board. Now, it’s time to test how well everything is working before the official certification audit. This is where the internal audit comes in—a crucial step in the ISO 9001 certification process that helps you identify and fix any weak spots before the external auditor does.
Think of an internal audit like a dress rehearsal before a big performance. You get a chance to spot mistakes, make improvements, and ensure everything is running smoothly before the real test. So, let’s break down what an internal audit involves and how you can conduct one effectively.
Why Internal Audits Are a Must in the ISO 9001 Certification Process
Some businesses make the mistake of seeing an internal audit as just another checkbox on the road to certification. But in reality, this step can make or break your success in the ISO 9001 certification process. Here’s why:
✔ It helps you catch non-conformities early – Finding gaps in your processes before the certification audit saves you from last-minute stress.
✔ It prepares your team – Employees get familiar with the audit process, so they’re more confident when the external auditor arrives.
✔ It builds a culture of continuous improvement – Instead of viewing audits as “trouble-finding” exercises, teams start seeing them as tools for growth.
The goal isn’t to “pass” the internal audit—it’s to find ways to improve before the official ISO 9001 certification audit.
How to Conduct an Effective Internal Audit
A successful internal audit follows a structured approach. Here’s a simple, step-by-step guide:
1. Plan Your Internal Audit
Before you start, you need a solid plan. Decide:
📌 What will be audited? Focus on key processes required by ISO 9001.
📌 Who will conduct the audit? Ideally, internal auditors should be trained and objective—meaning they shouldn’t audit their own department.
📌 When will it happen? Schedule the audit at least a few weeks before the external audit so you have time to fix any issues.
2. Use an ISO 9001 Audit Checklist
To make things easier, create an ISO 9001 internal audit checklist. This checklist should cover all essential areas, such as:
✅ Are all processes documented and being followed?
✅ Are employees aware of quality policies and objectives?
✅ Is customer feedback being collected and acted upon?
✅ Are non-conformities from previous audits resolved?
Having a checklist keeps the audit structured and ensures you don’t overlook important areas.
3. Conduct the Audit and Gather Evidence
Now, it’s time to dive in! During the internal audit:
✔ Review documentation and records—are they up to date and accurate?
✔ Observe processes in action—are employees following procedures correctly?
✔ Interview team members—do they understand their roles in maintaining quality?
Collect evidence, take notes, and highlight any non-conformities or areas for improvement.
4. Report the Findings
After the audit, compile your findings into a clear, actionable report. Your internal audit report should include:
📌 What’s working well – Acknowledge processes that meet ISO 9001 standards.
📌 What needs improvement – List any non-conformities and areas that need attention.
📌 Recommended corrective actions – Provide solutions to address any issues found.
5. Take Corrective Action and Improve Processes
Finding gaps in your QMS isn’t a bad thing—it’s an opportunity to make improvements! Once the audit is complete, take action by:
✔ Fixing non-conformities identified during the audit.
✔ Updating procedures or documentation as needed.
✔ Providing additional training if employees need better guidance.
By addressing these issues before the external certification audit, you’re setting yourself up for success in the ISO 9001 certification process.
What Happens After the Internal Audit?
Once you’ve made all the necessary improvements, you’re almost at the finish line! The next step is the certification audit, where an external auditor will review your QMS to determine if your business meets ISO 9001 requirements.
Feeling nervous? Don’t be! If you’ve done a thorough internal audit and taken corrective actions, you’ll be well-prepared for the real thing. Think of it this way—your internal audit has already helped you iron out any wrinkles, so now it’s just about showcasing the great work you’ve done.
In the next section, we’ll go over what to expect during the certification audit and how to make sure your business is ready to get officially certified. You’re almost there—keep going!
Step 5: The Certification Audit – The Final Step
Congratulations! You’ve done the hard work—your Quality Management System (QMS) is in place, you’ve conducted an internal audit, and you’ve made the necessary improvements. Now, it’s time for the big moment: the certification audit. This is the final hurdle in the ISO 9001 certification process, where an external auditor evaluates your QMS to determine if your business meets the ISO 9001 requirements.
Feeling a little nervous? That’s completely normal! But don’t worry—if you’ve followed the process step by step, you’re already in great shape. Let’s go over what to expect and how to make sure you’re fully prepared for your ISO 9001 certification audit.
Understanding the Certification Audit Process
The ISO 9001 certification process includes two main stages of auditing:
Stage 1: Documentation Review (Preliminary Audit)
This is a desk audit where the certification body’s auditor reviews your documentation to ensure it meets ISO 9001 standards. The goal here is to confirm that your QMS is properly documented before they conduct the full assessment.
What happens during Stage 1?
✔ The auditor reviews your Quality Manual, policies, and procedures.
✔ They check if your processes align with ISO 9001 requirements.
✔ You’ll receive feedback on any missing elements that need fixing before Stage 2.
If any gaps are found, don’t panic! The auditor will give you time to correct them before moving forward to the next stage.
Stage 2: On-Site Certification Audit
This is the big one! In Stage 2, an external auditor visits your business to assess how well your QMS is implemented. They will:
✔ Observe real-life processes to see if they match your documented procedures.
✔ Interview employees to check their understanding of ISO 9001 and quality policies.
✔ Look at records, reports, and corrective actions to ensure compliance.
✔ Identify any non-conformities that need fixing before certification can be granted.
At the end of the audit, you’ll receive an audit report. If there are minor non-conformities, you’ll need to correct them within a set timeframe before certification is issued. If there are major non-conformities, a follow-up audit may be required.
How to Prepare for the Certification Audit
Want to make sure your ISO 9001 certification process goes smoothly? Follow these simple steps:
1. Review Your Documentation One Last Time
Make sure all policies, procedures, and records are up to date and easily accessible. The auditor will want to see evidence that your QMS is well-documented and followed consistently.
2. Train Your Employees on ISO 9001 Requirements
The auditor will likely ask employees questions about their roles in maintaining quality. Everyone should have a basic understanding of:
✔ Your company’s quality policy and objectives.
✔ How their daily tasks contribute to meeting ISO 9001 standards.
✔ What to do if a problem or non-conformity arises.
Tip: Hold a quick refresher meeting before the audit to ensure everyone feels confident!
3. Conduct a Final Internal Audit or Mock Audit
This is your chance to spot and fix any last-minute issues before the external auditor arrives. A mock audit simulates the real thing, helping your team get comfortable with the process.
4. Be Transparent and Organized During the Audit
Auditors appreciate honesty and cooperation. If an issue is found, don’t try to hide it—show that you’re proactive about making improvements. Have your QMS documents, audit reports, and corrective actions ready to present when requested.
What Happens After the Certification Audit?
Once the ISO 9001 certification process is complete, there are three possible outcomes:
✅ Full Certification – If your business meets all ISO 9001 requirements with no major issues, you’ll receive your ISO 9001 certification, typically valid for three years.
🛠 Corrective Actions Required – If minor non-conformities are found, you’ll need to fix them and submit evidence of corrective actions before certification is issued.
🔄 Follow-Up Audit Needed – If major non-conformities are identified, you may need a re-audit before certification can be granted.
Once certified, you’ll officially be recognized as an ISO 9001-certified company, proving to customers, partners, and stakeholders that your business meets international quality standards!
Final Thoughts: You’re Almost There!
The ISO 9001 certification process may seem complex, but each step is designed to help your business operate more efficiently and consistently. If you’ve prepared well, the certification audit is just a final confirmation of the great work you’ve already done.
Now that you’re on your way to certification, what’s next? In the final section, we’ll cover how to maintain your ISO 9001 certification and keep your business compliant for years to come. Stay tuned—you’re about to cross the finish line!
Step 6: Maintaining Compliance After the ISO 9001 Certification
You did it! 🎉 Your business has successfully completed the ISO 9001 certification process, and you’re officially ISO 9001 certified. But before you kick back and celebrate too much, there’s one important thing to remember—certification isn’t the finish line, it’s just the beginning.
Maintaining your ISO 9001 certification requires ongoing effort to ensure your Quality Management System (QMS) continues to meet the standard’s requirements. If you don’t keep up with compliance, your certification can be at risk when it’s time for surveillance or recertification audits.
But don’t worry! Keeping your certification active doesn’t have to be overwhelming. In fact, when done right, it can help your business continuously improve, stay ahead of competitors, and enhance customer satisfaction. Let’s go over how to maintain your certification with confidence.
Surveillance Audits: What You Need to Know
Once your business is certified, your certification body will conduct annual surveillance audits to ensure your QMS is still compliant. These audits aren’t as extensive as the initial certification audit, but they’re still important.
What Happens During a Surveillance Audit?
✔ The auditor checks if you’re following your QMS as documented.
✔ They review corrective actions from previous audits.
✔ They assess if your processes are still meeting ISO 9001 requirements.
✔ They may identify new areas for improvement.
Think of these audits as a regular quality check-up. Just like you wouldn’t ignore maintenance on a car after buying it, you shouldn’t ignore ongoing compliance after completing the ISO 9001 certification process.
Keeping a Culture of Continuous Improvement
One of the biggest advantages of the ISO 9001 certification process is that it helps businesses adopt a continuous improvement mindset. Instead of just doing the bare minimum to stay certified, use ISO 9001 as a tool to make your company better every day.
Here’s how:
✔ Regular Internal Audits – Don’t wait for the external auditors to find issues—conduct internal audits at least once a year to catch and fix problems early.
✔ Employee Training & Engagement – Keep your team involved by offering refresher training on ISO 9001 best practices. A well-trained team means fewer compliance headaches!
✔ Monitor Key Performance Indicators (KPIs) – Track your quality objectives and make sure your processes are still meeting business goals.
✔ Encourage Feedback – Whether it’s from employees or customers, feedback is a goldmine for improvement. Listen, learn, and take action!
The more you integrate ISO 9001 principles into your everyday operations, the easier it will be to maintain compliance and keep growing.
Preparing for Recertification: The Three-Year Cycle
Your ISO 9001 certification isn’t valid forever. Most certificates are issued for three years, and before it expires, you’ll need to undergo a recertification audit. This audit is similar to the initial certification audit but focuses on how well you’ve maintained your QMS over time.
How to Get Ready for Recertification?
📌 Keep up with regular internal audits to ensure ongoing compliance.
📌 Address any issues found during surveillance audits immediately.
📌 Maintain proper documentation of corrective actions, quality objectives, and process improvements.
📌 Make sure employees remain engaged and aware of their ISO 9001 responsibilities.
When recertification time comes, businesses that have actively maintained their ISO 9001 system will have a smooth experience. Those that have neglected it, however, might struggle to keep their certification.
Final Thoughts: ISO 9001 is a Long-Term Commitment to Quality
The ISO 9001 certification process isn’t just about getting a certificate to hang on the wall—it’s about building a business that consistently delivers quality, efficiency, and customer satisfaction.
By maintaining compliance, embracing continuous improvement, and preparing for audits in advance, your business can not only keep its ISO 9001 certification but also thrive in a competitive market.
So, what’s next? Take what you’ve learned and make ISO 9001 part of your company’s DNA. Keep improving, keep innovating, and watch as your commitment to quality takes your business to new heights.
Want to learn more or need help with maintaining your ISO 9001 certification? Let’s keep the conversation going—quality management is a journey, and you’re on the right path!
Conclusion: Embracing the ISO 9001 Certification Process for Long-Term Success
And there you have it! We’ve walked through every step of the ISO 9001 certification process, from preparation to implementation, audits, and ongoing compliance. If you’ve made it this far, you now have a clear roadmap for getting ISO 9001 certified and maintaining your certification for years to come.
At first glance, the ISO 9001 certification process might seem overwhelming, but when broken down step by step, it’s actually a structured, logical approach to building a better, more efficient business. Whether you’re a quality manager ensuring compliance or a business owner looking to gain a competitive edge, following this process will help you create a system that delivers consistent quality, customer satisfaction, and operational improvements.
Why the ISO 9001 Certification Process is Worth It
Still wondering if the effort is worth it? Let’s take a moment to reflect on the benefits of completing the ISO 9001 certification process:
✔ Stronger Customer Trust – Being ISO 9001 certified tells customers that your business is committed to quality and reliability.
✔ More Business Opportunities – Many organizations prefer or require their suppliers to be ISO 9001 certified, giving you an advantage in contracts and partnerships.
✔ Improved Efficiency – Streamlined processes mean fewer mistakes, less waste, and better productivity.
✔ Continuous Improvement – The ISO 9001 framework encourages businesses to keep evolving and getting better over time.
Sure, achieving certification takes time and effort, but the long-term rewards far outweigh the initial work. Businesses that embrace the ISO 9001 certification process don’t just meet a standard—they set themselves apart as industry leaders.
Final Thoughts: Taking the First Step
If you’re ready to start your journey, remember: the best way to tackle the ISO 9001 certification process is one step at a time. Begin with a gap analysis, build your Quality Management System (QMS), and involve your team in the process. With the right approach, achieving and maintaining your ISO 9001 certification will feel less like a daunting task and more like a natural progression toward business excellence.
So, what’s your next move? Whether you’re just starting out or preparing for an audit, take action today and set your business up for success. The ISO 9001 certification process isn’t just about getting a certificate—it’s about creating a stronger, more efficient company that delivers top-notch quality every single time.
Ready to take the first step? Let’s make it happen!
Looking for More Resources on ISO 9001?
Looking for ISO 9001 Resources Tailored to Your Industry?
If this article helped clarify ISO 9001, take the next step with our industry-focused tools designed to simplify your certification journey:
📦 ISO 9001 Documentation Kits by Industry: Whether you’re in manufacturing, construction, consulting, or healthcare — we have complete, ready-to-use documentation tailored for your sector.
🎓 Online ISO 9001 Training: Learn how to implement ISO 9001 effectively with our easy-to-follow video lessons, real-world examples, and practical exercises.
📋 ISO 9001 Checklist: Download our step-by-step checklist to ensure your QMS meets all the 9001:2015 requirements from start to finish.
These resources are crafted to save you time, reduce stress, and help you achieve certification with confidence. Choose your industry and start now!
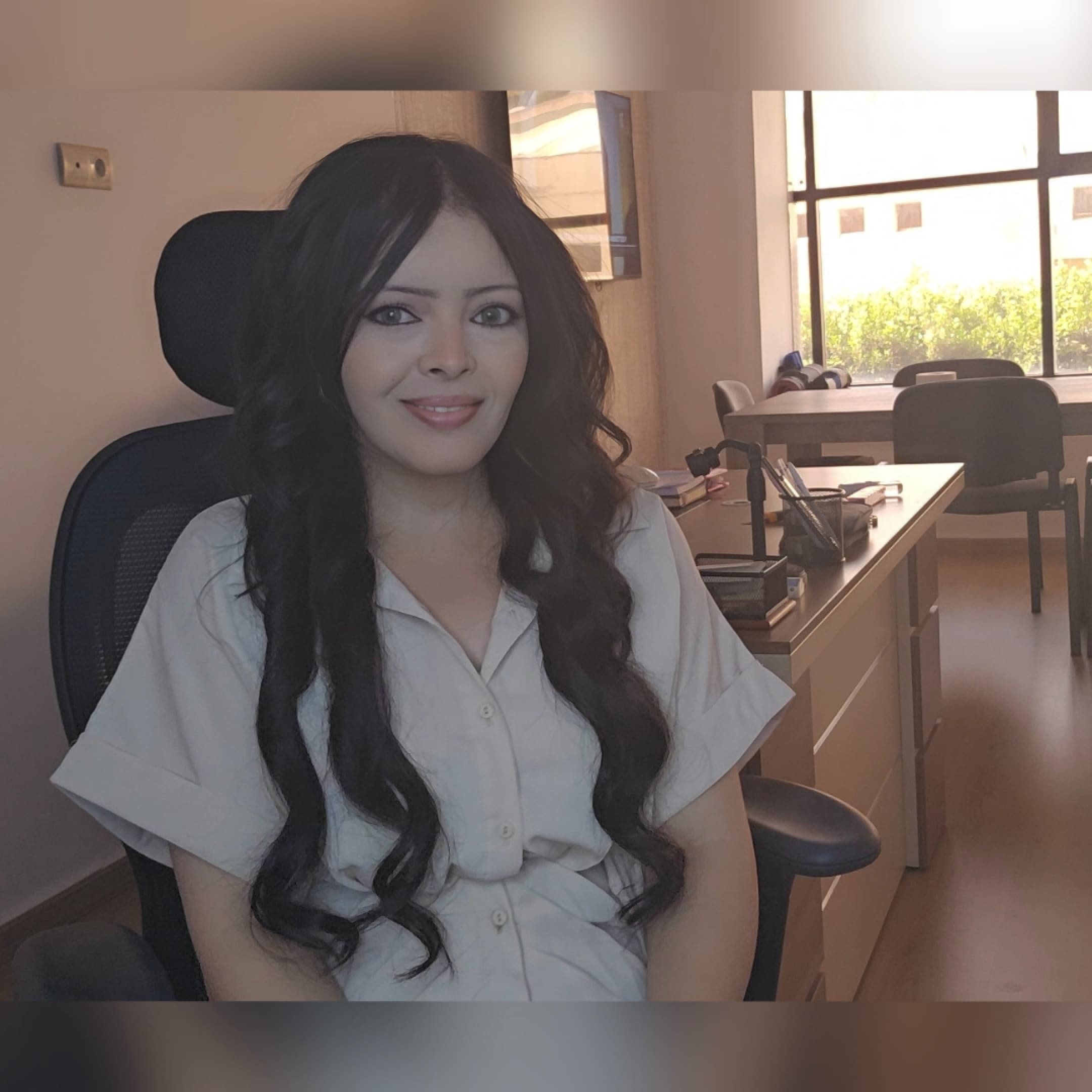
make ISO standards less intimidating and more approachable for everyone.
Whether it’s ISO 9001, ISO 22000, or the cosmetics-focused ISO 22716,
I’ve spent my career turning complex jargon into clear, actionable steps
that businesses can actually use. I’m not here to call myself an expert—I prefer “enthusiast” because I truly love what I do.
There’s something incredibly rewarding about helping people navigate food safety and quality management systems
in a way that feels simple, practical, and even enjoyable.
When I’m not writing about standards, you’ll probably find me playing Piano 🎹, connecting with people, or diving into my next big project💫.
- I’m an engineer specialized in the food and agricultural industry
- I have a Master’s in QHSE management and over 12 years of experience as a Quality Manager
- I’ve helped more than 15 companies implement ISO 9001, ISO 22000, ISO 22716, GMP, and other standards
- My clients include food producers, cosmetics manufacturers, laboratories, and service companies
- I believe quality systems should be simple, useful, and efficient
- Outside of work, I play piano and love learning something new every day
Let’s make ISO less about stress and more about success! 🙏