Cost of ISO 9001 Certification
Last Updated on July 2, 2025 by Melissa Lazaro
Cost of ISO 9001 Certification: What You Need to Know
Have you ever wondered what it would take to get your business ISO 9001 certified? More importantly, have you asked yourself how much it’s going to cost? The Cost of ISO 9001 Certification is one of the most common questions businesses have when considering this important step toward improving quality and customer satisfaction. And it’s a great question!
The truth is, the cost isn’t one-size-fits-all—it depends on factors like the size of your business, the complexity of your operations, and how much of your current processes align with ISO 9001 standards. But here’s the thing: the Cost of ISO 9001 Certification is not just an expense; it’s an investment in your business’s growth, efficiency, and reputation.
In this article, we’re going to break down the costs involved, explore what influences the price, and show you how to get the most value from the process. If you’ve been curious about ISO 9001 but held back because of the price tag, you’re in the right place. Let’s dive in and explore whether the Cost of ISO 9001 Certification is worth it for your business!
Why ISO 9001 Certification is Worth Considering
When thinking about the Cost of ISO 9001 Certification, it’s easy to focus on the price tag and wonder, “Is this really worth it?” The short answer? Absolutely. While there’s an upfront cost involved, the value ISO 9001 brings to your business far outweighs the initial investment. Let’s take a closer look at why ISO 9001 certification is something every organization should seriously consider.
The Value of Certification
ISO 9001 certification isn’t just a fancy piece of paper to hang on your office wall—it’s a globally recognized mark of quality. When customers see that you’re ISO 9001 certified, they immediately know your business is committed to high standards. This level of credibility can open doors to new opportunities, such as bigger contracts, partnerships, and loyal customers who trust your brand.
Example:
Imagine you’re a small manufacturing company bidding on a contract with a major retailer. If your competitor isn’t ISO certified but you are, that certification can give you the edge. The Cost of ISO 9001 Certification in this case becomes an investment in winning valuable new business.
Long-Term Benefits vs. Initial Costs
Yes, the Cost of ISO 9001 Certification requires some upfront planning and spending, but think of it like upgrading your car’s engine—it may take some work now, but it’ll run smoother and save you money in the long run. Certification often leads to improved efficiency, reduced waste, and happier customers, which can all boost your bottom line.
How It Helps:
- Efficiency Gains: By streamlining processes, you save time and money.
- Reduced Errors: A solid quality management system (QMS) minimizes costly mistakes.
- Customer Retention: Consistently delivering quality keeps customers coming back.
The upfront Cost of ISO 9001 Certification starts to look much smaller when you realize how much you’re saving and earning over time.
Building a Competitive Edge
In today’s market, standing out can be tough. But ISO 9001 certification is a clear way to show that your business is serious about quality and customer satisfaction. Many companies require ISO certification as a prerequisite to doing business with them. Without it, you might miss out on significant opportunities.
Example:
A logistics company might invest in ISO 9001 certification to secure contracts with international clients who prioritize suppliers with certified quality standards. In this case, the Cost of ISO 9001 Certification isn’t just an expense—it’s the key to accessing bigger markets.
Why It’s Worth It
Ultimately, the Cost of ISO 9001 Certification isn’t just about money—it’s about the value you’re adding to your business. From building trust with customers to improving internal processes, certification delivers benefits that far outweigh the initial expense. It’s an investment in your company’s growth, efficiency, and reputation.
In the next section, we’ll break down the specific factors that influence the Cost of ISO 9001 Certification, so you can better understand what goes into pricing and how to plan for it. Let’s keep going!
Factors That Influence the Cost of ISO 9001 Certification
So, what exactly determines the Cost of ISO 9001 Certification? The price can vary widely depending on a few key factors, which is why it’s important to understand what goes into it. Knowing these factors will help you better plan your budget and avoid surprises along the way. Let’s break it down together.
1. Business Size and Complexity
One of the biggest influences on the Cost of ISO 9001 Certification is the size and complexity of your business. Larger organizations with multiple locations or a wide range of services will naturally have more processes to evaluate and document, which can increase costs.
Example:
A small local café will likely spend less on certification than a global food production company because there are fewer processes to manage and standardize. The more moving parts your business has, the more time and resources the certification process will require.
2. Current Processes and Documentation
If your business already has a strong foundation of processes and documentation, you’re off to a great start. Companies that need to build a quality management system (QMS) from scratch will face higher upfront costs as they work to align with ISO 9001 requirements.
Example:
If you’re a manufacturer with detailed operating procedures and training records in place, you’ll spend less time and money on preparation. On the other hand, if you’re starting from ground zero, you may need to invest in creating documentation and training your team.
3. Industry-Specific Requirements
Certain industries have unique challenges or additional compliance requirements that can affect the Cost of ISO 9001 Certification. For example, healthcare providers or food manufacturers may need to meet specific safety or regulatory standards alongside ISO 9001.
Example:
A tech startup focusing on software development might have a simpler path to certification compared to a pharmaceutical company that must account for rigorous safety standards and detailed records.
4. Certification Body and Auditor Fees
The organization you choose to conduct your ISO 9001 audit will also play a role in determining the cost. Certification bodies set their own fees, which can vary depending on their reputation, location, and the services they offer.
Tips to Save:
- Research and compare certification bodies to find one that offers competitive pricing without compromising quality.
- Look for local auditors to avoid additional travel costs.
5. Employee Training Needs
Training your team on ISO 9001 requirements is another factor to consider. If your employees are already familiar with quality management systems, you might need less training. However, if ISO 9001 is new to your organization, investing in workshops or online courses will add to the overall Cost of ISO 9001 Certification.
Example:
A company with an experienced quality assurance team may only need a quick refresher, while a small business with no prior knowledge of ISO 9001 might need more extensive training for its employees.
6. Ongoing Maintenance Costs
Certification isn’t a one-time expense—it’s an ongoing process. Once you’re certified, you’ll need to budget for regular surveillance audits and continuous improvement to maintain your status.
Example:
A business might spend a few thousand dollars annually on follow-up audits and refining processes, which ensures they stay compliant and competitive.
What This Means for You
The Cost of ISO 9001 Certification isn’t fixed—it’s shaped by your business’s unique characteristics and needs. By understanding these factors, you can plan ahead, set realistic expectations, and focus on getting the best return on your investment.
In the next section, we’ll go even deeper and break down the costs into specific categories like implementation, training, and audit fees. Stick with me as we continue this journey to make ISO 9001 certification easier to understand and plan for!
Breaking Down the Cost of ISO 9001 Certification
Now that we’ve explored the factors that influence the Cost of ISO 9001 Certification, let’s dig a little deeper and break it down into the key components. Understanding what goes into the overall cost will give you a clearer picture of where your money is going and help you budget more effectively. Let’s take it one step at a time.
1. Implementation Costs
The first big piece of the puzzle is implementation. This involves creating or updating your quality management system (QMS) to align with ISO 9001 requirements. For some businesses, this might mean tweaking existing processes, while for others, it could involve building a QMS from scratch.
What’s Included:
- Reviewing and documenting current processes.
- Developing policies and procedures.
- Implementing tools or software to manage quality.
Example:
A small business with minimal processes might only need to spend a few hundred dollars on basic documentation. Meanwhile, a larger company might invest in specialized software to handle more complex workflows, adding to the Cost of ISO 9001 Certification.
2. Training Costs
To get the most out of ISO 9001, your team needs to understand how the system works and their role in maintaining it. Training is a critical part of the certification process, and the cost will depend on the level of expertise your employees need.
What’s Included:
- Online courses, workshops, or in-house training sessions.
- Certification-related materials, like guides or manuals.
Example:
A company new to ISO 9001 might invest in a full-day training workshop for all employees, while a business with experienced staff might only need a short refresher course. The cost here varies but is an essential part of the journey.
3. Internal Audits and Pre-Certification Preparation
Before the official certification audit, you’ll want to conduct internal audits to identify gaps and address any issues. This step is like a “practice run” to ensure your QMS meets ISO 9001 standards.
What’s Included:
- Time spent conducting internal audits.
- Hiring an external consultant, if needed, to help prepare.
Example:
Some companies handle this internally with existing staff, keeping costs low, while others might hire a consultant for expert advice, which adds to the Cost of ISO 9001 Certification.
4. Certification Audit Fees
This is where an accredited certification body steps in to conduct the official audit. The auditor will evaluate your QMS to ensure it complies with ISO 9001 requirements. The fees for this audit can vary depending on the size of your business and the complexity of your operations.
What’s Included:
- The auditor’s time (on-site or remote).
- Travel expenses if the auditor visits your location.
Example:
For a small business, audit fees might range from $1,000 to $3,000, while larger organizations could see costs upwards of $10,000 due to the additional time and complexity involved.
5. Ongoing Maintenance Costs
Once you’re certified, there are ongoing costs to maintain your ISO 9001 certification. These include surveillance audits (typically conducted annually) and the time spent on continuous improvement to keep your QMS effective.
What’s Included:
- Regular surveillance audits by the certification body.
- Updates to processes and training as your business evolves.
Example:
A medium-sized business might budget $2,000 to $5,000 annually for these ongoing costs to ensure compliance and continuous improvement.
What’s the Total?
The total Cost of ISO 9001 Certification depends on your unique business needs, but here’s a rough estimate to guide you:
- Small Businesses: $5,000–$10,000
- Medium-Sized Businesses: $10,000–$20,000
- Large Organizations: $20,000+
Remember, these numbers are just ballpark figures. The final cost will depend on the specifics of your business, including its size, industry, and current processes.
Making the Numbers Work for You
When you break it down, the Cost of ISO 9001 Certification becomes much easier to understand and manage. Think of it as a series of smaller, manageable steps rather than one giant expense. In the next section, we’ll share tips on how to minimize costs and get the most value from the certification process. Let’s keep going!
How to Minimize the Cost of ISO 9001 Certification
The Cost of ISO 9001 Certification might seem daunting at first, but the good news is there are plenty of ways to keep expenses under control. With some smart planning and strategic choices, you can reduce costs without compromising on quality. Let’s explore how to make the certification process as cost-effective as possible.
1. Start with a Gap Analysis
Before diving into the certification process, it’s essential to understand where your business currently stands. A gap analysis helps you identify which parts of your operations already align with ISO 9001 and where improvements are needed. This way, you can focus your resources on the areas that need the most attention.
How It Helps:
By knowing exactly what you need to fix, you can avoid unnecessary spending on processes or systems that are already working well.
Example:
A small manufacturing company might discover during a gap analysis that their quality checks are already ISO-compliant but their documentation needs improvement. They can then allocate their budget to enhancing record-keeping instead of overhauling their entire system.
2. Leverage Internal Resources
One of the easiest ways to reduce the Cost of ISO 9001 Certification is to use your existing team to handle parts of the process. With the right training and tools, your employees can take on tasks like creating documentation, conducting internal audits, and managing implementation.
How It Helps:
Relying on internal resources saves you from hiring external consultants or trainers for every step of the journey.
Example:
If your company already has a quality manager or team, empower them to lead the ISO 9001 implementation process. Provide them with training or resources to build their expertise rather than outsourcing the entire project.
3. Choose the Right Certification Body
Not all certification bodies are created equal, and their fees can vary significantly. Research and compare options to find a reputable body that offers competitive pricing.
How It Helps:
By shopping around, you can find a certification body that fits your budget without compromising on quality.
Tips for Saving:
- Look for local auditors to avoid travel-related expenses.
- Check reviews and references to ensure the certification body has a solid reputation.
4. Focus on Incremental Changes
Trying to overhaul your entire business at once can be overwhelming and expensive. Instead, tackle the certification process in manageable steps. Prioritize critical areas first, then address less urgent issues over time.
How It Helps:
Spreading out the changes allows you to balance costs and avoid overburdening your team.
Example:
A retail company might start by standardizing customer service procedures and gradually move on to improving inventory management.
5. Use Affordable Training Options
Training your employees is essential, but it doesn’t have to break the bank. Many online courses, webinars, and self-paced learning options are available at a fraction of the cost of in-person workshops.
How It Helps:
Affordable training options let you equip your team with the knowledge they need without overspending.
Example:
A small IT firm might use free or low-cost ISO 9001 resources to train employees on quality management basics before investing in more specialized workshops.
6. Invest in Technology
Sometimes, spending a little upfront on tools or software can save you money in the long run. Quality management software can help you streamline documentation, track performance, and manage audits more efficiently.
How It Helps:
By automating certain processes, you reduce manual effort and minimize the risk of errors.
Example:
A logistics company might use QMS software to track delivery performance and customer feedback, cutting down on time spent on manual record-keeping.
7. Plan for the Long Term
Remember, the Cost of ISO 9001 Certification isn’t just about getting certified—it’s about maintaining compliance. Budgeting for ongoing surveillance audits and regular updates to your processes ensures you’re always prepared for what’s next.
How It Helps:
Planning for long-term costs prevents surprises and keeps your business running smoothly.
Example:
A healthcare provider might allocate a portion of their annual budget to ISO-related expenses, ensuring they’re ready for future audits without scrambling for funds.
Why Cost-Effectiveness Matters
By taking these steps, you can significantly reduce the Cost of ISO 9001 Certification while still achieving all the benefits of certification. It’s all about working smarter, not harder, and focusing your resources on what truly matters.
In the next section, we’ll look at real-life examples of businesses that successfully managed their certification costs and saw incredible returns on their investment. Let’s keep the momentum going!
Real-Life Examples of ISO 9001 Certification Costs and ROI
If you’re wondering whether the Cost of ISO 9001 Certification is really worth it, the best way to answer that question is by looking at real-world examples. Many businesses, both large and small, have invested in ISO 9001 certification and seen remarkable returns on their investment. Let’s take a closer look at how some companies managed their costs and reaped the benefits.
1. The Small Manufacturing Business That Saved on Waste
A small family-owned manufacturing company decided to pursue ISO 9001 certification to improve their processes and reduce waste. While the initial Cost of ISO 9001 Certification seemed steep—about $8,000—they quickly discovered that implementing better quality controls saved them thousands of dollars each month in wasted materials.
Key Savings:
- Reduced material waste by 30% within six months.
- Improved production efficiency, allowing them to meet deadlines more consistently.
ROI:
Within the first year, their savings in reduced waste and increased customer orders more than covered the cost of certification.
2. The IT Startup That Won Big Contracts
A small IT startup was struggling to win contracts with larger corporations. After learning that many potential clients required ISO 9001 certification, they decided to invest in the process. The Cost of ISO 9001 Certification for their business came to about $10,000, which included training and audit fees.
Key Benefits:
- ISO 9001 certification opened doors to contracts with three major corporations.
- The startup built trust with potential clients, who saw the certification as proof of their commitment to quality.
ROI:
The new contracts brought in over $100,000 in revenue in the first year alone, making the upfront cost of certification a no-brainer.
3. The Retail Chain That Boosted Customer Satisfaction
A mid-sized retail chain wanted to improve customer satisfaction and streamline their inventory management. They spent around $15,000 on the Cost of ISO 9001 Certification, including hiring a consultant to help implement a quality management system.
Key Improvements:
- Reduced stockouts and overstock issues by 40%, improving customer experience.
- Established a clear system for tracking and resolving customer complaints.
ROI:
Happier customers led to a 20% increase in repeat business, which paid for the certification within two years.
4. The Logistics Company That Reduced Delivery Delays
A logistics company with a reputation for late deliveries decided it was time to make a change. They spent $12,000 on the Cost of ISO 9001 Certification, including training their team and upgrading their tracking systems.
Key Results:
- Delivery delays decreased by 50% within the first year.
- Customer satisfaction scores improved significantly, leading to more referrals.
ROI:
The company’s improved reputation helped them land a long-term contract with a major e-commerce retailer, increasing annual revenue by 25%.
5. The Healthcare Provider That Improved Compliance
A healthcare provider faced challenges meeting regulatory requirements and maintaining consistent patient care. They invested $20,000 in ISO 9001 certification, which included training, internal audits, and hiring an external auditor.
Key Benefits:
- Streamlined processes improved compliance with industry regulations.
- Enhanced patient satisfaction and reduced complaints.
ROI:
Their improved operations reduced regulatory fines and attracted more patients, resulting in significant financial and reputational gains.
What These Stories Teach Us
These real-life examples show that while the Cost of ISO 9001 Certification might seem like a big commitment upfront, the long-term benefits often far outweigh the initial expense. From reducing waste and improving efficiency to winning new contracts and building customer trust, ISO 9001 can transform your business in powerful ways.
Your Business Could Be Next
If these stories have inspired you, it’s time to think about how ISO 9001 could benefit your business. With careful planning and a clear understanding of the costs involved, you could be well on your way to achieving the same kind of success.
In the final section, we’ll wrap up everything you need to know about the Cost of ISO 9001 Certification and why it’s an investment worth making. Let’s finish strong!
Conclusion: The Cost of ISO 9001 Certification is an Investment in Your Future
When you look at the Cost of ISO 9001 Certification, it’s easy to focus on the price tag. But as we’ve seen throughout this discussion, it’s so much more than just an expense—it’s an investment in your business’s growth, efficiency, and reputation. Whether you’re a small business or a large organization, the benefits of ISO 9001 certification often far outweigh the initial costs.
Why the Cost of ISO 9001 Certification is Worth It
By implementing ISO 9001, you’re not just aligning with an international standard—you’re setting your business up for long-term success. Here’s what you gain:
- Better Customer Trust: Certification signals to your customers that you’re serious about delivering quality.
- Improved Efficiency: Streamlined processes reduce waste, save time, and cut costs.
- Access to New Opportunities: ISO 9001 certification can help you win bigger contracts and enter new markets.
- A Competitive Edge: Certification sets you apart in industries where quality is a must.
The Cost of ISO 9001 Certification becomes a strategic move when you consider the value it brings to your operations, team, and customers.
Plan for Success
Remember, the cost is influenced by factors like the size of your business, the complexity of your processes, and your current level of preparedness. By understanding these variables and planning carefully, you can manage costs and maximize the return on your investment. Start with small, manageable steps—like conducting a gap analysis or training your team—and work your way toward certification.
Make the Leap
At the end of the day, the Cost of ISO 9001 Certification isn’t just about dollars and cents—it’s about building a foundation for sustainable growth. Whether you’re looking to reduce waste, improve customer satisfaction, or position your business as a leader in your industry, ISO 9001 can help you get there.
So, what’s next for you? If you’re ready to take your business to the next level, consider starting your ISO 9001 journey today. The path might require effort and investment, but the rewards—greater efficiency, customer loyalty, and long-term success—are well worth it. Your future self (and your business) will thank you!
Looking for More Resources on ISO 9001?
Looking for ISO 9001 Resources Tailored to Your Industry?
If this article helped clarify ISO 9001, take the next step with our industry-focused tools designed to simplify your certification journey:
- ISO 9001 Documentation Kits by Industry: Whether you’re in manufacturing, construction, consulting, or healthcare — we have complete, ready-to-use documentation tailored for your sector.
- Online ISO 9001 Training: Learn how to implement ISO 9001 effectively with our easy-to-follow video lessons, real-world examples, and practical exercises.
- ISO 9001 Checklist: Download our step-by-step checklist to ensure your QMS meets all the 9001:2015 requirements from start to finish.
These resources are crafted to save you time, reduce stress, and help you achieve certification with confidence. Choose your industry and start now!
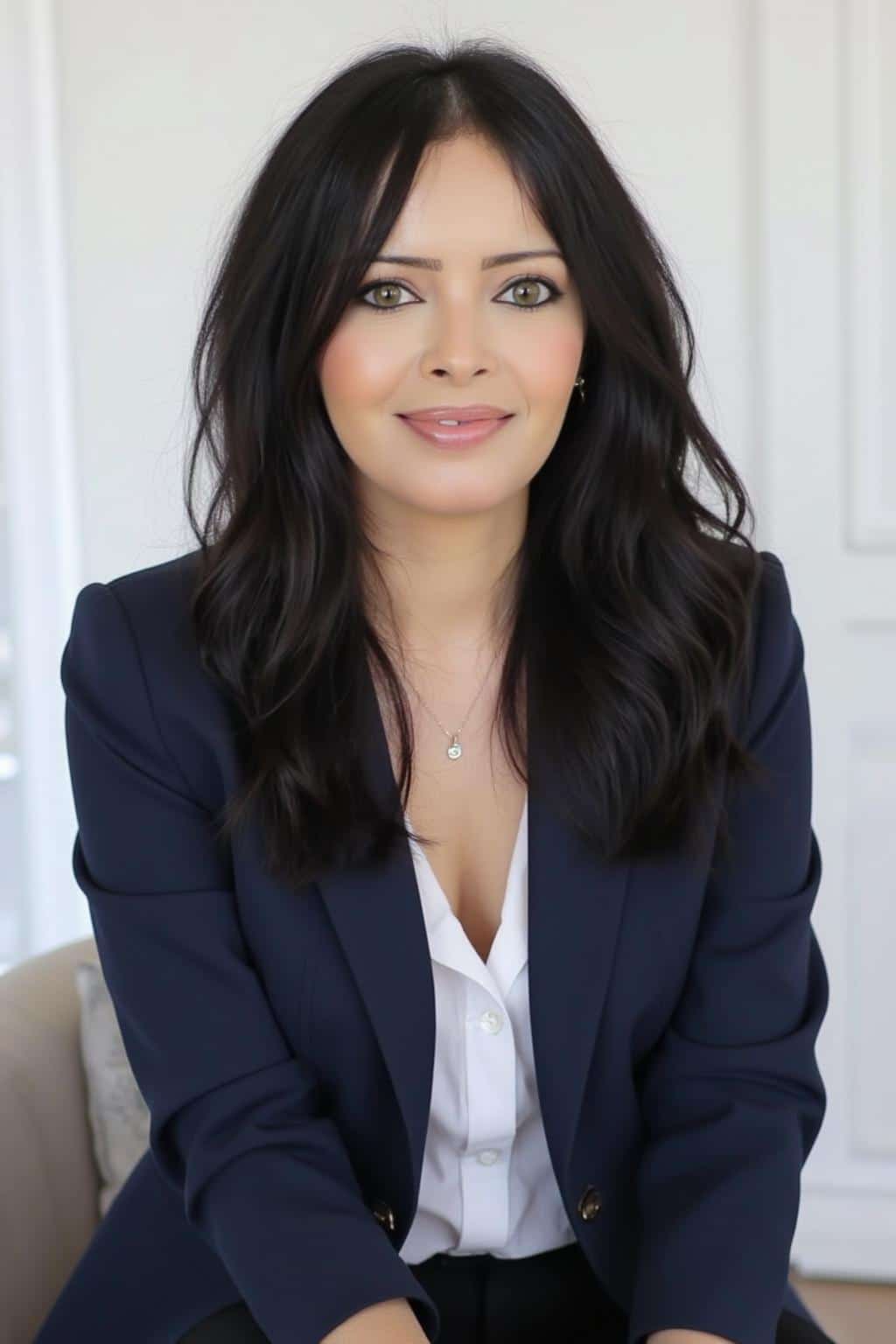
make ISO standards less intimidating and more approachable for everyone.
Whether it’s ISO 9001, ISO 22000, or the cosmetics-focused ISO 22716, I’ve spent my career
turning complex jargon into clear, actionable steps that businesses can actually use.
I’m not here to call myself an expert—I prefer “enthusiast” because I truly love what I do.
There’s something incredibly rewarding about helping people navigate food safety and quality management systems
in a way that feels simple, practical, and even enjoyable.
When I’m not writing about standards, you’ll probably find me playing Piano 🎹, connecting with people, or diving into my next big project💫.
I’m an engineer specialized in the food and agricultural industry
I have a Master’s in QHSE management and over 12 years of experience as a Quality Manager
I’ve helped more than 15 companies implement ISO 9001, ISO 22000, ISO 22716, GMP, and other standards
My clients include food producers, cosmetics manufacturers, laboratories, and service companies
I believe quality systems should be simple, useful, and efficient.