ISO 9001 Quality Objectives : A Comprehensive Overview
The Ultimate Guide to ISO 9001 Quality Objectives : A Comprehensive Overview
If you’re working with ISO 9001, you’ve probably heard about ISO 9001 Quality Objectives—but what exactly are they, and why do they matter? Are they just another requirement for certification, or can they actually help your business grow and improve?
Here’s the good news: when done right, ISO 9001 Quality Objectives can be a powerful tool for continuous improvement, customer satisfaction, and business success. These objectives go beyond compliance—they serve as measurable goals that guide your organization toward better quality, efficiency, and performance.
ISO 9001:2015 Clause 6.2 lays out clear expectations for setting, implementing, and tracking quality objectives. But many companies struggle with defining objectives that are realistic, meaningful, and actually drive improvement. That’s where this guide comes in!
In this article, we’ll break down:
✔ What ISO 9001 Quality Objectives are and why they’re essential
✔ How to develop clear, measurable objectives that align with your business goals
✔ How to track and improve quality objectives over time
✔ Common mistakes to avoid when setting ISO 9001 Quality Objectives
✔ How auditors assess quality objectives during ISO 9001 certification audits
By the end, you’ll have a clear roadmap for creating and implementing effective ISO 9001 Quality Objectives that help your company thrive—not just pass an audit. Let’s dive in!
What Are ISO 9001 Quality Objectives and Why Do They Matter?
Let’s start with the basics—what exactly are ISO 9001 Quality Objectives, and why are they so important?
In simple terms, ISO 9001 Quality Objectives are measurable goals that help an organization improve its quality management system (QMS). They act as road signs guiding a company toward better efficiency, higher customer satisfaction, and continuous improvement.
ISO 9001:2015, specifically Clause 6.2, requires organizations to define, implement, and track quality objectives that align with their overall quality policy. But this isn’t just about compliance—it’s about making sure your company is always moving forward.
Imagine you’re running a manufacturing business. A vague goal like “We want to improve product quality” isn’t enough. But an ISO 9001 Quality Objective like “Reduce product defects by 10% within the next 6 months through enhanced quality control measures”? That’s a clear, actionable, and measurable target that drives real progress.
Key Requirements of ISO 9001 Quality Objectives
ISO 9001 isn’t about setting random goals—it’s about defining objectives that actually make a difference. That’s why Clause 6.2 sets out specific requirements for ISO 9001 Quality Objectives. Here’s what they need to include:
✅ Consistency with the Quality Policy – Your objectives should align with your company’s overall quality commitments.
✅ Measurable and Trackable – You need to quantify your goals so you can measure progress (e.g., improve on-time delivery from 85% to 95%).
✅ Relevant to Business and Customer Needs – The objectives should directly impact product quality, customer satisfaction, efficiency, or compliance.
✅ Time-Bound – Objectives should have a clear deadline to track progress and maintain accountability.
✅ Communicated Across the Organization – Employees at all levels should be aware of the objectives and their role in achieving them.
The Connection Between ISO 9001 Quality Objectives and Business Success
A strong set of ISO 9001 Quality Objectives doesn’t just help with certification—it helps businesses:
✔ Improve product and service quality – Reducing defects, improving processes, and enhancing customer satisfaction.
✔ Increase operational efficiency – Minimizing waste, optimizing resources, and reducing errors.
✔ Boost customer trust and loyalty – Showing a commitment to quality strengthens relationships with clients.
✔ Drive continuous improvement – Objectives encourage a culture where employees actively look for ways to do things better.
📌 Example: A customer service company struggling with long response times might set a quality objective to reduce average response time from 24 hours to 12 hours over the next three months. This would not only improve efficiency but also enhance customer satisfaction and retention.
Final Thoughts: Why ISO 9001 Quality Objectives Matter
Without ISO 9001 Quality Objectives, companies risk losing focus on quality, failing audits, and missing out on improvement opportunities. These objectives help organizations stay on track, measure success, and make meaningful progress toward their quality goals.
In the next section, we’ll explore how to develop effective ISO 9001 Quality Objectives that align with your business strategy and set you up for success. Stay tuned!
How to Develop Effective ISO 9001 Quality Objectives
Now that we know what ISO 9001 Quality Objectives are and why they matter, the next big question is: How do you create objectives that are clear, meaningful, and actually drive improvement?
The good news? Setting effective ISO 9001 Quality Objectives doesn’t have to be complicated. The key is to make them specific, measurable, and directly connected to your quality management goals. Let’s walk through the process step by step.
Step 1: Align Objectives with Business Strategy and Quality Policy
Your ISO 9001 Quality Objectives should never exist in isolation—they should directly support your company’s business strategy, customer needs, and overall quality policy.
🔹 Ask yourself:
- What are the most critical quality challenges we face as a company?
- How can quality objectives help us improve customer satisfaction?
- Which aspects of our operations need measurable improvement?
📌 Example: A logistics company that frequently faces delivery delays might set a quality objective to increase on-time deliveries from 85% to 95% within the next 6 months. This directly supports customer satisfaction and aligns with business goals.
Step 2: Use the SMART Criteria for Setting ISO 9001 Quality Objectives
The best ISO 9001 Quality Objectives follow the SMART framework:
✅ S – Specific: Clearly define what you want to improve.
✅ M – Measurable: Include numbers or key performance indicators (KPIs) to track progress.
✅ A – Achievable: Set realistic goals based on resources and capabilities.
✅ R – Relevant: Make sure the objective aligns with business needs and ISO 9001 requirements.
✅ T – Time-bound: Set a deadline for achieving the goal.
📌 Example of a SMART Quality Objective:
“Reduce product defects from 5% to 2% over the next 12 months by improving quality control checks and employee training.”
🔹 Why it works:
- Specific? ✔ Focuses on defect reduction.
- Measurable? ✔ Clear percentage targets.
- Achievable? ✔ A realistic improvement goal.
- Relevant? ✔ Directly improves product quality.
- Time-bound? ✔ Has a 12-month deadline.
Compare that to a vague objective like: “Improve product quality”—which offers no direction, no timeline, and no way to measure success.
Step 3: Involve Key Stakeholders in Defining ISO 9001 Quality Objectives
A common mistake? Setting quality objectives without involving the people who actually impact quality.
🔹 Who should be involved?
- Top management – Ensures objectives align with business goals.
- Quality managers – Provides insight into compliance and process improvements.
- Employees – Offers practical input on what’s achievable in daily operations.
📌 Example: If a hospital wants to improve patient care, nurses and frontline healthcare workers should be involved in setting ISO 9001 Quality Objectives—not just upper management.
🔹 Pro Tip: Employees are more likely to support and work toward quality objectives if they had a role in defining them. Make it a team effort!
Final Thoughts: Setting Quality Objectives That Drive Real Change
Creating effective ISO 9001 Quality Objectives is about more than just meeting certification requirements—it’s about using them as a tool to improve performance, efficiency, and customer satisfaction.
By ensuring your objectives are aligned with business strategy, SMART, and developed with team involvement, you set your company up for meaningful, measurable success.
In the next section, we’ll dive into real-world examples of ISO 9001 Quality Objectives across different industries—so you can see how companies are using them to drive improvement. Stay tuned!
Real-World Examples of ISO 9001 Quality Objectives Across Different Industries
Now that we’ve covered how to develop ISO 9001 Quality Objectives, let’s take a look at how different industries put them into practice. The best quality objectives are specific, measurable, and aligned with business goals—but they also vary depending on the industry and company needs.
Below are some real-world examples to help you see how ISO 9001 Quality Objectives can drive improvement in different business sectors.
Manufacturing Industry: Reducing Defects and Improving Efficiency
In manufacturing, ISO 9001 Quality Objectives often focus on product quality, process efficiency, and waste reduction.
📌 Example 1: Reducing Defect Rates
“Reduce the defect rate of manufactured parts from 4% to 2% within the next 12 months through improved quality control and employee training.”
✔ Why it works:
- Targets a specific problem (defects).
- Provides a measurable goal (cutting defects in half).
- Focuses on achievable solutions (quality control and training).
- Time-bound with a 12-month deadline.
📌 Example 2: Increasing Production Efficiency
“Improve production line efficiency by 15% over the next six months by implementing lean manufacturing techniques.”
✔ Why it works:
- Addresses a key business goal (efficiency).
- Measurable with a percentage increase.
- Focuses on practical improvements (lean manufacturing).
Service Industry: Enhancing Customer Satisfaction
For service-based businesses, ISO 9001 Quality Objectives typically focus on customer satisfaction, response times, and service quality.
📌 Example 3: Improving Customer Satisfaction Scores
“Increase customer satisfaction scores from 85% to 90% within a year by enhancing service response times and customer support training.”
✔ Why it works:
- Directly linked to customer experience.
- Measurable goal (moving from 85% to 90%).
- Focuses on specific improvements (faster response times and better training).
📌 Example 4: Reducing Customer Complaints
“Reduce customer complaints related to service delays by 30% within six months through process optimization and staff training.”
✔ Why it works:
- Clearly defines the issue (service delays).
- Measurable improvement (30% reduction).
- Actionable strategies (process optimization and training).
Healthcare Industry: Enhancing Patient Safety and Efficiency
In healthcare, ISO 9001 Quality Objectives are often centered on patient care, safety, and regulatory compliance.
📌 Example 5: Reducing Patient Wait Times
“Decrease patient wait times in the emergency department by 20% within the next year by optimizing scheduling and triage processes.”
✔ Why it works:
- Tackles a common healthcare challenge.
- Provides a clear measurement (20% reduction).
- Identifies specific solutions (scheduling and triage improvements).
📌 Example 6: Enhancing Compliance with Safety Protocols
“Achieve 100% compliance with hospital hand hygiene protocols by the end of the year through staff training and monitoring.”
✔ Why it works:
- Directly improves patient safety.
- Measurable success (100% compliance).
- Focuses on real implementation (training and monitoring).
Logistics Industry: Increasing Delivery Accuracy and Timeliness
For logistics and supply chain companies, ISO 9001 Quality Objectives focus on on-time deliveries, order accuracy, and process efficiency.
📌 Example 7: Improving On-Time Delivery Rates
“Increase on-time delivery rates from 92% to 98% within the next 9 months by optimizing route planning and warehouse operations.”
✔ Why it works:
- Addresses a key logistics challenge (late deliveries).
- Measurable improvement (92% → 98%).
- Identifies clear strategies (route planning and warehouse efficiency).
📌 Example 8: Reducing Order Errors
“Reduce order fulfillment errors by 40% within a year through barcode scanning technology and employee training.”
✔ Why it works:
- Focuses on a critical business process (order accuracy).
- Measurable target (40% reduction).
- Provides clear action steps (barcode technology and training).
Why Industry-Specific ISO 9001 Quality Objectives Matter
As you can see, ISO 9001 Quality Objectives can be tailored to fit the unique needs of any business. The key takeaway? Make them relevant, measurable, and action-driven.
✔ If you’re in manufacturing, focus on reducing defects and improving efficiency.
✔ If you’re in customer service, aim for higher satisfaction and faster response times.
✔ If you’re in healthcare, prioritize patient safety and compliance.
✔ If you’re in logistics, work on delivery accuracy and operational efficiency.
By choosing the right quality objectives for your industry, you ensure that your ISO 9001 Quality Objectives truly support business growth and improvement.
Final Thoughts: Creating Quality Objectives That Drive Real Impact
Quality objectives shouldn’t just exist for ISO 9001 compliance—they should serve as a roadmap to better performance, efficiency, and customer satisfaction.
In the next section, we’ll explore how to implement and track ISO 9001 Quality Objectives to ensure they aren’t just words on paper but actually drive real business improvements. Stay tuned!
How to Implement and Track ISO 9001 Quality Objectives
Now that you’ve set your ISO 9001 Quality Objectives, the real work begins—implementing them and tracking progress. After all, an objective that’s written down but never acted on won’t do much to improve your business.
The key to success? Clear responsibility, ongoing measurement, and continuous improvement. Let’s walk through how to bring your quality objectives to life in a way that actually drives results.
Step 1: Assign Responsibility for Each ISO 9001 Quality Objective
A quality objective is only effective if someone is accountable for achieving it. That’s why each objective should have a clear owner or team responsible for its success.
✅ Define Who’s in Charge – Assign responsibility to a specific department or team (e.g., quality control, customer service, production).
✅ Break It Down by Role – Make sure every employee involved knows their part in achieving the objective.
✅ Set Clear Expectations – Establish what needs to be done, by whom, and by when.
📌 Example: If your ISO 9001 Quality Objective is to reduce product defects by 10% in six months, your quality control team might be responsible for improving inspection procedures, while your production team ensures better adherence to quality standards.
Step 2: Establish Key Performance Indicators (KPIs) to Measure Success
If you can’t measure it, you can’t manage it! Your ISO 9001 Quality Objectives need clear, measurable indicators so you can track progress.
✅ Define Key Metrics – What data will you track? (e.g., defect rates, customer complaints, on-time deliveries)
✅ Set Baselines and Targets – Compare progress against current performance.
✅ Use Data-Driven Insights – Monitor trends to understand whether you’re moving in the right direction.
📌 Example KPIs for Different Objectives:
- Reducing customer complaints – Track the number of complaints per month and compare it to your target reduction.
- Improving delivery accuracy – Measure the percentage of orders delivered on time and error-free.
- Increasing production efficiency – Track units produced per hour or percentage of downtime.
🔹 Pro Tip: Use a dashboard or tracking software to regularly monitor progress and keep objectives visible to your team.
Step 3: Integrate ISO 9001 Quality Objectives into Daily Operations
To make sure your quality objectives aren’t forgotten, they should be woven into everyday workflows.
✅ Include Quality Objectives in Team Meetings – Regularly review progress in team discussions.
✅ Incorporate Them into Employee Training – Ensure all staff understands how their daily work contributes to the objectives.
✅ Use Visual Reminders – Post objectives on bulletin boards, digital screens, or internal portals.
📌 Example: A customer service company aiming to reduce average response time from 24 hours to 12 hours might add a real-time tracking board to monitor open support tickets.
Step 4: Conduct Regular Reviews and Adjust Objectives as Needed
Setting ISO 9001 Quality Objectives isn’t a “set it and forget it” process. You need to continuously monitor progress and make adjustments if needed.
✅ Schedule Monthly or Quarterly Reviews – Check if you’re on track or if changes are needed.
✅ Analyze Roadblocks – Identify issues slowing down progress and find solutions.
✅ Revise Objectives If Necessary – If an objective is too ambitious or too easy, adjust it to make it meaningful.
📌 Example: If a hospital set a quality objective to reduce patient wait times by 20% in six months, but only achieved a 5% reduction, they might adjust staffing schedules or update their triage process to improve results.
Step 5: Link ISO 9001 Quality Objectives to Continuous Improvement
ISO 9001 is built on continuous improvement—meaning once an objective is achieved, you should be thinking about what’s next.
✅ Celebrate Achievements – Recognize teams that hit their targets and reinforce a culture of quality.
✅ Set New Goals – Once one objective is met, set a new, slightly more ambitious goal.
✅ Keep Refining Your Processes – Use insights from previous objectives to further streamline operations.
📌 Example: A manufacturing plant that reduces defects from 5% to 2% can set a new objective to implement automation tools for even greater precision.
Final Thoughts: Making ISO 9001 Quality Objectives Work for Your Business
The difference between a good and great ISO 9001 Quality Objective isn’t just how well it’s written—it’s how well it’s implemented, tracked, and continuously improved.
✔ Assign ownership so objectives don’t get overlooked.
✔ Measure success using KPIs and data-driven tracking.
✔ Make objectives part of daily operations so they stay top of mind.
✔ Review and refine them regularly to adapt to business needs.
✔ Use them as a tool for continuous improvement, not just for ISO compliance.
When done right, ISO 9001 Quality Objectives don’t just help you pass audits—they drive real, meaningful business improvements.
In the next section, we’ll dive into common mistakes to avoid when setting and tracking ISO 9001 Quality Objectives, so you can ensure your quality goals are truly effective. Stay tuned!
Common Mistakes to Avoid When Setting and Tracking ISO 9001 Quality Objectives
By now, you know that ISO 9001 Quality Objectives are a powerful tool for improving your business. But here’s the thing—not all quality objectives are effective. In fact, many companies set objectives that sound good on paper but fail to drive real results.
So, how do you make sure your ISO 9001 Quality Objectives actually work? By avoiding these common mistakes that can derail your quality improvement efforts. Let’s dive in!
Mistake #1: Setting Vague and Unmeasurable Objectives
One of the biggest mistakes companies make is creating objectives that are too broad or vague. If your objective doesn’t have a clear way to measure success, it’s nearly impossible to track progress.
🚫 Bad Example: “Improve product quality.”
✔ Better Example: “Reduce defective units from 4% to 2% over the next 12 months by improving supplier quality checks.”
🔹 How to Fix It: Always use the SMART method (Specific, Measurable, Achievable, Relevant, Time-bound) to create ISO 9001 Quality Objectives that are clear and actionable.
Mistake #2: Choosing Objectives That Don’t Align with Business Goals
ISO 9001 Quality Objectives should not exist in isolation—they should directly support your business strategy. If your objectives don’t align with your company’s goals, they’ll feel irrelevant to employees and won’t drive meaningful improvements.
🚫 Bad Example: A retail company setting an objective to reduce machine downtime when their real issue is customer service delays.
✔ Better Example: Setting an objective to reduce customer response time from 48 hours to 24 hours to improve satisfaction and retention.
🔹 How to Fix It: Make sure your quality objectives are tied to key business priorities, customer needs, and operational challenges.
Mistake #3: Setting Objectives That Are Unrealistic or Too Easy
Your ISO 9001 Quality Objectives should be challenging but achievable. If they’re too ambitious, your team may feel overwhelmed and give up. If they’re too easy, they won’t lead to real improvement.
🚫 Bad Example (Too Ambitious): “Achieve 100% customer satisfaction within three months.” (Unrealistic because no company has perfect satisfaction.)
🚫 Bad Example (Too Easy): “Increase customer satisfaction from 85% to 86% in a year.” (A 1% increase doesn’t drive meaningful change.)
✔ Better Example: “Increase customer satisfaction from 85% to 90% within 12 months by improving response times and implementing customer service training.”
🔹 How to Fix It: Set challenging but achievable targets, and review historical data to determine what’s realistic.
Mistake #4: Not Assigning Responsibility for Each Objective
If no one is responsible for an objective, it won’t get done. Every ISO 9001 Quality Objective should have a clear owner or team accountable for implementation.
🚫 Bad Example: “Reduce order errors by 20%.” (Who is responsible?)
✔ Better Example: “The warehouse team will reduce order errors by 20% in six months by implementing barcode scanning and improving employee training.”
🔹 How to Fix It: Clearly assign responsibility so that someone is accountable for tracking progress and making improvements.
Mistake #5: Failing to Track and Review Progress
Setting ISO 9001 Quality Objectives isn’t a one-time task. If you don’t monitor progress regularly, you won’t know if you’re on track or need to make adjustments.
🚫 Bad Example: Setting an objective but never reviewing progress until the next audit.
✔ Better Example: Reviewing progress monthly or quarterly and making necessary adjustments.
🔹 How to Fix It:
✅ Use KPIs to track results (e.g., defect rates, customer complaints, response times).
✅ Schedule regular reviews to assess progress.
✅ Adjust the objective if needed (e.g., if new challenges arise or the goal was too easy).
Mistake #6: Not Communicating Quality Objectives to Employees
Your ISO 9001 Quality Objectives won’t be effective if employees don’t know about them. Everyone in your organization should understand how their work contributes to achieving quality goals.
🚫 Bad Example: The quality manager sets objectives, but employees in production or customer service have no idea what they are.
✔ Better Example: Objectives are shared in team meetings, posted on bulletin boards, and discussed regularly so everyone knows their role.
🔹 How to Fix It:
✅ Include objectives in employee training and onboarding.
✅ Discuss them in regular meetings.
✅ Make them visible in shared spaces or digital dashboards.
Mistake #7: Not Using Quality Objectives for Continuous Improvement
Some companies see ISO 9001 Quality Objectives as just a requirement for certification audits—but that misses the point. These objectives should drive real business improvements.
🚫 Bad Example: Setting an objective just to pass an ISO audit, then forgetting about it.
✔ Better Example: Using quality objectives to continuously improve products, services, and customer satisfaction.
🔹 How to Fix It:
✅ Treat quality objectives as a tool for business growth—not just for compliance.
✅ Set new objectives once previous ones are achieved.
✅ Make quality a core part of your company culture.
Final Thoughts: Avoiding Common Pitfalls in ISO 9001 Quality Objectives
Avoiding these mistakes can mean the difference between an objective that drives real improvement and one that just sits in a report.
✔ Set clear, measurable objectives (avoid vague goals).
✔ Make sure they align with business priorities (not random metrics).
✔ Keep them realistic but challenging (not too easy, not impossible).
✔ Assign responsibility (so someone is accountable).
✔ Monitor progress regularly (don’t wait until the audit).
✔ Communicate objectives to employees (so everyone is on board).
✔ Use them for continuous improvement (not just compliance).
By following these best practices, your ISO 9001 Quality Objectives will become a powerful tool for growth, efficiency, and quality improvement—not just a requirement to check off your audit list.
In the next section, we’ll discuss how auditors assess ISO 9001 Quality Objectives and what you can do to ensure compliance and a smooth audit process. Stay tuned!
How Auditors Assess ISO 9001 Quality Objectives (and How to Prepare for an Audit)
If you’re working toward ISO 9001 certification—or just trying to maintain compliance—you know that ISO 9001 Quality Objectives play a big role in the audit process. But what exactly are auditors looking for? And more importantly, how can you ensure that your quality objectives pass the audit with ease?
Don’t worry—I’ve got you covered. Let’s break it down in simple, practical terms so you can feel confident when the auditor arrives.
What Do Auditors Look for in ISO 9001 Quality Objectives?
During an ISO 9001 audit, auditors will evaluate your ISO 9001 Quality Objectives based on several key factors. Here’s what they’re checking for:
✅ Are Your Quality Objectives Clearly Defined?
- Auditors will ask to see documented quality objectives to ensure they meet the SMART criteria (Specific, Measurable, Achievable, Relevant, and Time-bound).
- Pro Tip: If your objectives are vague, like “Improve product quality,” you might run into trouble. Instead, make them specific, like “Reduce product defects from 4% to 2% within 12 months.”
✅ Do Your Quality Objectives Align with Your Quality Policy?
- Your objectives should directly support your company’s quality policy and business strategy.
- Pro Tip: If your quality policy emphasizes customer satisfaction, at least one of your objectives should focus on customer-related metrics, like response times or complaint resolution.
✅ Are Your Objectives Being Monitored and Tracked?
- Auditors will check if you track progress toward achieving your ISO 9001 Quality Objectives.
- They may ask for evidence of performance reviews, data analysis, and corrective actions taken when objectives are not met.
- Pro Tip: If an objective isn’t being measured, it doesn’t count in the eyes of an auditor. Make sure you’re keeping records of progress.
✅ Are Your Quality Objectives Communicated to Employees?
- Auditors often interview employees at different levels of the organization to see if they know about the quality objectives and how their work contributes to them.
- Pro Tip: If employees don’t know the company’s quality objectives, it could lead to a nonconformance finding. Regularly discuss objectives in meetings and training sessions.
✅ Have You Taken Action to Achieve Your Objectives?
- It’s not enough to just set objectives—you must show what actions you’ve taken to reach them.
- Auditors will look for evidence of process improvements, employee training, or corrective measures taken when progress is slow.
- Pro Tip: Keep a log of quality improvements that shows how your objectives have driven real change.
How to Ensure Your ISO 9001 Quality Objectives Are Audit-Ready
To avoid last-minute stress, here’s a simple checklist to ensure your ISO 9001 Quality Objectives are audit-ready:
1. Keep Your Quality Objectives Well-Documented
✔ Maintain a clear record of all quality objectives.
✔ Ensure they are written in a SMART format and align with your quality policy.
✔ Store them in a centralized location where employees and auditors can easily access them.
📌 Example: If your objective is “Increase customer satisfaction from 85% to 90% within one year,” make sure this is documented in your Quality Management System (QMS).
2. Regularly Monitor and Measure Progress
✔ Establish Key Performance Indicators (KPIs) to track each objective.
✔ Keep data logs, reports, and performance reviews that show progress over time.
✔ Set up monthly or quarterly reviews to analyze results.
📌 Example: If your goal is to reduce product defects by 20%, maintain quality inspection reports that show the defect rate each month.
3. Involve Employees in the Process
✔ Train employees on what the quality objectives are and how they relate to their daily work.
✔ Display objectives in shared workspaces (bulletin boards, internal websites, dashboards).
✔ Encourage team discussions and feedback on progress.
📌 Example: A logistics company might place on-time delivery rate goals on a digital dashboard in the warehouse, so all employees can track progress in real-time.
4. Be Prepared to Explain Any Missed Targets
✔ If an objective wasn’t met, be ready to explain why and what actions were taken to improve.
✔ Show evidence of corrective actions, such as process changes, employee training, or technology upgrades.
📌 Example: If your goal was to reduce customer complaints by 30%, but you only achieved 20%, you could explain that a new training program was implemented mid-year, and the full impact will be seen in the next cycle.
5. Show Evidence of Continuous Improvement
✔ ISO 9001 is about ongoing improvement, not just setting objectives once and forgetting them.
✔ Demonstrate that you’ve used past results to refine and improve future objectives.
📌 Example: If you successfully reduced machine downtime by 15%, set a new objective to improve preventive maintenance schedules to reduce it further.
What Happens If Your ISO 9001 Quality Objectives Don’t Meet Audit Standards?
If an auditor finds issues with your ISO 9001 Quality Objectives, they might issue a nonconformance—but don’t panic! Here’s what to expect:
1️⃣ Minor Nonconformance:
- The objective is unclear, not measurable, or isn’t fully documented.
- Solution: Clarify and update the objective with better metrics.
2️⃣ Major Nonconformance:
- There’s no evidence that objectives are being tracked or acted upon.
- Solution: Implement a monitoring system, assign responsibility, and correct gaps in tracking and reporting.
3️⃣ Opportunity for Improvement (OFI):
- The auditor suggests a better way to track or refine your objectives but doesn’t issue a formal finding.
- Solution: Take the suggestion seriously and implement improvements before the next audit.
🔹 Pro Tip: If you do receive a nonconformance, address it quickly with a corrective action plan. This not only helps compliance but also demonstrates a commitment to continuous improvement.
Final Thoughts: Preparing for an Audit with Strong ISO 9001 Quality Objectives
Getting your ISO 9001 Quality Objectives audit-ready isn’t just about passing certification—it’s about building a quality-driven culture that improves efficiency, customer satisfaction, and business success.
✔ Clearly define and document quality objectives.
✔ Regularly measure and review progress.
✔ Ensure employees understand and support the objectives.
✔ Keep records of improvements and corrective actions.
✔ Use audits as an opportunity to refine and strengthen objectives.
By following these steps, you’ll not only pass your audit with confidence, but you’ll also turn your ISO 9001 Quality Objectives into a real driver of continuous improvement.
In the final section, we’ll summarize the key takeaways and outline the next steps you can take to fully integrate ISO 9001 Quality Objectives into your business. Stay tuned!
Final Thoughts: Turning ISO 9001 Quality Objectives into a Long-Term Success Strategy
By now, you have a clear understanding of how ISO 9001 Quality Objectives work—from setting them up and tracking progress to ensuring they pass audits. But here’s the key takeaway: ISO 9001 Quality Objectives aren’t just about compliance—they’re a tool for continuous improvement and long-term success.
The companies that get the most value from ISO 9001 Quality Objectives don’t just set them for the sake of passing an audit. They use them to enhance efficiency, improve customer satisfaction, and build a strong quality-focused culture.
So, what’s next? Let’s break down the key takeaways and your next steps to ensure your quality objectives truly make an impact.
Key Takeaways: Mastering ISO 9001 Quality Objectives
✔ ISO 9001 Quality Objectives should be SMART (Specific, Measurable, Achievable, Relevant, Time-bound).
Avoid vague goals—define objectives in a way that allows for clear measurement and accountability.
✔ Objectives must align with your company’s quality policy and business goals.
They should directly support customer satisfaction, operational efficiency, and process improvements.
✔ Tracking and reviewing quality objectives is essential for success.
Regular performance monitoring ensures that progress is on track and adjustments can be made when necessary.
✔ Employee involvement is key to achieving quality objectives.
When employees understand how their daily work contributes to ISO 9001 Quality Objectives, they are more engaged and committed to success.
✔ ISO 9001 Quality Objectives should be a part of your company’s culture, not just a document for audits.
Use them to drive real improvements, reduce waste, and enhance overall business performance.
Next Steps: How to Make ISO 9001 Quality Objectives Work for Your Business
✅ Step 1: Review Your Current Quality Objectives
- Are they clearly written?
- Do they align with your business goals?
- Are they measurable and trackable?
✅ Step 2: Improve Documentation and Tracking
- Ensure all objectives are properly documented in your QMS.
- Use KPIs and performance data to track progress.
- Set up regular review meetings to discuss progress and challenges.
✅ Step 3: Increase Employee Awareness and Engagement
- Communicate quality objectives across all departments.
- Train employees on how their roles contribute to quality goals.
- Encourage feedback and continuous improvement ideas from staff.
✅ Step 4: Be Prepared for ISO 9001 Audits
- Keep a clear record of progress, adjustments, and corrective actions.
- Make sure employees can explain quality objectives during an audit interview.
- Use audits as an opportunity to refine and strengthen your objectives.
✅ Step 5: Commit to Continuous Improvement
- Once an objective is met, set a new, slightly more challenging goal.
- Regularly refine objectives to adapt to business growth and industry changes.
- Keep quality objectives as a core part of decision-making and strategy.
Final Thought: Quality Objectives as a Competitive Advantage
At the end of the day, ISO 9001 Quality Objectives are more than a compliance requirement—they’re a powerful business tool. Companies that truly embrace them don’t just improve their quality management systems—they create stronger customer relationships, more efficient operations, and a culture of continuous improvement.
So, don’t just set quality objectives for the sake of passing an audit—use them to build a better, stronger, and more successful business.
💡 What’s your biggest challenge with ISO 9001 Quality Objectives? Drop a comment below, and let’s discuss!
Looking for More Resources on ISO 9001?
Looking for ISO 9001 Resources Tailored to Your Industry?
If this article helped clarify ISO 9001, take the next step with our industry-focused tools designed to simplify your certification journey:
📦 ISO 9001 Documentation Kits by Industry: Whether you’re in manufacturing, construction, consulting, or healthcare — we have complete, ready-to-use documentation tailored for your sector.
🎓 Online ISO 9001 Training: Learn how to implement ISO 9001 effectively with our easy-to-follow video lessons, real-world examples, and practical exercises.
📋 ISO 9001 Checklist: Download our step-by-step checklist to ensure your QMS meets all the 9001:2015 requirements from start to finish.
These resources are crafted to save you time, reduce stress, and help you achieve certification with confidence. Choose your industry and start now!
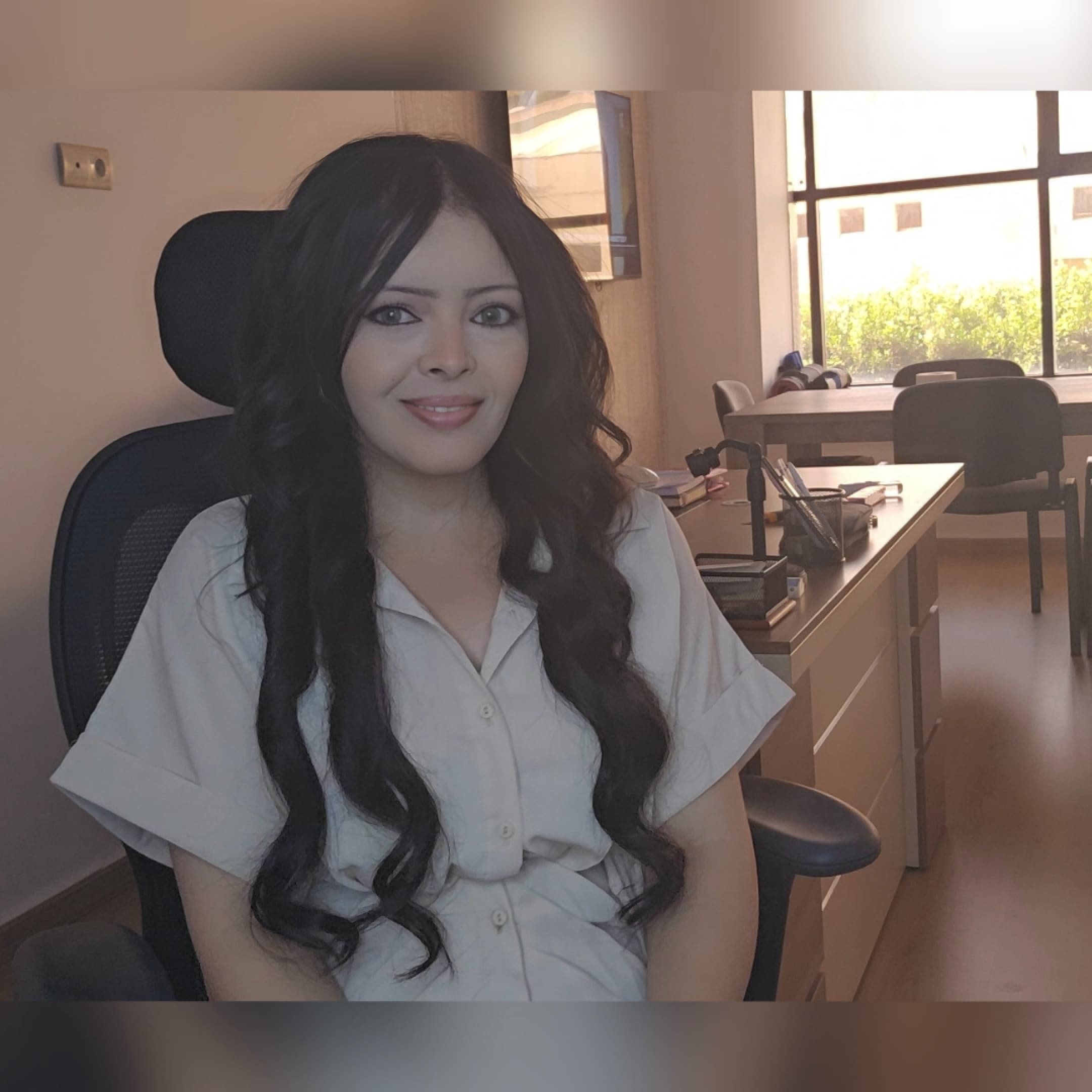
make ISO standards less intimidating and more approachable for everyone.
Whether it’s ISO 9001, ISO 22000, or the cosmetics-focused ISO 22716,
I’ve spent my career turning complex jargon into clear, actionable steps
that businesses can actually use. I’m not here to call myself an expert—I prefer “enthusiast” because I truly love what I do.
There’s something incredibly rewarding about helping people navigate food safety and quality management systems
in a way that feels simple, practical, and even enjoyable.
When I’m not writing about standards, you’ll probably find me playing Piano 🎹, connecting with people, or diving into my next big project💫.
- I’m an engineer specialized in the food and agricultural industry
- I have a Master’s in QHSE management and over 12 years of experience as a Quality Manager
- I’ve helped more than 15 companies implement ISO 9001, ISO 22000, ISO 22716, GMP, and other standards
- My clients include food producers, cosmetics manufacturers, laboratories, and service companies
- I believe quality systems should be simple, useful, and efficient
- Outside of work, I play piano and love learning something new every day
Let’s make ISO less about stress and more about success! 🙏