ISO 9001 Internal Audit Checklist: Essential Tips
Mastering the ISO 9001 Internal Audit Checklist: Essential Tips for Quality Managers and Business Owners
If you’re involved in quality management or business operations, chances are you’ve heard about the ISO 9001 Internal Audit. But let’s be honest—just hearing the word audit can make people nervous. It might bring to mind images of strict checklists, formal inspections, and the looming fear of finding something wrong. But here’s the thing: an ISO 9001 Internal Audit isn’t about catching mistakes—it’s about improving your business from the inside out.
Think of it this way: just like a car needs regular check-ups to keep running smoothly, your business needs internal audits to ensure that processes are efficient, employees are following best practices, and customer satisfaction remains high. The ISO 9001 Internal Audit is your chance to assess what’s working, fix what’s not, and continuously improve—all before an external auditor comes in for a certification review.
In this guide, we’ll break down everything you need to know about the ISO 9001 Internal Audit in a way that makes sense—no confusing jargon, no overwhelming details, just practical, easy-to-follow steps. Whether you’re a quality manager ensuring compliance or a business owner looking to strengthen operations, this article will help you master the internal audit process with confidence.
By the end of this guide, you’ll understand:
What the ISO 9001 Internal Audit is and why it matters.
How to prepare for an internal audit without stress.
The key areas to focus on to ensure compliance.
How to use audit findings to improve your business and avoid surprises in external audits.
The best part? Conducting a strong ISO 9001 Internal Audit isn’t just about passing a test—it’s about building a business that runs smoothly, efficiently, and with top-tier quality. So, let’s dive in and unlock the secrets to internal audit success!
Step 1: Understanding the Purpose of the ISO 9001 Internal Audit
Before diving into checklists and audit steps, let’s take a moment to understand why the ISO 9001 Internal Audit matters. Many people assume that internal audits are just a formality—something you have to do to maintain certification. But in reality, they’re one of the most powerful tools for improving your business.
The ISO 9001 Internal Audit isn’t about ticking boxes or finding fault. It’s about assessing your processes, identifying areas for improvement, and ensuring your Quality Management System (QMS) is actually working in practice. Think of it as a business health check—it helps you spot small issues before they turn into big problems.
Why the ISO 9001 Internal Audit is Important
So, why does the ISO 9001 Internal Audit matter? Here are some key reasons:
- Ensures Compliance – ISO 9001 requires businesses to regularly review their processes to ensure they meet quality standards. An internal audit is your way of staying on track.
- Prepares You for External Audits – Nobody wants surprises during a certification audit. A well-executed ISO 9001 Internal Audit helps you catch and fix non-conformities before an external auditor does.
- Improves Business Efficiency – By evaluating your processes, you can identify bottlenecks, inefficiencies, or outdated procedures that might be slowing down productivity.
- Enhances Customer Satisfaction – A strong Quality Management System means fewer errors, better service, and happier customers. Internal audits help ensure that your business consistently meets customer expectations.
- Encourages a Culture of Continuous Improvement – The ISO 9001 Internal Audit is not a one-time event—it’s a regular check-in that keeps your company moving forward, adapting to changes, and continuously improving.
Who is Responsible for the ISO 9001 Internal Audit?
An ISO 9001 Internal Audit isn’t something that one person can handle alone. It’s a team effort that requires input from different departments. Here’s who should be involved:
- Internal Auditors – These are trained employees (or external consultants) who conduct the audit. They should be impartial—meaning they shouldn’t audit their own department.
- Quality Managers – The quality manager typically oversees the audit, ensuring that findings are documented and corrective actions are taken.
- Department Leaders – Managers from different areas of the business help provide insight into how their processes align with ISO 9001 standards.
- Top Management – Leadership should be involved in reviewing audit results and supporting continuous improvement efforts.
Having the right team in place ensures that the ISO 9001 Internal Audit is not just an exercise in compliance, but a meaningful tool for business growth and success.
How Often Should You Conduct an ISO 9001 Internal Audit?
A common question is: How often should we do an internal audit? The answer depends on several factors, but as a general rule:
- At least once a year – To maintain ISO 9001 certification, an internal audit must be conducted annually.
- More frequently for high-risk processes – If certain areas of your business have a history of non-conformities, you may want to audit them quarterly or semi-annually.
- Before an external audit – Many companies schedule an internal audit a few months before their external certification audit to catch any last-minute issues.
- Whenever there are major changes – If you introduce new processes, software, or policies, an internal audit can help ensure a smooth transition.
The key is to make internal audits a proactive part of your quality management strategy, rather than just something you scramble to do before an external review.
Final Thoughts: Internal Audits as a Business Tool, Not a Burden
If you’ve ever seen an internal audit as a chore, it’s time to shift your mindset. The ISO 9001 Internal Audit is an opportunity to fine-tune your business, eliminate inefficiencies, and improve customer satisfaction. It’s not about finding faults—it’s about finding ways to do better.
Now that we understand why internal audits matter, let’s move on to the next step: how to prepare for a successful ISO 9001 Internal Audit.
Step 2: Preparing for the ISO 9001 Internal Audit
So, you’re ready to conduct an ISO 9001 Internal Audit—but where do you start? Jumping into an audit without preparation is like heading into an exam without studying. To make the process smooth and stress-free, proper preparation is key.
The good news? Preparing for an ISO 9001 Internal Audit doesn’t have to be complicated. With the right steps, you can ensure your audit is thorough, efficient, and effective—helping your business stay compliant and continuously improve.
Let’s go over how to set yourself up for a successful ISO 9001 Internal Audit.
Laying the Groundwork for a Smooth Internal Audit
Before the audit begins, you need to establish a clear plan. The goal is to ensure your team knows what to expect and that everything is in place for a productive review.
Here’s what you need to do before starting the ISO 9001 Internal Audit:
- Review Previous Audit Results – If your business has undergone previous internal or external audits, start by looking at past reports. Were there any non-conformities or areas for improvement? If so, have they been addressed?
- Update Your Documentation – The ISO 9001 Internal Audit relies on well-documented policies, procedures, and records. Make sure your Quality Management System (QMS) documents are up to date and reflect actual business practices.
- Train Your Audit Team – If your company has an internal audit team, ensure they are properly trained in ISO 9001 auditing techniques. Auditors should have a solid understanding of ISO 9001 standards, process evaluation, and objective reporting.
- Set the Audit Scope and Schedule – Define which areas of the business will be audited, the timeframe for the audit, and the objectives you want to achieve. Will this audit focus on specific processes, departments, or the entire organization?
- Notify Employees – A great ISO 9001 Internal Audit isn’t about catching people off guard—it’s about ensuring processes are working as they should. Let employees know in advance that an audit is coming and explain its purpose. This helps to create a positive and cooperative audit environment.
Creating an Effective ISO 9001 Internal Audit Plan
A well-structured ISO 9001 Internal Audit starts with a detailed audit plan. This document acts as a roadmap, guiding your audit team through the process while ensuring nothing important is overlooked.
Your audit plan should include:
- Audit Objectives – What do you hope to achieve? Examples: Ensuring compliance, identifying inefficiencies, or preparing for an external audit.
- Scope of the Audit – Will you be auditing the entire QMS, or just specific processes, departments, or locations?
- Audit Criteria – The standards and requirements you will be auditing against—these should be based on ISO 9001:2015 requirements, company policies, and past audit findings.
- Audit Team & Responsibilities – Assign roles to your audit team members, ensuring they are independent of the processes they are auditing.
- Audit Schedule – Establish a timeline for each phase of the audit, including document review, process observation, employee interviews, and reporting.
- Audit Checklist – Prepare an ISO 9001 Internal Audit checklist (which we’ll discuss in the next section) to keep the audit structured and focused.
Why Preparation is Key to a Successful Internal Audit
Skipping preparation is one of the biggest mistakes businesses make when conducting an ISO 9001 Internal Audit. Without a plan, audits can become disorganized, inefficient, and stressful—leading to missed opportunities for improvement.
By taking the time to review past audits, update documentation, train auditors, and develop a structured audit plan, you set the stage for a productive audit that genuinely benefits your business.
Now that you’re prepared, it’s time to dive into the heart of the audit—the ISO 9001 Internal Audit Checklist. This checklist will guide you through the essential areas to review, ensuring a thorough and effective evaluation. Let’s get into it!
Step 3: The ISO 9001 Internal Audit Checklist – What to Include
Now that you’ve got a solid plan in place, it’s time to focus on the tool that will make your ISO 9001 Internal Audit smooth and effective—the audit checklist. This checklist is your roadmap, guiding you through all the key areas that need to be reviewed to ensure compliance with ISO 9001 standards.
Think of it like a pre-flight checklist for a pilot—it ensures that nothing important is missed and that all systems are functioning as they should. A well-structured ISO 9001 Internal Audit checklist keeps the audit focused, organized, and efficient. So, what should be on it? Let’s dive in.
Why an ISO 9001 Internal Audit Checklist is Essential
A checklist is more than just a piece of paper—it’s a powerful tool that helps:
Ensure consistency – Every audit follows the same structured approach, covering all critical areas.
Improve efficiency – Auditors know exactly what to look for, reducing wasted time and confusion.
Identify gaps easily – A checklist highlights non-conformities and opportunities for improvement.
Keep records organized – Having a documented checklist makes it easier to track findings, corrective actions, and future improvements.
With these benefits in mind, let’s look at what a comprehensive ISO 9001 Internal Audit checklist should include.
Key Areas to Include in Your ISO 9001 Internal Audit Checklist
Your ISO 9001 Internal Audit checklist should cover all major components of your Quality Management System (QMS). Here’s what to include:
1. Quality Policy & Objectives
Is there a documented quality policy that aligns with the company’s goals?
Are quality objectives measurable, realistic, and regularly reviewed?
Do employees understand the quality policy and how it applies to their work?
2. Process Compliance & Effectiveness
Are all documented processes and procedures being followed correctly?
Are process owners aware of their responsibilities within the QMS?
Is there evidence of continuous improvement efforts?
3. Risk-Based Thinking & Preventive Actions
Has the company identified risks and opportunities that could impact quality?
Are risk mitigation strategies in place and being implemented?
Are preventive actions documented and reviewed regularly?
4. Corrective & Preventive Actions
Are non-conformities identified and addressed in a timely manner?
Are root causes of issues being properly investigated?
Are corrective actions effective in preventing the same issues from recurring?
5. Customer Satisfaction & Feedback Management
Is customer feedback collected and analyzed regularly?
Are complaints and negative feedback handled efficiently?
Is customer satisfaction improving over time?
6. Employee Training & Competency
Are employees properly trained for their roles?
Is there a system for tracking training records and certifications?
Do employees understand how their work impacts the ISO 9001 QMS?
7. Document Control & Record-Keeping
Are documents and records updated, properly stored, and easily accessible?
Are outdated documents removed from circulation?
Is there a document control process in place?
8. Internal Communication & Employee Awareness
Do employees have clear communication channels for quality-related issues?
Are quality policies and objectives communicated effectively?
Is there a culture of open feedback and improvement?
9. Supplier & External Provider Management
Are suppliers and service providers meeting quality requirements?
Is there a process for evaluating and selecting suppliers?
Are supplier non-conformities addressed and documented?
How to Use the ISO 9001 Internal Audit Checklist Effectively
Having a checklist is great, but how you use it is what really makes a difference. Here are some best practices to get the most out of your ISO 9001 Internal Audit checklist:
- Customize the Checklist – Tailor it to fit your company’s unique processes and priorities. No two businesses operate the same way, so your checklist should reflect your specific operations and risks.
- Use It as a Guide, Not a Script – Auditors should use the checklist as a framework, but they should also ask follow-up questions and dig deeper where needed.
- Document Findings Clearly – If a process doesn’t meet ISO 9001 standards, write down exactly what’s wrong and suggest corrective actions. The more detailed the findings, the easier it will be to fix issues.
- Involve Employees in the Process – Employees should feel comfortable discussing how they perform their tasks. A collaborative approach leads to better insights and real improvements.
- Review and Update the Checklist Regularly – The ISO 9001 Internal Audit checklist should evolve as your company grows and processes change. Keeping it up to date ensures continuous compliance and efficiency.
Final Thoughts: Your Internal Audit Checklist is Your Secret Weapon
A well-crafted ISO 9001 Internal Audit checklist is one of the best tools you can have to ensure compliance, efficiency, and continuous improvement. It helps businesses stay on top of quality standards, prepare for external audits, and refine internal processes—all of which contribute to long-term success.
Now that you have your checklist in place, it’s time to move on to the next step—conducting the ISO 9001 Internal Audit itself. This is where we put everything into action, ensuring that your business is not just meeting standards but excelling in quality management. 🚀 Stay tuned!
Step 4: Conducting the ISO 9001 Internal Audit – Putting the Checklist into Action
Now that you’ve got your ISO 9001 Internal Audit checklist ready, it’s time to roll up your sleeves and put it into action. This is where the real work happens—where you assess your business’s Quality Management System (QMS) to ensure it meets ISO 9001 standards and uncover opportunities for improvement.
If you’ve never conducted an ISO 9001 Internal Audit before, don’t worry! It’s not about playing detective or pointing fingers. Instead, think of it as a friendly health check for your business—a chance to fine-tune processes, eliminate inefficiencies, and ensure your team is set up for success.
Let’s break down the ISO 9001 Internal Audit into simple, manageable steps.
Step-by-Step Guide to Conducting an ISO 9001 Internal Audit
A great ISO 9001 Internal Audit follows a structured process to ensure consistency and effectiveness. Here’s how to do it:
1. Start with an Opening Meeting
Before diving into the audit, hold a brief meeting with relevant team members. The goal here is to:
Explain the purpose of the ISO 9001 Internal Audit—that it’s about improvement, not blame.
Clarify the scope of the audit—which processes, departments, or locations will be assessed.
Answer any questions and encourage open communication.
A friendly, transparent approach helps employees feel more comfortable and engaged during the audit.
2. Conduct Process Walkthroughs & Observations
Now it’s time to see things in action. Using your ISO 9001 Internal Audit checklist, go through each department or process and:
Observe daily operations – Are procedures being followed as documented?
Check for compliance – Do actual practices align with ISO 9001 standards?
Look for inefficiencies – Are there bottlenecks, unnecessary steps, or risks that could impact quality?
Take notes as you go. If something isn’t working as expected, make a note of it for further investigation.
3. Interview Employees & Gather Insights
A great ISO 9001 Internal Audit isn’t just about reviewing documents—it’s about understanding how processes work from the people who use them daily.
Here’s how to make the most of employee interviews:
Ask open-ended questions – Instead of “Do you follow this procedure?” try “Can you walk me through how you handle this process?”
Encourage honest feedback – Employees often know where problems exist—so make it safe for them to share insights.
Check knowledge of quality policies – Employees should understand how their work contributes to the company’s quality goals.
Remember, this isn’t an interrogation! It’s about learning and improving together.
4. Review Documents & Records
A crucial part of the ISO 9001 Internal Audit is ensuring that all necessary documentation is accurate, up to date, and properly maintained.
Check that:
Quality policies and objectives are documented and accessible.
Training records show that employees have the required skills and knowledge.
Customer feedback and complaint records are being reviewed and acted upon.
Corrective and preventive action reports are available and updated.
Document control procedures are in place to prevent outdated information from being used.
Proper documentation is a key part of ISO 9001 compliance, so take the time to review and verify records carefully.
5. Identify Non-Conformities & Areas for Improvement
As you go through the audit, you’ll likely come across non-conformities—areas where your company isn’t fully meeting ISO 9001 requirements. That’s okay! The purpose of an ISO 9001 Internal Audit is to find and fix these issues before an external audit.
Classify non-conformities – Are they minor (small procedural gaps) or major (significant risks to quality or compliance)?
Investigate the root cause – Why did this non-conformity happen? What needs to change to prevent it from happening again?
Document everything – Clearly record findings so that they can be addressed in the next step.
Spotting and correcting non-conformities early prevents bigger problems later on.
6. Hold a Closing Meeting & Discuss Findings
Once the audit is complete, gather your team for a closing meeting to review the results. This is your chance to:
Highlight what’s working well – Celebrate strengths and successes!
Discuss non-conformities – Explain any issues found and why they matter.
Propose corrective actions – Outline the next steps to fix any gaps and improve processes.
Encourage ongoing improvement – Reinforce the idea that audits are learning experiences, not punishments.
A positive, solution-focused closing meeting helps build engagement and accountability.
Making the Most of Your ISO 9001 Internal Audit
The success of your ISO 9001 Internal Audit doesn’t just depend on finding non-conformities—it depends on how you act on them.
Here’s how to get the most value from your audit:
Take Action Immediately – Address issues as soon as possible to prevent recurring problems.
Follow Up Regularly – Schedule follow-ups to ensure corrective actions are effective.
Use Findings for Continuous Improvement – Every audit is an opportunity to strengthen your business and enhance customer satisfaction.
When done right, the ISO 9001 Internal Audit becomes a powerful tool for growth, helping your business stay compliant, efficient, and ahead of the competition.
Now that we’ve covered how to conduct the audit, the next step is addressing non-conformities and implementing corrective actions. This is where real change happens, ensuring that your audit findings lead to tangible improvements. Let’s dive in!
Step 5: Addressing Non-Conformities and Implementing Corrective Actions in the ISO 9001 Internal Audit
So, you’ve completed your ISO 9001 Internal Audit, and now you have a list of findings—some good, some not-so-good. But don’t worry! Discovering non-conformities (a fancy way of saying “things that aren’t quite right”) is actually a great opportunity to make meaningful improvements.
The key to a successful ISO 9001 Internal Audit isn’t just identifying gaps—it’s what you do next. Taking corrective action ensures that issues don’t keep coming up, making your business stronger, more efficient, and ready for external audits.
Let’s break down how to effectively address non-conformities and implement corrective actions that actually make a difference.
What Are Non-Conformities in the ISO 9001 Internal Audit?
A non-conformity happens when a process, policy, or action does not fully meet ISO 9001 requirements. These can range from minor issues (like a missing document signature) to major gaps (like a failure to follow key quality procedures).
Here’s how non-conformities are typically classified:
- Minor Non-Conformity – A small issue that doesn’t directly impact product/service quality but still needs correction. Example: An outdated work instruction document being used.
- Major Non-Conformity – A serious issue that affects compliance, efficiency, or customer satisfaction. Example: A critical quality control step being skipped in production.
No matter how big or small the issue is, ISO 9001 Internal Audits are designed to catch and correct them before they become real problems.
Step-by-Step Guide to Corrective Actions After an ISO 9001 Internal Audit
Once a non-conformity is identified, it’s time to dig deeper and fix the root cause. Here’s how to do it effectively:
1. Document the Non-Conformity Clearly
First things first—write down exactly what went wrong. A good non-conformity report should answer:
- What was found? (Example: Employee training records were incomplete.)
- Where was it found? (Example: In the Human Resources training database.)
- Why is it a problem? (Example: ISO 9001 requires documented evidence of employee competence.)
Clearly documenting issues makes it easier to track progress and show auditors that corrective actions were taken seriously.
2. Investigate the Root Cause (Don’t Just Treat the Symptoms!)
Many businesses make the mistake of fixing the surface problem without digging into why it happened in the first place. That’s like putting a bandage on a leak instead of fixing the pipe!
Use Root Cause Analysis (RCA) techniques like:
The 5 Whys – Keep asking “why” until you find the real reason behind the issue.
Fishbone Diagram (Ishikawa Analysis) – Visually map out possible causes related to people, processes, materials, and machines.
For example, if a supplier consistently delivers defective materials, don’t just reject their shipments—ask:
Why is this happening? → Poor supplier quality control.
Why is that happening? → No proper supplier audits.
Why is that happening? → Lack of clear supplier requirements.
Now, instead of just rejecting materials, you might decide to strengthen supplier evaluation procedures—a long-term fix.
3. Develop a Corrective Action Plan
Once the root cause is identified, create a corrective action plan to fix the issue and prevent it from happening again.
A strong corrective action plan should include:
What needs to be fixed? (Example: Update training procedures and ensure all employee certifications are logged.)
Who is responsible? (Example: HR manager will update records; department heads will verify completion.)
Deadline for completion? (Example: Training records to be updated within 30 days.)
How will effectiveness be checked? (Example: Conduct an internal spot-check in 3 months.)
The goal is not just to fix problems, but to improve processes so they don’t come back later.
4. Implement and Monitor the Corrective Action
Now it’s time to put your plan into action. But taking corrective action isn’t just about fixing the issue today—it’s about ensuring the fix works long-term.
Here’s how to monitor corrective actions effectively:
Track Progress – Assign responsibility and set reminders to check if corrective actions were completed.
Verify Effectiveness – Conduct follow-up audits or process reviews to see if the problem is truly resolved.
Update Procedures – If changes were made to processes, update your QMS documents accordingly.
By continuously monitoring corrective actions, your business builds a culture of improvement, making future ISO 9001 Internal Audits easier and more successful.
Turning ISO 9001 Internal Audit Findings into Business Improvements
The ISO 9001 Internal Audit isn’t just about fixing what’s broken—it’s about making your business stronger, more efficient, and more resilient.
Here’s how you can use audit findings to drive continuous improvement:
Share Lessons Learned – Instead of just fixing an issue in one department, share best practices across teams.
Encourage Employee Involvement – Employees often see inefficiencies before managers do—get them involved in finding solutions.
Use Data for Decision-Making – Track audit trends over time. Are certain issues coming up repeatedly? If so, it might be time for a bigger process change.
Final Thoughts: The Power of Corrective Actions in the ISO 9001 Internal Audit
Fixing non-conformities and implementing corrective actions is where the real value of an ISO 9001 Internal Audit comes in. It’s not just about checking a compliance box—it’s about continuously improving your business so that it runs smoother, delivers higher quality, and stays ahead of risks.
By following these steps—documenting findings, investigating root causes, creating a corrective action plan, and monitoring improvements—your ISO 9001 Internal Audit becomes a powerful business optimization tool, not just a routine check.
Now that you’ve addressed non-conformities, it’s time to take your internal audits to the next level. In the next section, we’ll cover best practices for a truly effective ISO 9001 Internal Audit—helping your business go beyond compliance and into long-term quality excellence. Stay tuned!
Step 6: Best Practices for a Successful ISO 9001 Internal Audit
Now that you know how to conduct an ISO 9001 Internal Audit and address non-conformities, let’s take it a step further. How do you turn your internal audits into a powerful tool for continuous improvement—not just a compliance exercise?
A great ISO 9001 Internal Audit goes beyond simply checking boxes. It’s about identifying opportunities, strengthening processes, and ensuring long-term success. When done right, internal audits can streamline operations, reduce risks, and build a culture of quality within your organization.
Here are the best practices that will take your ISO 9001 Internal Audit from “just another requirement” to a game-changer for your business.
1. Approach the ISO 9001 Internal Audit with a Positive Mindset
Many businesses see audits as a necessary evil, something they have to do rather than want to do. But here’s the truth: the ISO 9001 Internal Audit is an opportunity to improve, innovate, and stay ahead of problems.
Instead of treating the audit as a fault-finding mission, shift the mindset to:
How can we improve efficiency?
Are there ways to simplify our processes?
What’s working really well that we should do more of?
By making the audit a constructive experience, employees will be more open, honest, and engaged—leading to better results and real improvements.
2. Use a Risk-Based Approach
ISO 9001 places a strong emphasis on risk-based thinking, and your internal audits should reflect this.
Instead of treating all areas of your business the same, prioritize high-risk processes—those that have the biggest impact on:
Customer satisfaction
Product/service quality
Regulatory compliance
Operational efficiency
By focusing on critical areas first, your ISO 9001 Internal Audit will have a bigger impact on business performance.
3. Keep Audits Objective & Unbiased
One of the biggest mistakes in internal audits is lack of objectivity. If employees audit their own work, there’s a risk of bias or oversight.
To maintain audit integrity, follow these best practices:
Assign trained internal auditors who are independent of the process they’re auditing.
Consider using cross-department audits, where one team audits another.
If needed, bring in an external consultant for a fresh perspective.
An objective ISO 9001 Internal Audit ensures real issues are identified and addressed—rather than just giving the illusion of compliance.
4. Communicate Clearly & Involve Employees
A great ISO 9001 Internal Audit is collaborative. It’s not just about auditors reviewing documents—it’s about engaging employees, gathering insights, and working together.
Before the audit – Let employees know what to expect and why audits are important.
During the audit – Encourage open discussions, listen to feedback, and create a non-intimidating atmosphere.
After the audit – Share results transparently, celebrate strengths, and provide guidance on improvements.
When employees feel involved and valued, they’re more likely to embrace ISO 9001 principles in their daily work.
5. Focus on Continuous Improvement, Not Just Compliance
The biggest difference between a basic audit and a great audit is the mindset.
A basic ISO 9001 Internal Audit checks whether processes meet requirements.
A great ISO 9001 Internal Audit asks: How can we do this better?
To truly leverage the audit process, focus on:
Finding inefficiencies – Are there unnecessary steps slowing things down?
Enhancing customer satisfaction – Are there ways to improve service quality?
Optimizing workflows – Can technology or automation improve processes?
By making continuous improvement the core goal, internal audits become valuable business tools, not just compliance exercises.
6. Document Everything Clearly & Track Progress
An ISO 9001 Internal Audit is only as useful as the actions taken afterward. To ensure improvements actually happen:
Keep detailed records – Document findings, corrective actions, and deadlines.
Assign responsibility – Make sure someone is accountable for addressing each issue.
Follow up regularly – Check progress and confirm corrective actions were implemented.
Use past audits as a benchmark – Compare findings over time to track improvement.
By maintaining clear records, your business will always be prepared for external audits and future quality improvements.
7. Don’t Let Audits Become a “Once-a-Year Event”
A common mistake is treating the ISO 9001 Internal Audit as a one-time event, done only to prepare for an external audit. But to truly benefit, audits should be ongoing and proactive.
Here’s how to keep quality top-of-mind year-round:
Conduct smaller, focused internal audits throughout the year.
Set up regular performance reviews to track compliance.
Create a culture where employees report and fix issues proactively—not just during audits.
The more integrated internal audits are into daily operations, the stronger your Quality Management System (QMS) will be.
Final Thoughts: Making the Most of the ISO 9001 Internal Audit
A successful ISO 9001 Internal Audit is so much more than a routine check—it’s a powerful tool for growth, efficiency, and continuous improvement.
By following best practices like:
Approaching audits positively and constructively
Using a risk-based approach to focus on critical areas
Keeping audits objective and unbiased
Engaging employees and encouraging open communication
Tracking progress and turning findings into real improvements
Making audits an ongoing part of business operations
… your ISO 9001 Internal Audit will do more than just meet compliance requirements—it will transform your business for the better.
Now that you’ve mastered best practices, the next step is preparing for external audits and certification. We’ll walk you through how the ISO 9001 Internal Audit sets the stage for a successful certification audit, ensuring your business gets—and stays—ISO 9001 certified. Stay tuned!
Step 7: Preparing for External Audits with the ISO 9001 Internal Audit
So, you’ve successfully conducted your ISO 9001 Internal Audit—you’ve checked processes, identified areas for improvement, and implemented corrective actions. Now, the big question is: Are you ready for the external audit?
The ISO 9001 certification audit is the final step in proving that your Quality Management System (QMS) meets the required standards. But here’s the good news: If you’ve conducted a thorough and well-planned ISO 9001 Internal Audit, you’re already on the right path!
Think of your internal audit as a practice run for the external audit. It helps you find and fix potential non-conformities before the certification body arrives, making the process smoother, less stressful, and more successful.
Let’s go over how to use your ISO 9001 Internal Audit to fully prepare for certification and ensure your business is set up for success.
How the ISO 9001 Internal Audit Prepares You for External Certification
The ISO 9001 Internal Audit serves as your first line of defense when preparing for external audits. Here’s how it helps:
Identifies and corrects non-conformities before the external auditor finds them.
Ensures all documentation is up to date and accessible for review.
Gives employees confidence by familiarizing them with the audit process.
Strengthens compliance with ISO 9001 requirements, reducing the risk of failing certification.
Demonstrates a proactive approach to quality management, which auditors appreciate.
By taking the internal audit seriously, you reduce surprises during the external audit and increase your chances of achieving ISO 9001 certification smoothly.
What External Auditors Look For in the ISO 9001 Certification Audit
During the ISO 9001 certification audit, an external auditor will evaluate whether your business meets ISO 9001 standards. They typically focus on:
Compliance with ISO 9001 Requirements – Are all necessary processes and policies in place?
Documented Evidence – Is there proof that procedures are being followed?
Employee Knowledge & Involvement – Can employees explain their role in maintaining quality?
Corrective Actions from Internal Audits – Have past issues been addressed effectively?
Continuous Improvement Efforts – Is the company committed to ongoing quality enhancements?
A well-executed ISO 9001 Internal Audit ensures that all of these areas are in great shape before the external auditor steps in.
How to Use Your ISO 9001 Internal Audit to Prepare for Certification
Here’s a step-by-step approach to ensure your internal audit fully prepares you for the ISO 9001 certification audit:
1. Conduct a Final Internal Audit Review
Before your external audit, do a final review of your ISO 9001 Internal Audit findings to confirm that:
All non-conformities have been resolved and corrective actions are in place.
Documentation is complete and well-organized, including policies, procedures, and records.
Employees are confident in their roles and understand ISO 9001 requirements.
This last internal review acts as a quality check before the real thing.
2. Organize and Review Key Documents
One of the most important aspects of an ISO 9001 certification audit is documentation. External auditors will want to see proof that your QMS is functioning properly.
Make sure you have:
A Quality Manual outlining your QMS structure and objectives.
Process documentation to show how key operations are managed.
Internal audit reports that demonstrate compliance and corrective actions.
Training records proving employees are properly trained.
Customer feedback reports to show how you manage quality improvements.
Having these documents ready ensures a smooth, efficient audit with fewer delays.
3. Conduct a Mock Audit (Audit Simulation)
A great way to build confidence before the external audit is to conduct a mock audit. This simulates the certification audit and helps your team get comfortable with the process.
How to run a mock audit:
Use your ISO 9001 Internal Audit checklist to perform a full review of compliance.
Have an independent auditor or external consultant assess your QMS.
Encourage employees to answer questions as if they were speaking to an external auditor.
Identify any remaining weak areas and correct them before the real audit.
A mock audit helps eliminate last-minute surprises, ensuring your team is fully prepared and confident.
4. Prepare Employees for Auditor Interviews
One of the most common concerns before an external audit is employee interviews. Auditors often ask employees questions to verify that ISO 9001 processes are being followed in daily operations.
Here’s how to help employees feel prepared and confident:
Explain the purpose of the audit – It’s about improving the business, not finding faults.
Review key quality objectives – Employees should understand how their work contributes to quality.
Encourage honesty – If employees don’t know the answer to a question, they should be honest and explain where they would find the information.
Practice common audit questions – Hold a Q&A session to go over potential auditor questions.
By ensuring employees are comfortable with the audit process, you create a positive audit experience for everyone.
5. Be Proactive and Stay Organized on Audit Day
When the day of the ISO 9001 certification audit arrives, staying calm and organized is key.
Assign a main contact person – This helps keep communication smooth with the auditor.
Have all documents readily available – Don’t waste time scrambling for missing paperwork.
Encourage a positive, open approach – Auditors appreciate businesses that are proactive, honest, and engaged in the process.
If the auditor finds a minor issue, don’t panic! Certification bodies often allow businesses to make small corrections after the audit to maintain compliance.
Final Thoughts: Using the ISO 9001 Internal Audit as a Springboard for Certification
The ISO 9001 certification audit may feel like a big moment, but with a well-executed ISO 9001 Internal Audit, you’ll be fully prepared.
By taking the time to:
Conduct thorough internal audits and address non-conformities,
Organize documentation and records,
Run mock audits to boost confidence,
Prepare employees for auditor interviews,
Maintain a proactive and engaged attitude,
… you set your business up for a smooth, stress-free certification audit.
Remember, the ISO 9001 Internal Audit isn’t just a preparation tool—it’s a long-term strategy for ensuring continuous improvement and quality excellence.
Now that you’re equipped with everything you need to ace the ISO 9001 certification audit, it’s time to move forward with confidence. Your business is on its way to achieving ISO 9001 certification—and maintaining it for years to come!
Step 8: Maintaining Long-Term Compliance After the ISO 9001 Internal Audit
Congratulations! You’ve successfully conducted your ISO 9001 Internal Audit, corrected non-conformities, and even prepared for the external audit. But here’s the thing—ISO 9001 compliance isn’t a one-time achievement; it’s an ongoing commitment.
Many businesses make the mistake of treating the ISO 9001 Internal Audit as a once-a-year event, just to tick the compliance box. But the real value of internal audits comes from using them as a continuous improvement tool. By making audits a regular part of your business operations, you ensure that quality remains a priority every single day.
So, how do you maintain compliance long after the audit is over? Let’s dive into the strategies that will keep your ISO 9001 system strong and effective for the long haul.
1. Schedule Regular ISO 9001 Internal Audits (Not Just Once a Year!)
One of the biggest mistakes businesses make? Only conducting an ISO 9001 Internal Audit when the certification renewal is coming up.
Instead, set up a regular audit schedule throughout the year to keep your Quality Management System (QMS) running smoothly. Here’s a simple way to structure it:
Quarterly mini-audits – Focus on high-risk processes and key quality areas.
Departmental audits – Rotate between departments to assess compliance and efficiency.
Annual full internal audit – Conduct a complete ISO 9001 Internal Audit before your external audit to ensure everything is in top shape.
Frequent audits make compliance a normal part of business operations, reducing stress when certification audits come around.
2. Keep Employees Engaged with ISO 9001 Principles
A strong ISO 9001 Internal Audit isn’t just about policies and procedures—it’s about people. If employees don’t understand or embrace ISO 9001, maintaining compliance becomes a challenge.
Here’s how to keep your team engaged:
Regular training sessions – Offer refresher courses on ISO 9001 principles and best practices.
Interactive workshops – Make quality training engaging with real-life scenarios and hands-on activities.
Encourage employee feedback – Employees working directly with processes often have the best insights on where improvements are needed.
Recognize and reward quality efforts – Celebrate employees who actively contribute to quality improvements.
When employees see ISO 9001 as part of their daily work, maintaining compliance becomes second nature.
3. Continuously Improve Your Quality Management System (QMS)
ISO 9001 isn’t about staying the same—it’s about getting better over time. Use your ISO 9001 Internal Audit findings to drive ongoing improvements.
Here’s how to make continuous improvement a habit:
Analyze audit trends – Are the same issues popping up in every audit? If so, it’s time to adjust your processes.
Implement corrective actions promptly – Don’t just document issues—fix them and monitor the results.
Set measurable quality objectives – Define goals that encourage innovation and efficiency.
Leverage customer feedback – Use customer input to refine and enhance your processes.
By continuously refining your Quality Management System, you not only maintain ISO 9001 compliance—you stay ahead of the competition.
4. Prepare for Surveillance Audits & Recertification
After achieving ISO 9001 certification, you’ll need to undergo annual surveillance audits to ensure you’re still meeting the standard’s requirements. These audits are conducted by your certification body to confirm that your QMS remains compliant.
How to stay prepared:
Keep all documentation up to date – Don’t wait until an audit is scheduled to update policies and records.
Monitor previous non-conformities – Ensure that past issues have been fully resolved and improvements sustained.
Use internal audits as pre-checks – Treat each ISO 9001 Internal Audit as a preparation step for surveillance audits.
And remember, every three years, you’ll need to undergo a full recertification audit. Staying proactive with your ISO 9001 Internal Audit process ensures that recertification is smooth and stress-free.
5. Leverage ISO 9001 Certification as a Competitive Advantage
Being ISO 9001 certified isn’t just about compliance—it’s a powerful business tool. Many customers, suppliers, and partners look for ISO 9001 certification as a sign of reliability, quality, and trustworthiness.
Use your ISO 9001 Internal Audit results to strengthen your business reputation:
Showcase your certification on your website, marketing materials, and proposals.
Highlight quality improvements in customer communications.
Use audit findings to refine operations and stand out from competitors.
By actively promoting your ISO 9001 certification, you can turn compliance into a business advantage that attracts more customers and partnerships.
Final Thoughts: ISO 9001 Compliance is a Journey, Not a Destination
Completing an ISO 9001 Internal Audit is a major step—but the real challenge is maintaining compliance over time. By making internal audits a regular practice, engaging employees, driving continuous improvement, and staying proactive with surveillance audits, your business will not only remain compliant but thrive with a strong quality management system.
Remember, ISO 9001 isn’t just about passing audits—it’s about building a culture of quality that benefits your business, employees, and customers.
So, what’s next? Take what you’ve learned and make ISO 9001 a living, breathing part of your organization. Keep improving, keep innovating, and watch your business grow with stronger quality practices every day.
Conclusion: Making the ISO 9001 Internal Audit a Powerful Tool for Business Growth
By now, you’ve seen that the ISO 9001 Internal Audit isn’t just a compliance requirement—it’s a powerful tool that can transform your business, improve efficiency, and drive continuous improvement. When done right, internal audits help identify opportunities, reduce risks, and ensure your Quality Management System (QMS) is delivering real value.
But here’s the key takeaway: ISO 9001 Internal Audits should be more than just a checklist exercise. They should be an ongoing practice that strengthens your processes, engages employees, and keeps your business at the forefront of quality.
Let’s quickly recap what we’ve covered:
Understanding the Purpose of the ISO 9001 Internal Audit – Why audits matter and how they contribute to compliance and business success.
Preparing for the Internal Audit – Setting up a structured approach to make the audit smooth and effective.
Using the ISO 9001 Internal Audit Checklist – Ensuring a thorough evaluation of your quality management processes.
Conducting the Internal Audit – Engaging employees, reviewing documents, and identifying areas for improvement.
Addressing Non-Conformities and Implementing Corrective Actions – Turning audit findings into real improvements.
Best Practices for a Successful Internal Audit – Keeping audits objective, engaging, and focused on continuous growth.
Preparing for External Audits and Certification – Using the ISO 9001 Internal Audit to ensure a stress-free external certification process.
Maintaining Long-Term Compliance – Making quality management a daily habit and ensuring ISO 9001 compliance lasts for years.
Your Next Steps: Turning ISO 9001 Internal Audits into a Competitive Advantage
Now that you have a clear roadmap for conducting effective ISO 9001 Internal Audits, here’s how you can apply what you’ve learned:
Schedule your next ISO 9001 Internal Audit – Don’t wait until the last minute! Regular audits keep your QMS strong.
Engage your employees in the process – Quality is a team effort. Make sure your team understands the value of internal audits.
Use audits as a tool for growth – Identify areas for efficiency, innovation, and customer satisfaction improvements.
Stay proactive – Keep refining your audit process, training staff, and tracking improvements over time.
Remember, the ISO 9001 Internal Audit isn’t just about meeting requirements—it’s about building a smarter, stronger, and more resilient business.
So, what’s your next move? Start planning your next ISO 9001 Internal Audit today and take your quality management efforts to the next level!
Looking for More Resources on ISO 9001?
Looking for ISO 9001 Resources Tailored to Your Industry?
If this article helped clarify ISO 9001, take the next step with our industry-focused tools designed to simplify your certification journey:
- ISO 9001 Documentation Kits by Industry: Whether you’re in manufacturing, construction, consulting, or healthcare — we have complete, ready-to-use documentation tailored for your sector.
- Online ISO 9001 Training: Learn how to implement ISO 9001 effectively with our easy-to-follow video lessons, real-world examples, and practical exercises.
- ISO 9001 Checklist: Download our step-by-step checklist to ensure your QMS meets all the 9001:2015 requirements from start to finish.
These resources are crafted to save you time, reduce stress, and help you achieve certification with confidence. Choose your industry and start now!
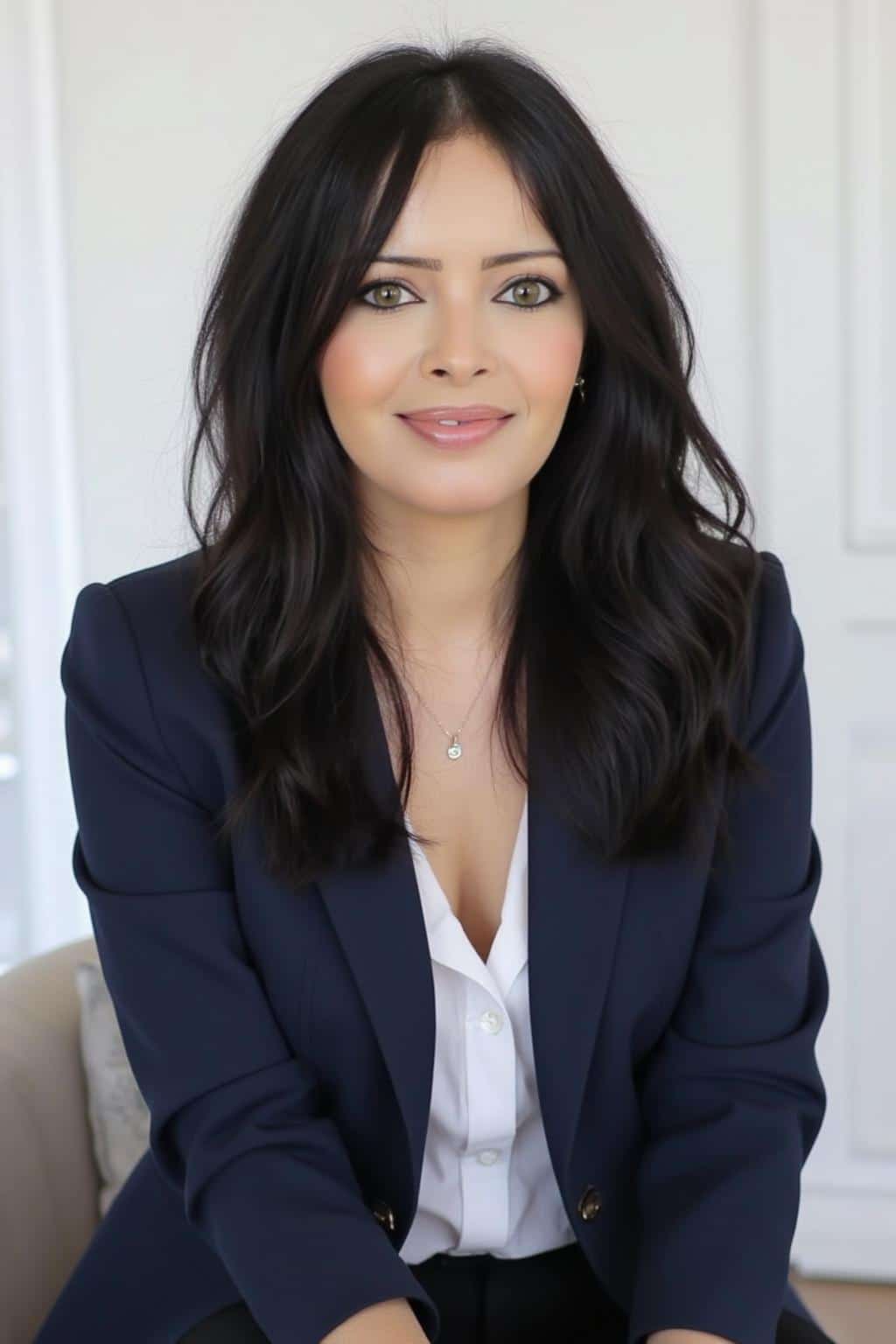
👋 Hi, I’m HAFSA, and for the past 12 years, I’ve been on a journey to
make ISO standards less intimidating and more approachable for everyone.
Whether it’s ISO 9001, ISO 22000, or the cosmetics-focused ISO 22716,
I’ve spent my career turning complex jargon into clear, actionable steps
that businesses can actually use. I’m not here to call myself an expert—I prefer “enthusiast” because I truly love what I do.
There’s something incredibly rewarding about helping people navigate food safety and quality management systems
in a way that feels simple, practical, and even enjoyable.
When I’m not writing about standards, you’ll probably find me playing Piano 🎹, connecting with people, or diving into my next big project💫.
I’m an engineer specialized in the food and agricultural industry
I have a Master’s in QHSE management and over 12 years of experience as a Quality Manager
I’ve helped more than 15 companies implement ISO 9001, ISO 22000, ISO 22716, GMP, and other standards
My clients include food producers, cosmetics manufacturers, laboratories, and service companies
I believe quality systems should be simple, useful, and efficient
Outside of work, I play piano and love learning something new every day
Let’s make ISO less about stress and more about success! 🙏