Quality Assurance vs Quality Control
Quality Assurance vs. Quality Control
Imagine you’re at your favorite restaurant, eagerly waiting for your meal. Behind the scenes, the kitchen is bustling. The chef is meticulously following recipes, ensuring the freshest ingredients are used, and setting up systems to make sure every dish is consistently delicious. Meanwhile, before your plate reaches the table, the waiter takes one last look to check that everything is perfect—no spills, no missing garnish, just as you ordered.
This, my friend, is the difference between Quality Assurance (QA) and Quality Control (QC) in action. QA is like the chef’s thoughtful planning and preparation to ensure the food is amazing, while QC is the waiter’s final check to catch anything that might have gone wrong. Both are crucial to your dining experience—and to pretty much every product or service we rely on in our daily lives.
But what do these terms really mean in the business world, and why should you care? Well, whether you’re running a business, working on a project, or just curious about how things work, understanding QA and QC can give you a whole new perspective on how quality is built and maintained. Let’s dive into it together.
1. What is Quality Assurance?
Alright, let’s talk about Quality Assurance (QA). Think of QA as the blueprint for quality—it’s all about setting up systems and processes to make sure things go right from the very beginning. The focus? Prevention. QA is like laying a strong foundation for a house: if you get it right, everything else is easier to build, and you avoid costly repairs later.
The Basics of QA
At its core, QA is a proactive approach. Instead of waiting for problems to show up, it asks, “How can we design this process so that mistakes don’t happen in the first place?” It’s all about the big picture—creating rules, standards, and systems that guide everyone involved to deliver consistent quality.
How Does QA Work?
Here’s a simple breakdown:
- Processes: QA focuses on how things are done, from start to finish. It’s not about checking individual products but about ensuring that the way they’re made is solid.
- Standards: These are the rules everyone follows to make sure quality isn’t left to chance. For example, an ISO standard like ISO 9001 helps organizations build frameworks to manage quality.
- Training: A big part of QA is teaching the team how to follow processes correctly. After all, even the best system won’t work if no one knows how to use it.
A Real-Life Analogy
Let’s say you’re baking cookies (because, who doesn’t love cookies?). QA would be making sure you:
- Have a clear recipe.
- Use high-quality ingredients.
- Preheat the oven to the right temperature.
- Train everyone in the kitchen on how to follow the steps.
By doing all this, you’re setting yourself up for success. You’ve minimized the chances of burnt cookies or forgotten sugar (we’ve all been there).
Key Tools and Techniques in QA
In the business world, QA uses tools to ensure processes run smoothly. Some of the big ones include:
- Standard Operating Procedures (SOPs): Step-by-step guides that leave no room for guesswork.
- Audits: Regular checks to make sure processes are being followed.
- Risk Assessments: Identifying potential issues before they happen.
Why QA Matters
Without QA, you’re leaving things to chance. A strong QA system ensures that quality isn’t just a happy accident—it’s a built-in feature. Plus, it saves time and money. Imagine catching a potential issue during the planning stage rather than after it’s already caused delays or customer complaints. That’s the power of QA.
2. What is Quality Control?
Now that we’ve talked about Quality Assurance (QA), let’s shift gears to Quality Control (QC). If QA is all about setting the stage, QC is about checking the performance. It’s the final step in the quality process—the one that makes sure the product or service meets expectations before it’s delivered.
The Basics of QC
While QA focuses on preventing problems, QC is there to detect them. It’s like having a safety net. QC checks the output to ensure it aligns with the quality standards set during the QA process. The focus is on the end product or service, not the process.
How Does QC Work?
Here’s a simple explanation:
- Inspection: QC involves examining products or services to find defects or deviations from the standard.
- Testing: In many industries, this means putting products through various tests to confirm they work as intended.
- Documentation: Every inspection or test is recorded, so there’s a clear track of what passed and what didn’t.
A Real-Life Analogy
Imagine you’re assembling furniture. Once you’re done, QC would be like stepping back to check if everything looks right. Is the table sturdy? Are all the screws in place? Does it match the picture on the box? QC catches those little (or big) things that might have gone wrong during assembly.
Here’s another example: Let’s go back to the restaurant analogy. QA was the chef planning and setting up systems in the kitchen. QC is the waiter checking if the plate is clean, the steak is cooked medium rare, and the garnish is on point before serving it to the customer.
Key Tools and Techniques in QC
In the world of QC, the focus is on identifying and fixing defects. Here are some tools that make it happen:
- Checklists: These ensure every product or service meets specific criteria. It’s like having a “to-do” list for quality.
- Sampling: Instead of testing every single item, QC often examines a random sample to ensure quality consistency.
- Statistical Process Control (SPC): This uses data and charts to monitor and control quality during production.
Why QC Matters
Even with the best QA system, mistakes can happen. QC is the safety check that ensures no defective product or subpar service slips through the cracks. It gives businesses the confidence to say, “Yes, this is ready for our customers.”
QC also provides valuable feedback for improvement. If a defect is found, the QC team can trace it back to the process and suggest changes. In this way, QC and QA work together like a well-oiled machine.
QA vs. QC: Working Hand-in-Hand
Both QA and QC are essential for delivering high-quality products and services. QA sets the stage, and QC ensures the performance. Think of it like building and decorating a house: QA is making sure the structure is solid, and QC is checking that the paint job is flawless.
3. Quality Assurance vs Quality Control : Key Differences
Now that we’ve got a good grasp of what Quality Assurance (QA) and Quality Control (QC) are, let’s talk about how they differ. While they work toward the same goal—ensuring quality—they take very different approaches. Think of QA and QC as two sides of the same coin. They complement each other but have distinct roles to play.
Focus: Process vs. Product
- QA is process-oriented. It’s all about designing and managing the processes that lead to quality. The focus is on getting things right from the start.
- QC is product-oriented. It’s about examining the final product or service to make sure it meets the required standards.
Example: In a bakery, QA involves creating the recipes and training the bakers. QC is inspecting the finished cakes to ensure they look and taste perfect.
Timing: Before vs. After
- QA happens before production. It’s proactive, focused on preventing issues from ever occurring.
- QC happens after production. It’s reactive, catching issues that might have slipped through.
Example: In car manufacturing, QA involves setting up processes to ensure every part is assembled correctly. QC involves testing cars at the end of the line to confirm they’re safe and functional.
Responsibility: Everyone vs. Specialists
- QA is everyone’s responsibility. It’s a team effort. From management to employees, everyone contributes to following the systems and processes.
- QC is handled by specialists. The QC team is typically trained to inspect, test, and identify defects.
Example: In a software company, QA might involve the entire team following coding standards and processes. QC would be the testers running the finished software to catch bugs.
Tools: Systems vs. Checks
- QA uses tools like SOPs, audits, and risk assessments. These tools are about building and maintaining the framework for quality.
- QC uses tools like checklists, inspections, and sampling. These tools are focused on verifying that individual products or services meet quality standards.
Goal: Prevention vs. Detection
- QA’s goal is to prevent defects. It’s about building quality into the process so problems don’t arise.
- QC’s goal is to detect defects. It’s about ensuring any issues are identified and addressed before they reach the customer.
Example: QA is like designing a water filtration system to prevent contamination. QC is testing the water that comes out to make sure it’s clean.
Why Both Are Necessary
Now, here’s the thing: QA and QC aren’t competitors—they’re partners. A business that focuses only on QC may catch defects, but it’s often too late and more expensive to fix them. On the other hand, a business that relies solely on QA might overlook mistakes that slip through the cracks.
When QA and QC work together, they create a complete quality management system:
- QA builds the framework and processes to minimize errors.
- QC provides the safety net to catch anything that might go wrong.
Quick Summary:
- QA = Proactive, process-focused, and prevention.
- QC = Reactive, product-focused, and detection.
4. Why Both Quality Assurance vs Quality Control Are Critical
So now you know what Quality Assurance (QA) and Quality Control (QC) are and how they differ. But you might be wondering: “Do I really need both? Can’t I just pick one?” The short answer is: You need both. Here’s why.
QA and QC Are Complementary
QA and QC are like two halves of a perfect partnership. While QA works to prevent mistakes, QC steps in to catch anything that might have slipped through. Together, they create a powerful system that ensures consistent, reliable quality.
Think about a car assembly line:
- QA makes sure the design process, equipment setup, and assembly instructions are flawless.
- QC inspects the finished cars, testing things like brakes and airbags to ensure safety.
Without QA, there’s no structure to guide quality. Without QC, there’s no guarantee that the output meets expectations.
The Real-World Impact of QA and QC
Let’s look at what happens when you rely on only one of these approaches.
- If you skip QA: Imagine building a house without a solid blueprint. Sure, you might catch problems during the final inspection (QC), but fixing a crooked wall or faulty wiring after the fact is expensive and time-consuming.
- If you skip QC: Now imagine designing the perfect blueprint (QA) but never checking if the builders followed it. You could end up with a house where the windows don’t close properly or the roof leaks—and you’d only find out when it rains.
Skipping either step creates gaps in the quality process, which can lead to unhappy customers, higher costs, and damaged reputations.
QA and QC Save Money
Here’s a little-known secret: Prevention is cheaper than correction.
Fixing defects after they’ve been made (or after they’ve reached the customer) costs time, money, and sometimes even your reputation. A strong QA system reduces the chances of defects in the first place, saving resources. QC, on the other hand, ensures you don’t let a bad product slip through, which could cost you even more in refunds, recalls, or lost trust.
Example: A pharmaceutical company that invests in QA by following Good Manufacturing Practices (GMP) minimizes the risk of producing faulty medication. However, QC testing ensures that every batch leaving the factory is safe and effective.
QA and QC Work in Every Industry
You might think QA and QC are just for manufacturing, but they’re everywhere. Let’s look at a few industries:
- Food Industry:
- QA = Implementing HACCP plans to prevent contamination.
- QC = Sampling products to test for bacteria or allergens.
- Software Development:
- QA = Establishing coding standards and best practices.
- QC = Testing the software for bugs before launch.
- Healthcare:
- QA = Training staff and developing processes for patient care.
- QC = Reviewing patient charts to ensure protocols were followed.
- Construction:
- QA = Designing detailed plans and ensuring workers follow safety regulations.
- QC = Inspecting the final structure to confirm it’s safe and up to code.
No matter what field you’re in, QA and QC work together to ensure the best results.
A Happy Customer Is the Ultimate Goal
At the end of the day, QA and QC both serve the same purpose: to make sure the customer gets a high-quality product or service. A customer who receives something flawless is a happy customer—and happy customers stick around, recommend your business, and boost your reputation.
By balancing QA and QC, you’re building trust. Customers know they can count on you for consistent quality, and that’s priceless.
Quick Recap:
- QA prevents mistakes; QC catches the ones that slip through.
- Together, they save time, money, and your reputation.
- They apply to every industry, from food to tech to healthcare.
- Happy customers are the ultimate payoff.
5. Misconceptions About Quality Assurance vs Quality Control
Even though Quality Assurance (QA) and Quality Control (QC) are vital to delivering quality products and services, they’re often misunderstood. Let’s clear up some common misconceptions that might be holding you (or your business) back.
Misconception 1: QA and QC Are the Same
This is probably the most common mix-up. While QA and QC both aim to ensure quality, they couldn’t be more different in their approach.
- QA is about preventing problems: It’s proactive, focusing on the processes that lead to quality.
- QC is about finding problems: It’s reactive, focusing on the products or outputs to ensure they meet standards.
Example: QA would be like creating a gym routine to stay healthy, while QC is stepping on a scale to check your progress.
Misconception 2: If You Have QA, You Don’t Need QC
It’s tempting to think that if your QA systems are rock solid, you can skip QC. But even with the best QA processes in place, errors can still happen. QC acts as your safety net to catch any issues before they reach the customer.
Think of it like flying a plane:
- QA is the team ensuring the plane is well-maintained and the pilots are trained.
- QC is the pre-flight inspection, making sure everything is in working order before takeoff.
You wouldn’t skip either step, right?
Misconception 3: QC Means You Don’t Need QA
On the flip side, some people think QC is enough on its own. “Why worry about processes when we can just fix issues later?” But this mindset can lead to costly mistakes. Without QA, you’re likely to see the same problems pop up again and again.
Example: Imagine a bakery skipping QA. They don’t create recipes or train their staff, so they end up baking inconsistent cakes. QC catches the bad ones, but they’re wasting time and ingredients on products that shouldn’t have gone wrong in the first place.
Misconception 4: QA and QC Are Only for Manufacturing
When people hear terms like “Quality Control,” they often picture factory floors and production lines. But QA and QC are for any industry.
- In software: QA ensures coding standards are followed, while QC tests for bugs.
- In healthcare: QA sets up patient care protocols, while QC ensures those protocols are followed.
- In retail: QA involves training staff and setting customer service standards, while QC checks that customers are satisfied.
Wherever quality matters (spoiler: it matters everywhere), QA and QC have a role to play.
Misconception 5: QA Is Just About Paperwork
Let’s be honest—QA often gets a bad rap as being overly bureaucratic. Sure, documentation is a big part of it, but it’s not the only part. QA is about strategy, foresight, and designing systems that work seamlessly. The paperwork just helps make sure nothing gets lost in translation.
Example: Writing Standard Operating Procedures (SOPs) isn’t about creating piles of paper. It’s about ensuring everyone knows how to do their job right, every time.
Misconception 6: QC Is Just About Finding Faults
QC sometimes gets a reputation for being the “bad guy”—the team that points out mistakes. But it’s much more than that. QC plays a critical role in continuous improvement by identifying trends and feeding that data back to QA.
Example: If QC notices a recurring defect in a product, they can share that information with the QA team, who can then tweak the process to prevent the issue in the future. It’s a team effort!
Why Busting These Myths Matter
Misunderstandings about QA and QC can lead to gaps in your quality system. By knowing the truth, you can:
- Implement both QA and QC effectively.
- Foster better communication between teams.
- Deliver consistent, reliable quality to your customers.
Quick Recap:
- QA = Proactive (process-focused), QC = Reactive (product-focused).
- QA and QC are complementary; you need both.
- They apply to every industry, not just manufacturing.
- QA is strategic, not just paperwork.
- QC isn’t just about pointing out mistakes; it drives improvement.
6. Practical Tips for Balancing Quality Assurance vs Quality Control
Now that we’ve tackled the myths, let’s get practical. Implementing both Quality Assurance (QA) and Quality Control (QC) in your business can feel overwhelming, but it doesn’t have to be. With the right balance, you can set up a system that’s efficient, effective, and tailored to your needs. Here’s how to do it.
Start with QA: Build a Strong Foundation
You can think of QA as your quality game plan. Without it, you’re just reacting to problems as they come. Here’s how to get started:
- Define Your Standards:
- Decide what “quality” means for your business. For example, in food manufacturing, it might mean following ISO 22000 standards for food safety.
- Use frameworks like ISO 9001 to guide your quality processes.
- Document Your Processes:
- Create clear, step-by-step instructions (Standard Operating Procedures or SOPs) for every key task.
- Involve your team to make sure the processes are realistic and practical.
- Train Your Team:
- A well-trained team is your biggest asset. Make sure everyone understands the processes and why they matter.
- Provide regular updates and refresher sessions to keep quality top of mind.
- Monitor and Improve:
- Use tools like internal audits and risk assessments to identify areas for improvement.
- Encourage feedback from employees—those on the ground often spot issues first.
Layer in QC: Your Final Line of Defense
Once QA is in place, it’s time to add QC as the safety net. QC ensures your final product or service meets the standards you set.
- Establish Inspection Points:
- Decide when and where QC checks will happen. For example:
- In manufacturing, inspect products after each major step.
- In service industries, review customer feedback regularly.
- Decide when and where QC checks will happen. For example:
- Use Checklists and Testing Tools:
- Develop simple checklists to guide QC inspections. These ensure consistency and prevent details from being overlooked.
- Invest in tools that help with testing, like calibrated equipment for product inspections or automated software testing tools.
- Record and Analyze Data:
- Keep detailed records of QC inspections. Look for patterns—are certain defects showing up repeatedly?
- Share this data with the QA team to improve processes.
Practical Examples by Business Size
The way you balance QA and QC will depend on your resources. Here are some tailored tips:
- Small Businesses:
- Focus on simple, effective QA processes. For instance, a bakery might have one SOP for dough preparation and another for baking.
- Perform random QC checks on batches instead of inspecting every product to save time.
- Medium-Sized Businesses:
- Introduce internal audits to check compliance with processes.
- Use QC data to identify areas where your QA system might need improvement.
- Large Enterprises:
- Implement an Integrated Management System (IMS) to combine QA and QC efforts across departments.
- Use advanced tools like predictive analytics to identify risks early.
Industry-Specific Tips
Every industry has its quirks. Here are a few examples of how QA and QC play out in different fields:
- Food Industry:
- QA: Develop a HACCP plan to prevent contamination.
- QC: Perform random sampling to test for pathogens or spoilage.
- Software Development:
- QA: Set coding standards and use version control systems.
- QC: Test for bugs using both manual and automated tools.
- Healthcare:
- QA: Train staff on patient safety protocols.
- QC: Review patient records to ensure protocols are followed.
- Construction:
- QA: Ensure designs meet safety standards and regulations.
- QC: Inspect materials and structures during and after construction.
A Continuous Cycle of Improvement
QA and QC aren’t “set it and forget it” processes. They’re part of a continuous improvement cycle:
- Plan: Define your quality goals and processes (QA).
- Do: Implement your processes and produce your product or service.
- Check: Inspect and test the results (QC).
- Act: Use feedback to refine your processes.
By constantly refining both QA and QC, you create a culture of quality that benefits your customers, employees, and bottom line.
Quick Recap:
- Start with QA to build solid processes, then layer in QC for final checks.
- Tailor your approach based on your business size and industry.
- Use QA and QC data to create a continuous improvement loop.
7. How Quality Assurance vs Quality Control Tie Into ISO Standards
If you’re serious about quality, you’ve probably heard of ISO standards. These global frameworks help businesses implement best practices for managing quality, efficiency, and compliance. Here’s how QA and QC fit into the world of ISO standards—and why they’re such a powerful combination.
The Role of ISO Standards in QA and QC
ISO standards, like ISO 9001, provide a structured approach to quality management. They’re designed to ensure businesses consistently meet customer expectations while improving processes. Here’s how they align with QA and QC:
- QA in ISO Standards: ISO emphasizes the importance of proactive measures, which is the essence of QA. For example:
- ISO 9001 focuses heavily on designing effective processes, documenting them, and training employees to follow them.
- Standards like ISO 17025 (for laboratories) or ISO 15189 (for medical labs) require strict control over testing procedures and staff competency, which fall under QA.
- QC in ISO Standards: While ISO prioritizes prevention, it doesn’t skip over detection. QC comes into play through:
- Monitoring and measuring outputs to verify compliance with standards.
- Maintaining records of inspections, tests, and results to ensure traceability.
Examples of ISO Standards That Blend QA and QC
Let’s look at some popular ISO standards and how they incorporate both QA and QC:
- ISO 9001 (Quality Management Systems):
- QA: Emphasizes risk-based thinking, process design, and employee training.
- QC: Requires monitoring and measurement of products to ensure they meet specifications.
- ISO 17025 (Testing and Calibration Labs):
- QA: Focuses on method validation, staff training, and equipment calibration.
- QC: Includes sample testing and documentation of results to ensure accuracy and reliability.
- ISO 15189 (Medical Labs):
- QA: Ensures protocols for patient safety and staff competency are in place.
- QC: Includes reviewing test results and performing quality checks on lab equipment.
- ISO 22000 (Food Safety Management):
- QA: Implements Hazard Analysis and Critical Control Points (HACCP) to prevent contamination.
- QC: Conducts product sampling and microbial testing to detect potential risks.
Why ISO Standards Matter for QA and QC
- Credibility and Trust: Following ISO standards shows customers and stakeholders that you’re serious about quality. It’s like having a globally recognized seal of approval.
- Consistency Across the Board: ISO standards help you align QA and QC efforts, ensuring everyone in your organization is on the same page.
- Continuous Improvement: ISO standards emphasize regular audits and reviews. This encourages a culture of ongoing refinement for both processes (QA) and outputs (QC).
- Compliance and Risk Management: For industries like healthcare, food, and aviation, ISO standards ensure you meet regulatory requirements and reduce risks.
Implementing QA and QC with ISO Standards
Here’s how you can start integrating ISO standards into your QA and QC practices:
- Understand the Standard:
- Read through the requirements of the ISO standard relevant to your industry. Break it down into actionable steps for QA and QC.
- Map QA and QC Processes:
- QA: Focus on the areas where ISO requires processes, documentation, and risk management.
- QC: Identify where the standard specifies inspections, testing, or monitoring.
- Train Your Team:
- Make sure your staff understands the standard and their role in meeting its requirements.
- Monitor, Audit, and Improve:
- Conduct internal audits to check compliance with ISO.
- Use QC results to identify gaps in your QA system and refine your processes.
How ISO Standards Help QA and QC Teams Collaborate
One of the best things about ISO standards is how they encourage collaboration between QA and QC teams. Here’s how:
- Shared Goals: Both teams work toward compliance and customer satisfaction.
- Clear Communication: ISO requires thorough documentation, which ensures everyone has access to the same information.
- Data Sharing: QC findings feed into QA improvements, creating a feedback loop.
Quick Recap:
- ISO standards like ISO 9001, 17025, and 15189 seamlessly integrate QA and QC.
- QA focuses on building processes; QC ensures outputs meet standards.
- ISO helps you build credibility, consistency, and a culture of continuous improvement.
- Start by understanding the standard, mapping your processes, and training your team.
8. Common Challenges and How to Overcome Them
Even with a clear understanding of Quality Assurance (QA) and Quality Control (QC), implementing both can be tricky. Like any system, challenges can crop up, whether it’s misalignment between teams, resistance to change, or unexpected obstacles. But don’t worry—these challenges are manageable with the right strategies. Let’s break them down.
Challenge 1: Misalignment Between QA and QC Teams
Sometimes, QA and QC teams don’t see eye to eye. QA might feel that QC focuses too much on finding faults, while QC might think QA is overly theoretical. This disconnect can lead to inefficiencies, miscommunication, and gaps in quality.
How to Fix It:
- Encourage Collaboration:
- Host regular meetings between QA and QC teams to discuss goals and share insights.
- Use data from QC (like recurring defects) to improve QA processes.
- Clarify Roles:
- Clearly define the responsibilities of each team. For instance:
- QA designs the process.
- QC ensures the output meets the standards set by QA.
- Clearly define the responsibilities of each team. For instance:
- Create a Feedback Loop:
- Establish a system where QC findings are routinely shared with QA for process improvement.
Challenge 2: Over-Reliance on QC
Some businesses rely heavily on QC to catch defects rather than investing in strong QA systems to prevent them. While QC is important, it’s more expensive to fix defects than to avoid them in the first place.
How to Fix It:
- Invest in QA:
- Focus on creating robust processes, clear documentation, and thorough employee training.
- Shift the Mindset:
- Emphasize that QA saves time and money by reducing the number of defects QC has to catch.
- Measure the Cost of Defects:
- Use data to show how much fixing defects costs compared to preventing them. This can help build buy-in for stronger QA practices.
Challenge 3: Resistance to Change
Implementing or improving QA and QC systems often requires changes in how people work. Employees may resist these changes, seeing them as extra work or unnecessary bureaucracy.
How to Fix It:
- Involve the Team:
- Get employees involved in designing QA and QC processes. When people feel ownership, they’re more likely to support the changes.
- Explain the Benefits:
- Show how QA and QC improve not only product quality but also job satisfaction (fewer mistakes mean less stress).
- Provide Training:
- Offer hands-on training to make new systems easy to understand and follow.
Challenge 4: Lack of Resources
Small businesses or startups may feel they lack the time, money, or expertise to implement both QA and QC effectively.
How to Fix It:
- Start Small:
- Focus on one or two critical processes or products to develop your QA and QC systems.
- Use simple tools like checklists and spreadsheets before investing in advanced software.
- Leverage Standards:
- Use frameworks like ISO 9001 to guide your efforts. These provide a ready-made roadmap for quality management.
- Outsource Expertise:
- If hiring a full-time QA or QC expert isn’t feasible, consider hiring consultants for setup and training.
Challenge 5: Inconsistent Processes
When QA processes are inconsistent or poorly documented, it becomes harder for QC to do its job effectively. This often leads to confusion and a lack of accountability.
How to Fix It:
- Standardize Procedures:
- Develop SOPs for every major process and make them accessible to all team members.
- Audit Regularly:
- Conduct periodic audits to ensure everyone is following the processes consistently.
- Update as Needed:
- Review and revise procedures regularly to keep them relevant and effective.
Challenge 6: Difficulty in Scaling
As businesses grow, their QA and QC systems need to grow with them. What worked for a small team might not work for a larger organization.
How to Fix It:
- Implement Scalable Systems:
- Use cloud-based tools to manage documentation, track QC inspections, and share data across teams.
- Hire Strategically:
- Bring in dedicated QA and QC specialists as your team expands.
- Adopt Advanced Tools:
- Consider automating parts of your QA and QC processes, like real-time data monitoring or automated testing.
Embracing Challenges as Opportunities
Challenges in QA and QC aren’t just obstacles—they’re opportunities to refine your systems and improve your business. Each challenge, when addressed thoughtfully, brings you closer to creating a culture of quality that benefits everyone: your team, your customers, and your bottom line.
Quick Recap:
- Misalignment, over-reliance on QC, and resistance to change are common challenges.
- Solutions include fostering collaboration, investing in QA, and providing training.
- Start small, use ISO standards as a guide, and scale strategically as your business grows.
9. The Future of Quality Assurance vs Quality Control
Quality Assurance (QA) and Quality Control (QC) aren’t static concepts. As industries evolve, so do the ways we approach quality. Emerging technologies, global trends, and shifting customer expectations are reshaping QA and QC, making them more efficient, data-driven, and aligned with modern demands. Let’s take a look at where the future is headed.
1. Automation: The Rise of Smart QA and QC
Automation is revolutionizing both QA and QC by reducing human error and speeding up processes. Here’s how it’s changing the game:
- In QA:
- AI and Machine Learning: Predictive analytics can identify potential process weaknesses before they cause issues. For example, AI can analyze data trends to suggest process improvements.
- Automated Documentation: Tools like workflow software can create and update SOPs automatically, saving time and ensuring consistency.
- In QC:
- Automated Testing: In industries like manufacturing, robots can inspect products for defects at speeds humans can’t match.
- Real-Time Monitoring: Sensors on production lines can detect issues immediately, allowing for instant corrections.
Example: In pharmaceutical production, automated systems now test the chemical composition of medicines during production, combining QA and QC in real time.
2. Data-Driven Quality: Big Data Meets QA and QC
Data is the new gold, and QA/QC teams are mining it for insights. Big data allows businesses to make smarter, faster decisions about quality.
- For QA:
- Data analytics helps identify trends, risks, and areas for improvement in processes.
- Example: Analyzing customer complaints to find patterns and improve manufacturing methods.
- For QC:
- Statistical tools like Six Sigma can pinpoint problem areas in production.
- Example: Tracking defect rates over time to identify and eliminate recurring issues.
3. Remote QA and QC
The rise of remote work has impacted quality processes, too. Businesses are finding ways to ensure quality without being physically present.
- For QA:
- Virtual audits and online training platforms are becoming the norm. Tools like Zoom and digital checklists allow teams to collaborate on quality processes from anywhere.
- Example: Remote auditing of a supplier’s facility using video and live documentation sharing.
- For QC:
- Remote inspections use cameras, drones, or sensors to check products or facilities.
- Example: Using drones to inspect large infrastructure projects like bridges or pipelines.
4. Sustainability: QA and QC for a Greener Future
Customers and governments are increasingly demanding sustainable practices. QA and QC are stepping up to the challenge.
- In QA:
- Focus on creating processes that minimize waste and energy use.
- Example: Developing lean manufacturing systems to reduce resource consumption.
- In QC:
- Ensuring that end products meet eco-friendly certifications, like recyclable packaging or energy-efficient performance.
- Example: Testing electronic devices to ensure they meet energy-saving standards.
5. Globalization and Cross-Border Standards
With businesses operating across borders, QA and QC need to navigate different regulatory requirements and cultural expectations.
- Unified Standards: Organizations like ISO are working on global frameworks to make quality management easier for international businesses.
- Cultural Sensitivity: QA and QC teams are adapting their processes to meet local market preferences.
Example: A global food company ensures compliance with both FDA standards in the U.S. and EU food safety regulations.
6. AI-Driven Personalization in Quality
As personalization becomes a key market trend, QA and QC processes are being tailored to meet individual customer needs.
- For QA:
- Processes are designed to accommodate customization, like on-demand manufacturing.
- For QC:
- Products are tested for personalized features, such as custom sizing or unique configurations.
Example: In the automotive industry, QA ensures assembly lines can handle custom orders, while QC inspects the final cars to confirm they match customer specifications.
7. The Integration of QA and QC
In the future, the lines between QA and QC will blur as technologies like AI and real-time monitoring allow for continuous feedback loops.
- Seamless Systems: Processes will be designed to incorporate both QA and QC in a single, unified workflow.
- Example: A software platform that automatically flags defects during production and updates the QA process to prevent them in the future.
What This Means for You
As the future of QA and QC unfolds, businesses that embrace these changes will stay ahead of the curve. Here’s how you can prepare:
- Invest in Technology: Start exploring tools that support automation, data analytics, and remote capabilities.
- Focus on Sustainability: Evaluate your processes to see where you can reduce waste and energy use.
- Adapt to Global Standards: Stay up to date with ISO developments and other international quality frameworks.
Quick Recap:
- Automation and AI are transforming QA and QC.
- Big data allows smarter decision-making for quality management.
- Sustainability and globalization are driving changes in processes and standards.
- The future will see more integrated, seamless QA and QC systems.
10. Conclusion: Bringing It All Together
By now, you should have a crystal-clear picture of how Quality Assurance (QA) and Quality Control (QC) work, how they differ, and why they’re both essential. These two pillars of quality management aren’t just buzzwords—they’re practical tools that can transform your business processes, improve customer satisfaction, and boost your bottom line.
Why QA and QC Matter Together
To recap:
- QA is the architect of quality, designing processes that prevent problems before they occur. It’s proactive, strategic, and focuses on the how.
- QC is the detective of quality, inspecting and testing outputs to catch any defects. It’s reactive, detailed, and focuses on the what.
Together, QA and QC form a robust quality system. QA sets the foundation, and QC ensures that foundation delivers reliable results.
How QA and QC Impact Your Business
- Reduce Costs: By preventing and detecting defects, you avoid costly rework, recalls, and dissatisfied customers.
- Improve Efficiency: Strong QA processes streamline operations, while QC ensures consistent results.
- Build Trust: When customers know they can count on you for quality, they stick around and recommend you to others.
Taking the Next Step
So, where do you go from here? Whether you’re running a small business, working in a global corporation, or just starting to think about quality management, here are some actionable steps:
- Assess Your Current Processes:
- Are your QA systems strong enough to prevent issues?
- Is your QC catching defects effectively?
- Start Small, Think Big:
- If you’re new to QA and QC, focus on a single product or process. Nail it, then expand.
- Leverage Standards Like ISO:
- Frameworks like ISO 9001 give you a clear roadmap for managing quality in a structured way.
- Invest in Continuous Improvement:
- QA and QC are never “done.” Use feedback, data, and lessons learned to refine your approach over time.
Think of QA and QC as your quality dream team. They’re not in competition—they’re partners, working together to help you deliver the best products and services possible. Whether it’s a perfect cup of coffee, a cutting-edge app, or a life-saving medication, QA and QC ensure you can deliver with confidence, every time.
Your Turn! What’s your experience with QA and QC? Have you faced challenges implementing them, or do you have success stories to share? Let’s continue the conversation—quality is a journey we’re all on together!
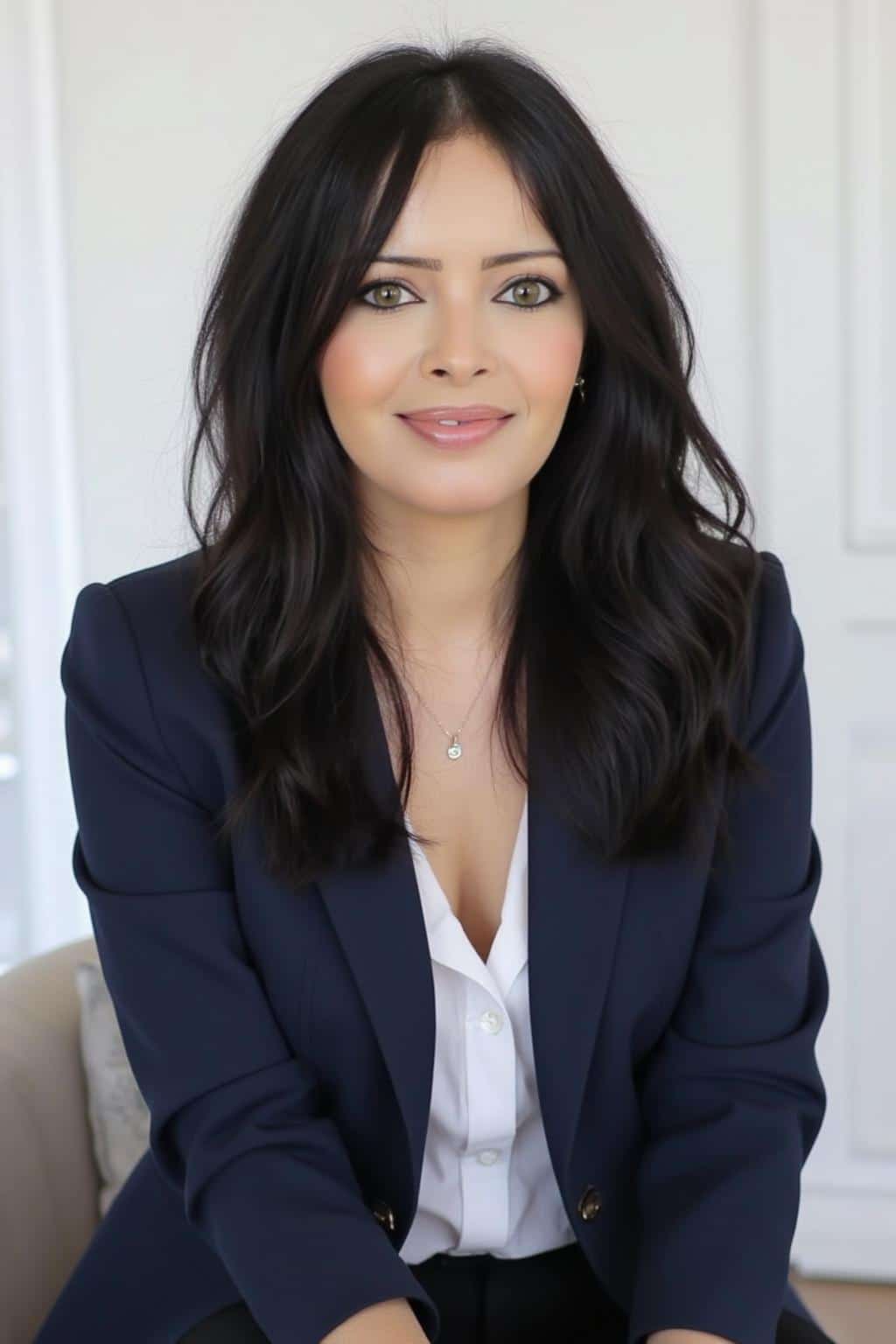
👋 Hi, I’m HAFSA, and for the past 12 years, I’ve been on a journey to
make ISO standards less intimidating and more approachable for everyone.
Whether it’s ISO 9001, ISO 22000, or the cosmetics-focused ISO 22716,
I’ve spent my career turning complex jargon into clear, actionable steps
that businesses can actually use. I’m not here to call myself an expert—I prefer “enthusiast” because I truly love what I do.
There’s something incredibly rewarding about helping people navigate food safety and quality management systems
in a way that feels simple, practical, and even enjoyable.
When I’m not writing about standards, you’ll probably find me playing Piano 🎹, connecting with people, or diving into my next big project💫.
I’m an engineer specialized in the food and agricultural industry
I have a Master’s in QHSE management and over 12 years of experience as a Quality Manager
I’ve helped more than 15 companies implement ISO 9001, ISO 22000, ISO 22716, GMP, and other standards
My clients include food producers, cosmetics manufacturers, laboratories, and service companies
I believe quality systems should be simple, useful, and efficient
Outside of work, I play piano and love learning something new every day
Let’s make ISO less about stress and more about success! 🙏
Related Posts
Popular tags
Recent Posts
Recent Comments
- Engr. Shamsuddeen Dalhatu on ISO 9001 Requirements Checklist: A Comprehensive Guide
- Lakshman Balajepalli on How to get GMP certification?
- Hani alghamdi on What is the difference between AS9100 and ISO 9001?
- keberku on Simple method to ensure confidentiality in laboratories for ISO/IEC 17025
- Abdullatif Al Najim on Procedure for Externally Provided Products and Services in ISO 17025
Subscribe on YouTube
Product tags
Popular Courses