ISO 9001 2015 Documentation Requirements
ISO 9001 2015 Documentation Requirements
Have you ever started a project and thought, “Where do I even begin?” That’s how many businesses feel when they first encounter ISO 9001:2015 certification. One of the first steps—and arguably the most important—is creating the right documentation. But don’t worry, you’re not alone! Understanding ISO 9001 Documentation is simpler than it sounds, and I’m here to break it down for you.
ISO 9001 documentation forms the backbone of your quality management system (QMS). It’s what ensures that everyone in your organization knows what to do, how to do it, and why it matters. It’s not just about checking boxes for certification—it’s about building a system that helps your business run smoother, more efficiently, and with fewer headaches.
In this article, we’ll explore why ISO 9001 Documentation is so essential, what the requirements are, and how you can create effective, easy-to-use documents for your business. So, grab a coffee, and let’s dive into the world of ISO 9001 together!
Why ISO 9001 Documentation is Important
If you’re wondering why ISO 9001 Documentation gets so much attention, think of it as the blueprint for your business’s success. Imagine trying to build a house without a plan—you might end up with something that looks okay on the outside but crumbles when you need it most. That’s where documentation steps in: it provides structure, clarity, and consistency to everything you do.
The Role of Documentation in a QMS
At its core, ISO 9001 Documentation is all about creating a quality management system (QMS) that works for your business. It ensures that processes are followed consistently, which helps maintain the quality of your products or services. Without proper documentation, you might find yourself constantly reinventing the wheel or dealing with preventable mistakes.
Why It Matters:
- Consistency: When processes are clearly documented, everyone knows exactly what to do.
- Accountability: Documentation shows who’s responsible for what, so there’s no confusion.
- Compliance: Proper records demonstrate to auditors that you meet ISO 9001 requirements.
For example, let’s say you run a catering business. Without documented procedures, one chef might use a different recipe than another, leading to inconsistent results. With ISO 9001 Documentation, every meal meets the same high standards, delighting your customers every time.
Documentation as a Communication Tool
Another reason ISO 9001 Documentation is so important is that it serves as a bridge between different teams and departments. Clear, well-organized documents ensure that everyone is on the same page, reducing miscommunication and errors.
Think of it this way:
If your team has access to a clear manual or checklist, they won’t need to waste time asking questions or guessing what’s expected of them. This not only boosts efficiency but also creates a more collaborative work environment.
Example:
In a small manufacturing company, a documented workflow might outline exactly how raw materials are handled, processed, and packaged. This ensures that the production team, quality control team, and shipping team are all aligned, preventing delays or defects.
The Bottom Line
Good documentation isn’t just a requirement for certification—it’s a tool for building a stronger, more efficient business. Whether you’re creating policies, work instructions, or records, every piece of ISO 9001 Documentation plays a role in making your operations more reliable and your team more effective.
In the next section, we’ll dive into the specific documentation requirements of ISO 9001:2015, so you’ll know exactly what’s needed to get started. Let’s keep going!
Overview of ISO 9001:2015 Documentation Requirements
Now that we know why documentation is so important, let’s dive into what ISO 9001 Documentation actually requires. One of the things people love about ISO 9001:2015 is that it’s more flexible than earlier versions. While it still emphasizes the need for clear and effective documentation, it’s less prescriptive, giving you the freedom to create a system that works for your business.
Here’s a breakdown of the key documentation requirements and what they mean for your organization.
Mandatory Documents You Must Have
The first thing to know about ISO 9001 Documentation is that there are a few must-haves—documents that every certified organization needs. These include:
- Scope of the QMS
- This outlines what your quality management system covers, including the products, services, and locations it applies to. Think of it as the “big picture” document.
- Quality Policy
- This is your commitment to quality, written in a way that’s easy for your team to understand. It sets the tone for your entire QMS.
- Quality Objectives
- These are specific, measurable goals that align with your quality policy. For example, “reduce customer complaints by 15% over the next year.”
- Process Documentation
- For critical processes, like production, sales, or customer support, you’ll need to document how things are done.
- Records of Compliance
- Evidence that you’re meeting the standard’s requirements, such as internal audit results, corrective action plans, and performance evaluations.
Records vs. Documents: What’s the Difference?
Here’s where it can get a little confusing: ISO 9001 Documentation includes both documents and records, and they’re not quite the same thing.
- Documents explain how things should be done. For example, a work instruction that outlines how to operate a machine.
- Records show what has been done. For example, a maintenance log for that same machine.
Think of it this way: documents are the plan, and records are the proof.
Flexibility in Documentation
ISO 9001:2015 gives you the flexibility to decide how much documentation your business needs. While the standard requires certain documents and records, it’s up to you to determine what additional documentation will help your operations run smoothly.
For example:
- A small, family-run bakery might only need a few simple checklists to cover their processes.
- A large, international manufacturing company might require detailed flowcharts, manuals, and digital tracking systems.
The key is to create ISO 9001 Documentation that’s practical and easy to use, rather than overwhelming your team with unnecessary details.
What’s Next?
With these requirements in mind, you’re well on your way to understanding the foundation of ISO 9001:2015 documentation. In the next section, we’ll explore the specific sections of ISO 9001 Documentation in more detail, so you can start building a system that works for your business. Let’s keep going!
Key Sections of ISO 9001 Documentation
Now that we’ve covered the basics of ISO 9001 Documentation, let’s dig deeper into the key sections. These areas form the foundation of your quality management system (QMS) and ensure that every aspect of your business is aligned with ISO 9001:2015 requirements. Don’t worry—I’ll break it down step by step so it feels manageable.
1. Context of the Organization
This section is all about understanding the environment your business operates in. Think of it as setting the stage for your QMS.
What to Document:
- Internal and External Issues: What factors impact your ability to meet customer needs? For example, market trends, competition, or resource availability.
- Interested Parties: Who are the stakeholders in your business? These could be customers, employees, suppliers, or regulators.
- Scope of the QMS: Clearly define what your QMS covers and where it applies.
Why It Matters:
Documenting the context of your organization helps you stay focused on the big picture while ensuring your processes align with your goals. For example, a logistics company might document how supply chain disruptions impact delivery times and plan accordingly.
2. Leadership Commitment
ISO 9001 places a strong emphasis on leadership. This section of your ISO 9001 Documentation should demonstrate that your leadership team is actively involved in supporting and maintaining the QMS.
What to Document:
- Roles and Responsibilities: Clearly outline who is responsible for what within the QMS.
- Communication: Show how leaders communicate the importance of quality to the entire organization.
- Quality Policy: This should reflect the company’s commitment to meeting customer and regulatory requirements.
Why It Matters:
When leadership is involved, the entire team is more likely to take the QMS seriously. For example, if a retail business documents how managers will regularly review quality goals with staff, it sets the tone for accountability and improvement.
3. Risk Management and Opportunities
One of the standout features of ISO 9001:2015 is its focus on risk-based thinking. Your ISO 9001 Documentation should show how your organization identifies, assesses, and addresses risks and opportunities.
What to Document:
- Risks: What could go wrong, and how will you prevent it?
- Opportunities: What could go right, and how will you take advantage of it?
- Action Plans: Document how risks and opportunities are monitored and managed.
Why It Matters:
By addressing risks and opportunities, you’re not just reacting to problems—you’re staying ahead of them. For instance, a software company might document potential risks like system downtime and outline backup strategies to minimize impact.
4. Operational Processes
This is where the magic happens—your day-to-day activities. This section of your ISO 9001 Documentation should detail how your products or services are created and delivered.
What to Document:
- Work Instructions: Step-by-step guides for specific tasks, like operating machinery or handling customer complaints.
- Process Flowcharts: Visual representations of workflows, from start to finish.
- Monitoring and Measurement: How will you track the effectiveness of these processes?
Why It Matters:
Clear documentation ensures consistency and quality. For example, a small café might document their coffee preparation process to ensure every cup tastes just right.
5. Performance Evaluation
ISO 9001 isn’t just about setting up processes—it’s about improving them. Your documentation should show how you measure performance and identify areas for improvement.
What to Document:
- Key Performance Indicators (KPIs): Metrics that help you track progress, like customer satisfaction scores or production efficiency.
- Audit Reports: Results from internal or external audits.
- Corrective Actions: Steps taken to address any non-conformities.
Why It Matters:
When you measure and evaluate performance, you create a culture of continuous improvement. For example, a transportation company might document on-time delivery rates and use the data to optimize routes.
Bringing It All Together
These sections form the backbone of your ISO 9001 Documentation. By breaking it down into manageable pieces, you can ensure that every aspect of your QMS is well-documented and aligned with ISO 9001:2015 requirements.
In the next section, we’ll talk about how to create effective documentation that’s not only compliant but also easy to use and maintain. Let’s keep building!
How to Create Effective ISO 9001 Documentation
Now that we’ve covered the key sections, let’s talk about how to create ISO 9001 Documentation that’s not only compliant but also practical and easy to use. After all, the goal isn’t just to impress auditors—it’s to create a system that genuinely helps your business run better. The good news? You don’t need to overcomplicate things. With a few simple strategies, you can develop documentation that works for everyone on your team.
1. Keep It Simple and Relevant
One of the biggest mistakes businesses make is creating overly detailed or complex documentation. While it’s important to meet ISO 9001 requirements, your documents should be easy to understand and use in real life.
Tips:
- Focus on clarity—use straightforward language and avoid jargon.
- Include only the information that’s truly necessary for the process.
- Use bullet points, charts, or visuals to make documents more user-friendly.
Example:
Instead of writing a five-page manual on how to handle customer complaints, create a one-page checklist that covers the key steps. This makes it easier for your team to follow and apply consistently.
2. Use Templates and Tools
Why start from scratch when there are plenty of resources available to help you? Using templates and tools can save time and ensure your ISO 9001 Documentation is organized and professional.
Where to Find Them:
- Many certification bodies and ISO consultants offer free or low-cost templates for quality policies, work instructions, and process maps.
- Quality management software can help you create, store, and track documentation more efficiently.
Example:
A small IT company might use a template to document its incident management process, ensuring it covers all the necessary elements without spending weeks creating it from the ground up.
3. Involve Your Team
Your team is on the front lines of your operations, so they’re the best resource for creating practical and effective ISO 9001 Documentation. Involving employees ensures that your documents reflect real-world processes and are easier to follow.
How to Collaborate:
- Hold workshops or brainstorming sessions to map out processes with your team.
- Ask for feedback on draft documents—your employees might spot gaps or suggest improvements.
- Assign team members as “owners” of specific documents to ensure they stay up to date.
Example:
A manufacturing company could ask production line workers to review a draft of their operating procedures, ensuring the steps make sense and are feasible in practice.
4. Focus on Accessibility
Your ISO 9001 Documentation won’t do much good if your team can’t find it when they need it. Make sure all your documents are well-organized, easy to access, and stored in a central location.
Best Practices:
- Use a digital system to store and manage documentation, such as cloud-based software.
- Create a clear naming convention for files to make them easy to search.
- Train employees on where to find the documents they need.
Example:
A retail chain could use an online portal to store its procedures, so employees at any location can quickly access the information they need, from handling returns to updating inventory.
5. Review and Update Regularly
Creating your ISO 9001 Documentation isn’t a one-and-done task. Processes evolve, and your documents need to keep up. Regular reviews ensure your documentation stays relevant and effective.
How to Stay Current:
- Set a schedule for reviewing key documents, such as annually or after major changes.
- Use version control to keep track of updates and ensure everyone is working with the latest version.
- Encourage employees to report when a document no longer reflects the current process.
Example:
A healthcare provider might update their patient intake procedures after introducing new technology, ensuring the documentation aligns with the updated workflow.
Make It Work for Your Business
Effective ISO 9001 Documentation is all about balance—meeting the standard’s requirements while keeping things simple, relevant, and useful. By following these tips, you’ll create a system that not only helps you achieve certification but also adds real value to your organization.
In the next section, we’ll cover common mistakes to avoid when working on ISO 9001 documentation. Trust me, knowing what NOT to do is just as important as knowing what to do. Let’s keep the momentum going!
Common Mistakes to Avoid in ISO 9001 Documentation
Creating ISO 9001 Documentation can feel like a big task, but here’s the good news: it doesn’t have to be perfect the first time. That said, there are some common pitfalls you’ll want to steer clear of to save yourself time, frustration, and headaches down the road. Let’s go over these mistakes so you can avoid them and create documentation that truly works for your business.
1. Overloading Documents with Unnecessary Details
Have you ever opened a document and felt completely overwhelmed by endless paragraphs of information? That’s exactly what you want to avoid with ISO 9001 Documentation. Including too much detail can make documents harder to use and less effective.
Why It’s a Problem:
- Employees might skip over critical information because they’re drowning in unnecessary details.
- It becomes harder to update documents when every little thing is written down.
What to Do Instead:
- Focus on what’s essential—only include information that’s relevant and actionable.
- Use clear headings, bullet points, and visuals to make documents easy to scan.
Example:
Instead of a five-page procedure for opening a store, a retail business might create a one-page checklist that covers the key steps, like turning on the lights, stocking registers, and unlocking doors.
2. Neglecting Regular Updates
One of the biggest mistakes businesses make is treating ISO 9001 Documentation as a “set it and forget it” task. Processes change, teams evolve, and your documents need to keep up.
Why It’s a Problem:
- Outdated documents lead to confusion and mistakes.
- Auditors might flag discrepancies if your documentation doesn’t reflect current practices.
What to Do Instead:
- Schedule regular reviews—quarterly or annually works well for most businesses.
- Assign a document owner for each section to ensure updates are made when needed.
Example:
A small tech company might update its onboarding process documentation after introducing new software, ensuring that new hires have accurate instructions to follow.
3. Ignoring Employee Input
Your employees are the ones using the ISO 9001 Documentation, so it only makes sense to involve them in the process. Failing to get their input can lead to documents that look good on paper but don’t work in practice.
Why It’s a Problem:
- Processes might not match what’s actually happening on the ground.
- Employees might resist using the documentation if they don’t feel it reflects their reality.
What to Do Instead:
- Involve employees in drafting and reviewing documents.
- Ask for feedback on how documents can be improved.
Example:
A manufacturing company might sit down with production line workers to ensure the steps outlined in their operating procedures are realistic and easy to follow.
4. Making Documentation Too Rigid
Flexibility is key when it comes to ISO 9001 Documentation. If your documents are too rigid, your team might struggle to adapt to unexpected situations.
Why It’s a Problem:
- Overly strict procedures can limit creativity and problem-solving.
- Employees might avoid using the documentation if it feels too restrictive.
What to Do Instead:
- Focus on outcomes rather than micromanaging every step.
- Allow room for discretion when it makes sense.
Example:
A customer service team might document general guidelines for handling complaints but allow employees the freedom to adapt based on the situation.
5. Forgetting About Accessibility
Even the best documentation won’t help if your team can’t find it when they need it. Making documents accessible and easy to locate is just as important as the content itself.
Why It’s a Problem:
- Employees waste time searching for information.
- Critical tasks might be delayed due to inaccessible documents.
What to Do Instead:
- Store documents in a centralized location, like a cloud-based platform.
- Use a clear naming system and organize files by category or department.
Example:
A healthcare provider might use an online portal to store policies and procedures, ensuring that all staff can access them quickly, even during emergencies.
Avoiding These Mistakes Sets You Up for Success
By steering clear of these common pitfalls, you’ll create ISO 9001 Documentation that’s not only compliant but also practical and user-friendly. Remember, the goal isn’t to create perfect documents—it’s to create documents that help your business operate more smoothly and efficiently.
In the next section, we’ll talk about the benefits of well-structured ISO 9001 documentation and how it can positively impact your business. Let’s keep moving forward!
Benefits of Well-Structured ISO 9001 Documentation
If you’re still wondering why ISO 9001 Documentation is such a big deal, let’s talk about the benefits. Creating clear, organized, and user-friendly documentation doesn’t just help you check a box for certification—it brings real, tangible improvements to your business. Let’s dive into the ways well-structured ISO 9001 documentation can make a difference.
1. Improved Efficiency and Consistency
Imagine running a team where everyone knows exactly what to do, how to do it, and why it matters. That’s the magic of well-organized ISO 9001 Documentation. By standardizing processes, you reduce confusion, avoid mistakes, and make your operations run more smoothly.
How It Helps:
- Employees can follow documented procedures to complete tasks consistently, even if they’re new to the team.
- Repetitive errors are minimized because everyone is on the same page.
Example:
A logistics company might use detailed documentation to standardize their packing and shipping procedures, reducing errors and speeding up delivery times.
2. Audit Readiness
If the thought of an audit makes you nervous, don’t worry—having solid ISO 9001 Documentation will help you sail through it. Auditors look for evidence that your quality management system (QMS) is working as intended, and your documentation provides that proof.
How It Helps:
- Well-structured documents make it easy to show compliance with ISO 9001 requirements.
- You’ll spend less time scrambling to gather evidence when everything is already in place.
Example:
A small manufacturing firm can quickly provide auditors with maintenance logs, training records, and quality policies, demonstrating their commitment to the standard without stress.
3. Enhanced Customer Satisfaction
One of the ultimate goals of ISO 9001 is improving customer satisfaction, and your documentation plays a key role in making that happen. By ensuring consistency in how you deliver products or services, you’re more likely to meet or exceed customer expectations.
How It Helps:
- Customers receive the same high-quality experience every time.
- Faster resolution of customer complaints thanks to documented procedures.
Example:
A retail chain with a documented customer service process can handle returns and complaints quickly and professionally, leaving customers with a positive impression.
4. Supports Training and Onboarding
Ever had a new hire struggle because they didn’t know where to start? With great ISO 9001 Documentation, training becomes a breeze. Clear, step-by-step instructions help employees get up to speed faster and reduce the learning curve.
How It Helps:
- Employees can refer to documentation for guidance instead of relying on memory or guesswork.
- Training becomes consistent, ensuring everyone learns the same best practices.
Example:
A tech startup might use a documented onboarding checklist to ensure every new hire is trained on company policies, tools, and processes in a consistent and thorough way.
5. Drives Continuous Improvement
ISO 9001 isn’t just about maintaining the status quo—it’s about getting better over time. Your ISO 9001 Documentation provides a framework for tracking performance, identifying gaps, and making improvements.
How It Helps:
- Regularly updated documentation keeps your business aligned with its goals.
- Encourages a culture of accountability and innovation.
Example:
A healthcare provider might use documented performance metrics to identify areas where patient care can be improved, such as reducing wait times or streamlining appointment scheduling.
6. Builds Trust and Credibility
When your documentation is well-organized and your processes are consistent, it sends a strong message to your customers, partners, and stakeholders: you take quality seriously. ISO 9001 certification, backed by excellent documentation, boosts your credibility.
How It Helps:
- Attracts new customers who value quality assurance.
- Strengthens relationships with existing clients and partners.
Example:
A supplier with ISO 9001 certification and well-documented processes might secure more contracts because buyers know they can rely on consistent quality.
Why It’s Worth the Effort
Creating and maintaining great ISO 9001 Documentation might take some effort upfront, but the long-term benefits are undeniable. From smoother operations and happier customers to stress-free audits and continuous growth, strong documentation is a game-changer for any business.
In the next section, we’ll wrap things up and show you how to get started with your ISO 9001 documentation journey. Let’s bring it all together!
Conclusion: Start Your ISO 9001 Documentation Journey Today
We’ve covered a lot of ground, and by now, you probably see just how important ISO 9001 Documentation is—not just for certification but for transforming the way your business operates. From improving efficiency and consistency to enhancing customer satisfaction and building trust, good documentation lays the foundation for success.
What’s the Next Step?
The first step is simple: start small. Don’t worry about creating a perfect system overnight. Focus on one process at a time, involve your team, and use templates or tools to guide you. Whether it’s documenting your quality policy, outlining procedures, or keeping track of performance metrics, every step you take brings you closer to a fully functioning quality management system.
Why It’s Worth the Effort
Yes, creating ISO 9001 Documentation takes time and effort, but the rewards are worth it. You’re not just meeting a standard—you’re building a system that helps your business run smoothly, adapt to changes, and grow. Whether you’re a small startup or a large organization, strong documentation will set you apart and help you achieve your goals.
Your Documentation Can Be a Game-Changer
Think of ISO 9001 Documentation as your business’s instruction manual. It keeps everyone on the same page, ensures that quality is maintained, and gives you the confidence to tackle audits, satisfy customers, and continuously improve.
So, are you ready to get started? Start with the basics, keep it simple, and involve your team every step of the way. Before you know it, you’ll have a robust set of documents that not only meet ISO 9001 requirements but also make your business stronger and more efficient.
If you need help along the way, don’t hesitate to reach out for resources, training, or guidance. The journey might seem daunting at first, but with the right approach, you’ll make it—and the results will speak for themselves! Let’s make your ISO 9001 Documentation journey a success!
Looking for More Resources on ISO 9001?
Looking for ISO 9001 Resources Tailored to Your Industry?
If this article helped clarify ISO 9001, take the next step with our industry-focused tools designed to simplify your certification journey:
📦 ISO 9001 Documentation Kits by Industry: Whether you’re in manufacturing, construction, consulting, or healthcare — we have complete, ready-to-use documentation tailored for your sector.
🎓 Online ISO 9001 Training: Learn how to implement ISO 9001 effectively with our easy-to-follow video lessons, real-world examples, and practical exercises.
📋 ISO 9001 Checklist: Download our step-by-step checklist to ensure your QMS meets all the 9001:2015 requirements from start to finish.
These resources are crafted to save you time, reduce stress, and help you achieve certification with confidence. Choose your industry and start now!
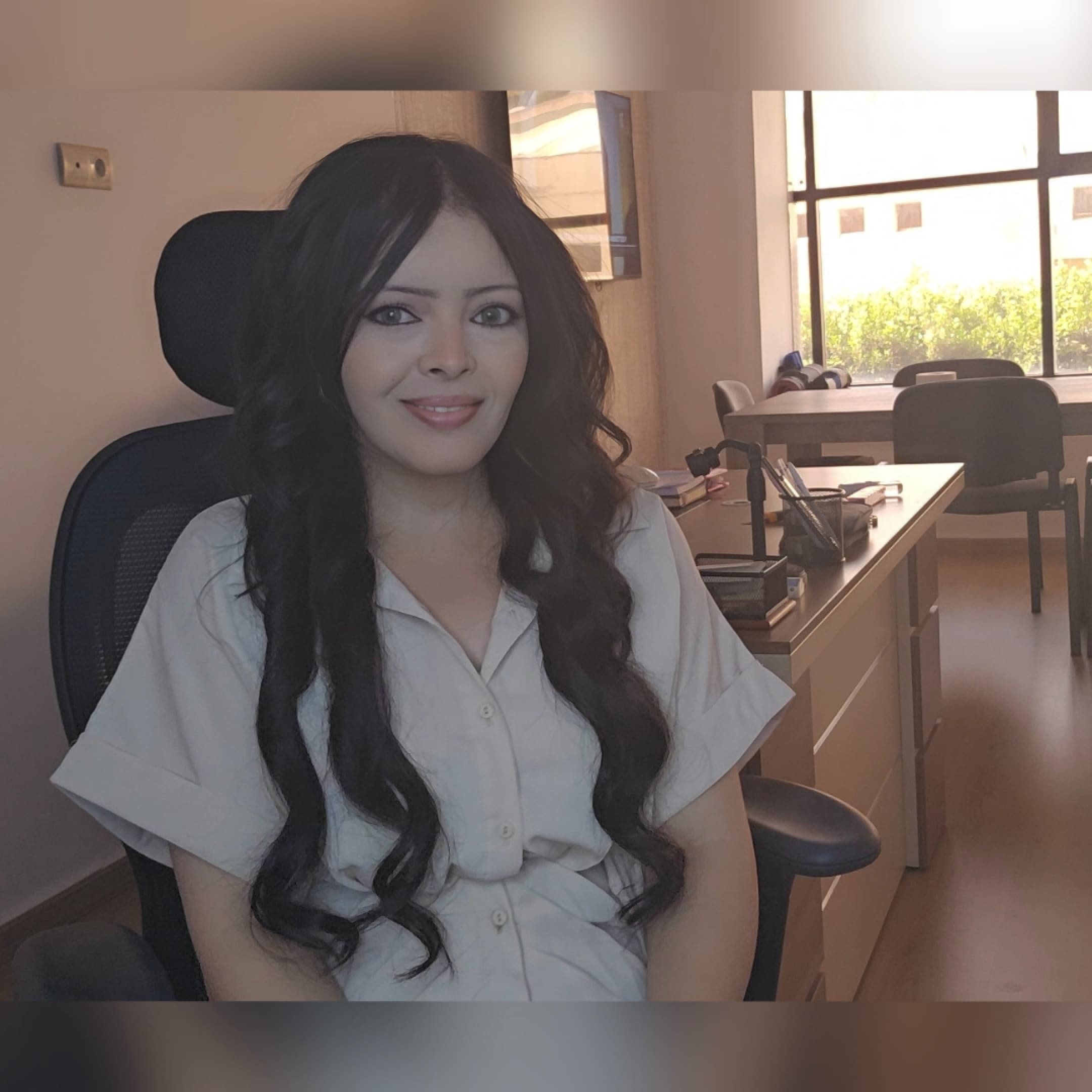
make ISO standards less intimidating and more approachable for everyone.
Whether it’s ISO 9001, ISO 22000, or the cosmetics-focused ISO 22716,
I’ve spent my career turning complex jargon into clear, actionable steps
that businesses can actually use. I’m not here to call myself an expert—I prefer “enthusiast” because I truly love what I do.
There’s something incredibly rewarding about helping people navigate food safety and quality management systems
in a way that feels simple, practical, and even enjoyable.
When I’m not writing about standards, you’ll probably find me playing Piano 🎹, connecting with people, or diving into my next big project💫.
- I’m an engineer specialized in the food and agricultural industry
- I have a Master’s in QHSE management and over 12 years of experience as a Quality Manager
- I’ve helped more than 15 companies implement ISO 9001, ISO 22000, ISO 22716, GMP, and other standards
- My clients include food producers, cosmetics manufacturers, laboratories, and service companies
- I believe quality systems should be simple, useful, and efficient
- Outside of work, I play piano and love learning something new every day
Let’s make ISO less about stress and more about success! 🙏